Chemical Vapor Deposition (CVD) is often preferred over Physical Vapor Deposition (PVD) due to its versatility, ability to produce high-purity and uniform coatings, and suitability for complex geometries. CVD operates at lower pressures and temperatures, reducing costs and simplifying the process. It excels in creating ultra-thin, durable layers with precise control over material properties, making it ideal for applications like electrical circuits and high-performance coatings. Additionally, CVD can deposit a wide range of materials, including ceramics and metals, and is not limited by line-of-sight constraints, enabling it to coat intricate shapes effectively. These advantages make CVD a more economical and efficient choice for many industrial applications.
Key Points Explained:
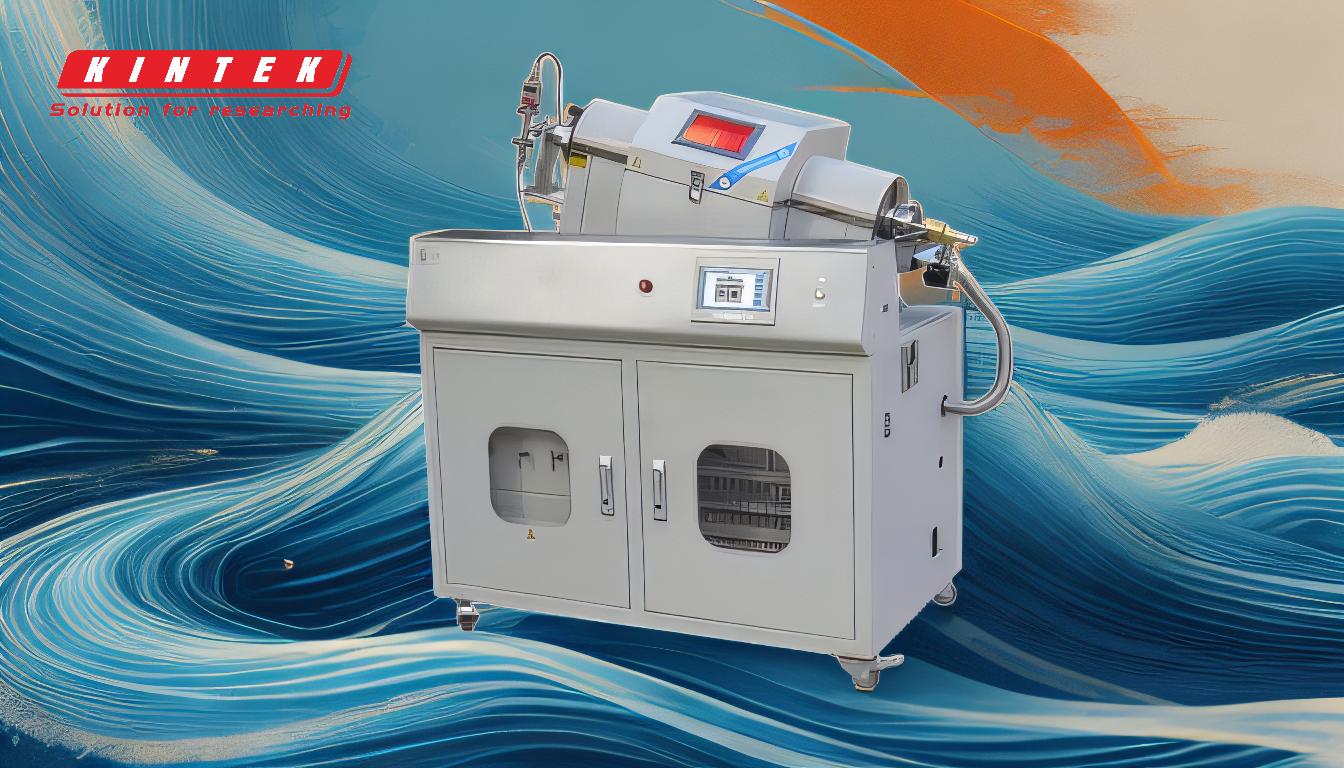
-
Versatility and Material Range:
- CVD can deposit a wide variety of materials, including ceramics, metals, and glass, making it highly versatile.
- It allows for the optimization of gases to achieve specific properties like corrosion resistance, abrasion resistance, or high purity.
-
High Purity and Uniformity:
- CVD produces films with high purity and uniformity, which are critical for applications requiring precise material properties.
- The process ensures dense and high-quality coatings with low residual stress and good crystallization.
-
Complex Geometry Coating:
- Unlike PVD, CVD is not limited by line-of-sight deposition, enabling it to coat complex shapes, holes, and deep recesses effectively.
- This makes CVD suitable for precision and intricate surfaces, such as those found in electrical circuits.
-
Lower Operating Costs:
- CVD operates at lower pressures and temperatures compared to PVD, reducing energy consumption and operational costs.
- The process is more economical, with high deposition rates and the ability to produce thick coatings.
-
Improved Performance and Control:
- CVD offers better thickness control, smoother surfaces, and enhanced electrical and thermal conductivity compared to other deposition methods.
- The properties of the deposited material can be finely tuned by adjusting deposition parameters, providing greater flexibility.
-
Environmental and Economic Benefits:
- CVD has a reduced CO2 footprint compared to other technologies, making it more environmentally friendly.
- The simplicity of the equipment and ease of operation further contribute to its cost-effectiveness and widespread adoption.
-
Durability and Stress Resistance:
- CVD coatings are durable and can withstand high-stress environments, extreme temperatures, and temperature variations.
- This makes CVD ideal for applications requiring long-lasting and reliable coatings.
In summary, CVD's ability to produce high-quality, uniform, and durable coatings on complex geometries, combined with its cost-effectiveness and environmental benefits, makes it a preferred choice over PVD for many industrial and manufacturing applications.
Summary Table:
Advantage | Description |
---|---|
Versatility | Deposits ceramics, metals, and glass; optimizes material properties. |
High Purity & Uniformity | Produces dense, high-quality coatings with precise control over material properties. |
Complex Geometry Coating | Coats intricate shapes, holes, and recesses without line-of-sight limitations. |
Lower Operating Costs | Operates at lower pressures and temperatures, reducing energy and operational costs. |
Improved Performance | Offers better thickness control, smoother surfaces, and enhanced conductivity. |
Environmental Benefits | Reduces CO2 footprint and simplifies equipment for cost-effective operations. |
Durability | Withstands high-stress environments, extreme temperatures, and temperature variations. |
Discover how CVD can optimize your industrial processes—contact us today for expert advice!