When considering which type of tablet press is more suitable for large-scale production, the choice largely depends on factors such as production volume, efficiency, precision, and operational costs. Rotary tablet presses are generally more suitable for large-scale production due to their high output capacity, consistent performance, and ability to handle a wide range of tablet sizes and shapes. They are designed for continuous operation, making them ideal for pharmaceutical, nutraceutical, and industrial applications where large quantities of tablets are required. In contrast, single-punch or eccentric presses are better suited for small-scale or laboratory use due to their lower output and slower operation. Below, we explore the key points that make rotary tablet presses the preferred choice for large-scale production.
Key Points Explained:
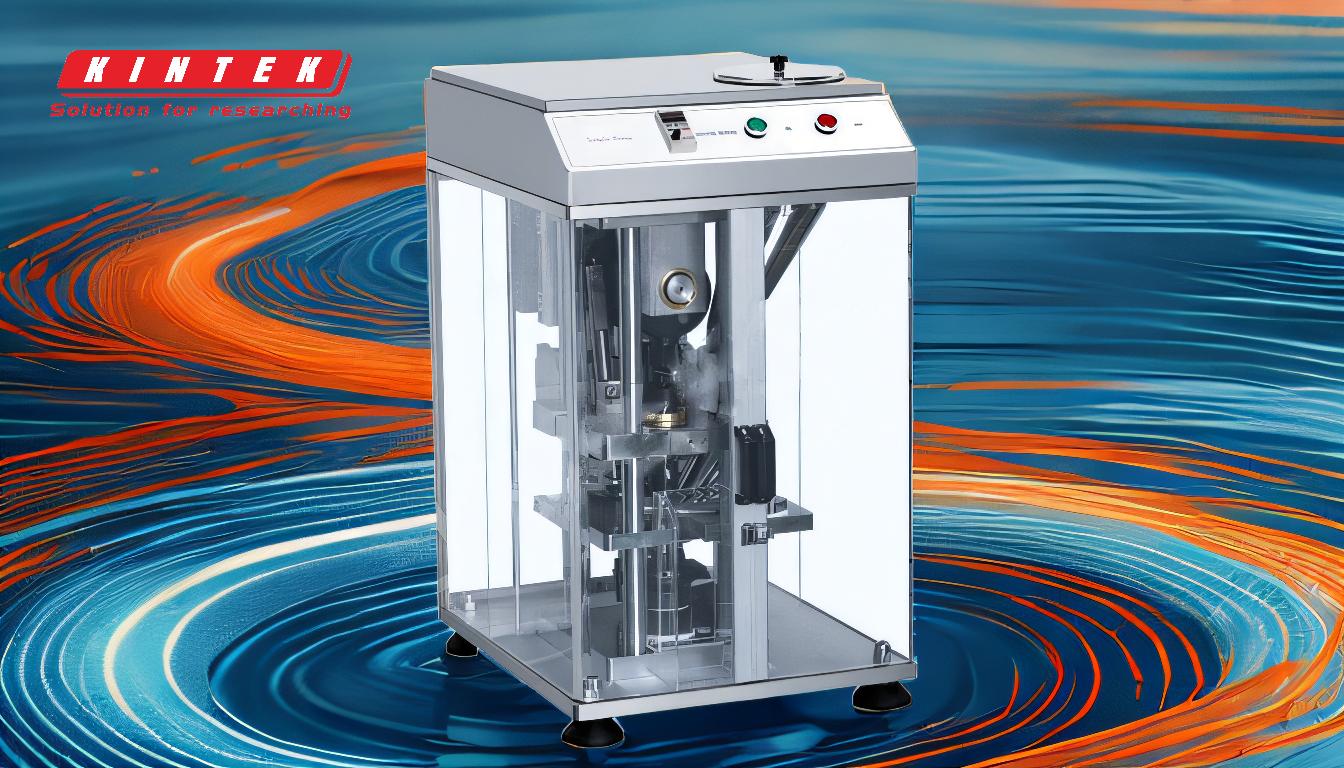
-
High Production Capacity:
- Rotary tablet presses are designed to produce thousands of tablets per hour, making them ideal for large-scale manufacturing. They feature multiple stations (dies and punches) that operate simultaneously, significantly increasing output compared to single-punch presses.
- For example, a rotary press with 55 stations can produce up to 500,000 tablets per hour, while a single-punch press might only produce a few hundred.
-
Continuous Operation:
- Rotary presses are engineered for continuous operation, which is essential for large-scale production. They can run for extended periods with minimal downtime, ensuring consistent output.
- Automated feeding systems and advanced control mechanisms further enhance their efficiency, reducing the need for manual intervention.
-
Versatility in Tablet Design:
- Rotary tablet presses can produce tablets of various shapes, sizes, and formulations, including multi-layer and coated tablets. This versatility is crucial for large-scale manufacturers who need to produce a wide range of products.
- Advanced models also allow for precise control over tablet weight, hardness, and thickness, ensuring uniformity and quality.
-
Reduced Labor Costs:
- The automation and high-speed operation of rotary presses reduce the need for manual labor, lowering operational costs. This is particularly beneficial for large-scale production, where labor costs can be significant.
- Automated systems for feeding, compression, and ejection streamline the production process, minimizing human error and improving efficiency.
-
Durability and Reliability:
- Rotary tablet presses are built to withstand the rigors of continuous, high-volume production. They are constructed from high-quality materials and designed for long-term reliability.
- Regular maintenance is straightforward, and many models come with self-diagnostic features to prevent breakdowns and ensure consistent performance.
-
Regulatory Compliance:
- Large-scale pharmaceutical and nutraceutical manufacturers must adhere to strict regulatory standards. Rotary presses are designed to meet these requirements, with features such as easy cleaning, validation protocols, and documentation capabilities.
- Compliance with Good Manufacturing Practices (GMP) is essential, and rotary presses are equipped to handle these demands effectively.
-
Cost-Effectiveness in the Long Run:
- While rotary tablet presses have a higher initial investment compared to single-punch presses, their high output and efficiency make them more cost-effective for large-scale production over time.
- The ability to produce large quantities with minimal downtime and labor costs results in a lower cost per tablet, which is a critical factor for manufacturers.
-
Integration with Other Systems:
- Rotary presses can be integrated with other production systems, such as coating machines, packaging lines, and quality control systems. This integration enhances overall production efficiency and ensures a seamless workflow.
- For example, tablets produced by a rotary press can be directly transferred to a coating machine for finishing, reducing handling and processing time.
In conclusion, rotary tablet presses are the most suitable option for large-scale production due to their high output, continuous operation, versatility, and cost-effectiveness. They are designed to meet the demands of modern manufacturing, ensuring consistent quality and efficiency. For manufacturers looking to scale up production, investing in a rotary tablet press is a strategic decision that offers long-term benefits.
Summary Table:
Feature | Rotary Tablet Press | Single-Punch Press |
---|---|---|
Production Capacity | Thousands of tablets per hour (e.g., 500,000/hour with 55 stations) | Limited to a few hundred tablets per hour |
Operation | Continuous operation with minimal downtime | Slower operation, not ideal for continuous use |
Versatility | Produces various shapes, sizes, and formulations (e.g., multi-layer, coated tablets) | Limited to simpler tablet designs |
Labor Costs | Reduced labor due to automation and high-speed operation | Higher labor requirements due to manual processes |
Durability | Built for continuous, high-volume production with long-term reliability | Less durable, suited for small-scale or lab use |
Regulatory Compliance | Designed to meet strict GMP standards with validation and documentation capabilities | Limited compliance features |
Cost-Effectiveness | Higher initial cost but lower cost per tablet over time | Lower initial cost but higher cost per tablet for large-scale production |
Integration | Easily integrated with coating, packaging, and quality control systems | Limited integration capabilities |
Ready to scale up your production? Contact us today to find the perfect rotary tablet press for your needs!