Chemical Vapor Deposition (CVD) is a widely used technique in materials science and engineering for creating high-quality, high-performance solid materials. It involves the chemical reaction of gaseous precursors to form a solid material on a substrate. CVD is favored for its ability to produce thin films and coatings with exceptional purity, uniformity, and control over composition and thickness. This method is essential in industries such as semiconductor manufacturing, optics, and protective coatings due to its versatility and precision. Below, we delve into the key reasons why CVD is extensively used and its advantages over other deposition techniques.
Key Points Explained:
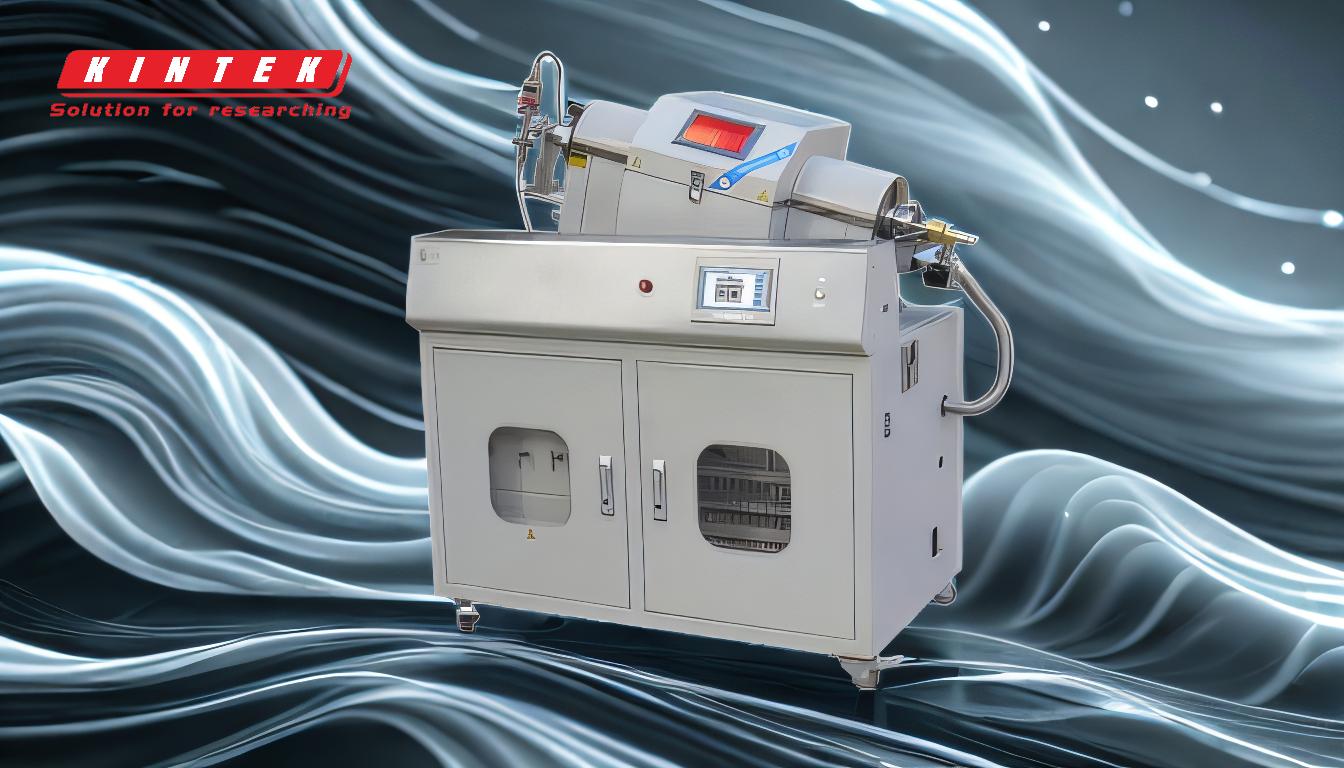
-
High-Quality Thin Films:
- CVD is renowned for producing thin films with excellent uniformity, density, and adhesion. The process allows for precise control over the deposition parameters, enabling the creation of films with tailored properties such as thickness, composition, and microstructure.
- This is particularly important in semiconductor manufacturing, where even minor defects or inconsistencies can significantly impact device performance.
-
Versatility in Material Deposition:
- CVD can deposit a wide range of materials, including metals, ceramics, polymers, and composites. This versatility makes it suitable for various applications, from creating conductive layers in microelectronics to producing wear-resistant coatings in industrial tools.
- The ability to deposit multiple materials in a single process (e.g., through sequential or co-deposition) further enhances its utility.
-
Superior Purity and Control:
- The gaseous precursors used in CVD are typically highly pure, resulting in deposited materials with minimal impurities. This is critical for applications requiring high-performance materials, such as in aerospace or medical devices.
- The process parameters, such as temperature, pressure, and gas flow rates, can be finely tuned to achieve the desired material properties.
-
Conformal Coatings:
- CVD excels at depositing uniform coatings on complex geometries and three-dimensional structures. This conformal coating capability is essential for applications like coating internal surfaces of pipes, intricate semiconductor devices, or optical components.
- Unlike physical vapor deposition (PVD), which often struggles with shadowing effects, CVD ensures even coverage on all exposed surfaces.
-
Scalability and Industrial Applicability:
- CVD processes can be scaled up for industrial production, making it a cost-effective solution for large-scale manufacturing. Techniques like plasma-enhanced CVD (PECVD) and low-pressure CVD (LPCVD) have been optimized for high-throughput applications.
- Its compatibility with existing manufacturing workflows further enhances its adoption in industries like electronics and automotive.
-
Enhanced Material Properties:
- Materials produced via CVD often exhibit superior mechanical, thermal, and electrical properties compared to those produced by other methods. For example, CVD-grown diamond films are used in cutting tools due to their exceptional hardness and thermal conductivity.
- The ability to engineer materials at the atomic or molecular level allows for the creation of advanced materials with unique functionalities.
-
Environmental and Safety Advantages:
- Modern CVD processes are designed to minimize waste and reduce the use of hazardous chemicals. Advances in precursor chemistry and reactor design have made CVD more environmentally friendly.
- Additionally, the closed-system nature of CVD reduces exposure to harmful byproducts, enhancing workplace safety.
-
Integration with Advanced Technologies:
- CVD is integral to the development of cutting-edge technologies such as nanotechnology, photovoltaics, and quantum computing. For instance, CVD is used to grow graphene and other two-dimensional materials, which are critical for next-generation electronic devices.
- Its ability to deposit materials at the nanoscale with high precision makes it indispensable for research and innovation.
In summary, CVD is a cornerstone technology in modern materials science due to its ability to produce high-quality, versatile, and precisely controlled materials. Its advantages in terms of purity, conformal coating, scalability, and integration with advanced technologies make it the preferred choice for a wide range of industrial and research applications. Whether in semiconductor fabrication, protective coatings, or nanotechnology, CVD continues to drive innovation and enable the development of next-generation materials and devices.
Summary Table:
Advantage | Description |
---|---|
High-Quality Thin Films | Produces uniform, dense, and well-adhered films with precise control. |
Versatility in Materials | Deposits metals, ceramics, polymers, and composites for diverse applications. |
Superior Purity and Control | Uses highly pure precursors for minimal impurities and tailored material properties. |
Conformal Coatings | Ensures even coverage on complex geometries and 3D structures. |
Scalability | Scales for industrial production with techniques like PECVD and LPCVD. |
Enhanced Material Properties | Delivers superior mechanical, thermal, and electrical properties. |
Environmental and Safety | Minimizes waste and reduces exposure to hazardous byproducts. |
Integration with Advanced Tech | Enables nanotechnology, photovoltaics, and quantum computing advancements. |
Ready to leverage CVD for your next project? Contact our experts today to get started!