Induction furnaces are widely used in industrial and manufacturing settings due to their energy efficiency, cleanliness, and precision. They are particularly valued for their ability to melt metals quickly and uniformly while minimizing contamination and energy consumption. Induction furnaces are versatile, capable of handling both ferrous and non-ferrous metals, and are suitable for a variety of applications, including alloy manufacturing, investment casting, and heat treatment processes. Their design, which uses electromagnetic induction to generate heat within the metal itself, ensures a controlled and pollution-free melting process. This makes them an environmentally friendly and cost-effective choice for modern foundries and industrial operations.
Key Points Explained:
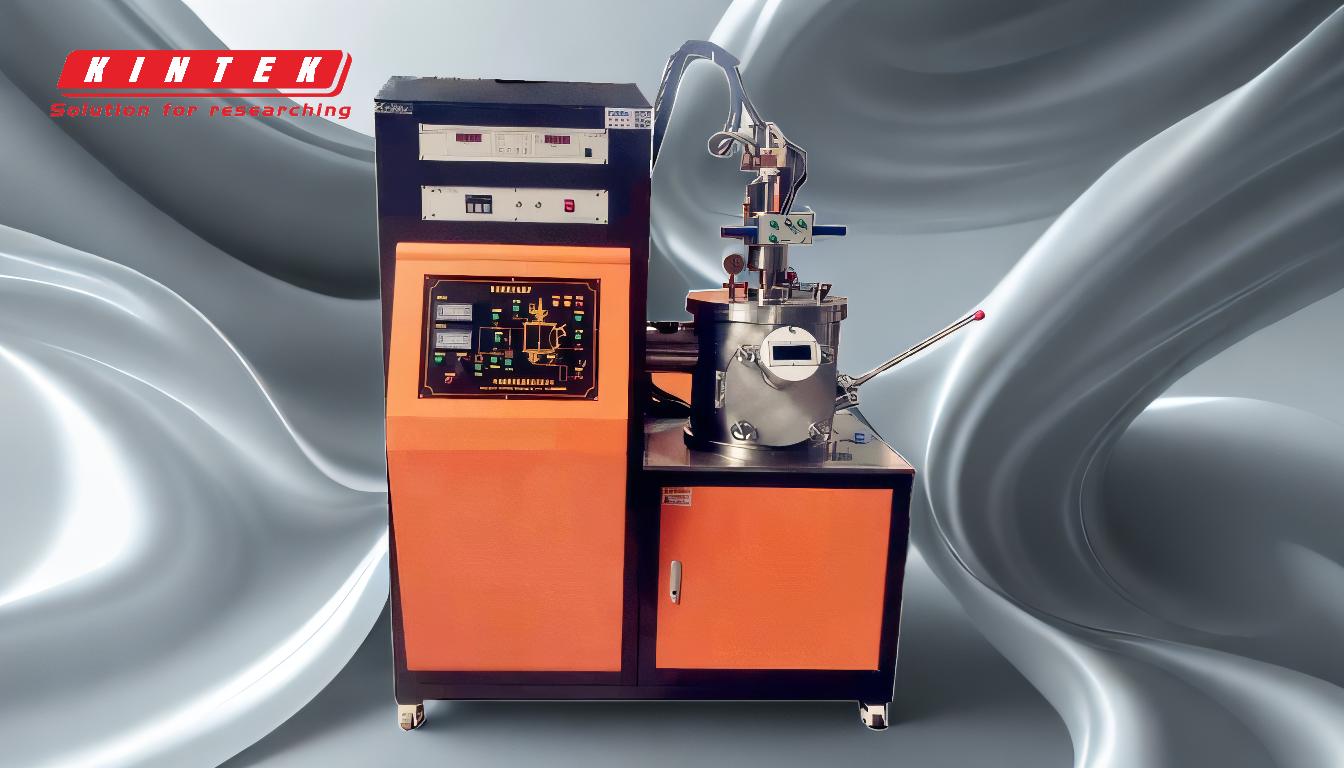
-
Energy Efficiency and Low Energy Consumption
- Induction furnaces are highly energy-efficient because they generate heat directly within the metal charge using electromagnetic induction. This reduces energy loss compared to traditional furnaces that rely on external heat sources like combustion or arcs.
- The process minimizes heat dissipation, ensuring that most of the energy is used for melting, which translates to lower operational costs and reduced carbon footprint.
-
Clean and Pollution-Free Operation
- Unlike combustion-based furnaces, induction furnaces do not produce dust, smoke, or other pollutants. This makes them environmentally friendly and compliant with stringent environmental regulations.
- The absence of combustion or arc heating also eliminates the risk of contamination from external sources, ensuring the purity of the melted metal.
-
Precise Temperature Control
- Induction furnaces offer superior temperature control, with minimal temperature differences between the core and surface of the metal. This precision is crucial for processes that require specific melting or heating conditions, such as alloy manufacturing or heat treatment.
- The ability to regulate heat accurately helps preserve valuable alloying elements, ensuring the quality and consistency of the final product.
-
Fast Heating Speed and High Production Efficiency
- Induction furnaces heat metals rapidly, significantly reducing melting times compared to traditional methods. This leads to higher production efficiency and throughput.
- The fast heating process also reduces oxidation and decarburization, which can degrade the quality of the metal.
-
Versatility in Applications
- Induction furnaces are suitable for a wide range of applications, including:
- Melting ferrous and non-ferrous metals (e.g., steel, aluminum, copper).
- Alloy manufacturing, where uniformity and flexibility are critical.
- Investment casting, shrink-fitting, annealing, and brazing.
- Heat treatment processes like quenching, tempering, and preheating.
- Their adaptability makes them a preferred choice in industries ranging from automotive to aerospace.
- Induction furnaces are suitable for a wide range of applications, including:
-
Improved Working Conditions
- The contained and controlled melting process of induction furnaces creates a cleaner and safer working environment.
- Workers are not exposed to harmful pollutants or extreme heat, improving overall workplace conditions and reducing health risks.
-
Material and Cost Savings
- Induction furnaces minimize material loss by reducing oxidation and preserving alloying elements. This leads to significant cost savings in raw materials.
- The precise control over the melting process also reduces wear and tear on forging dies and other equipment, further lowering operational costs.
-
Small Footprint and Ease of Regulation
- Induction furnaces are compact and require less space compared to traditional furnaces.
- The melting process is easy to regulate, allowing for consistent and repeatable results, which is essential for high-quality manufacturing.
In summary, induction furnaces are chosen for their efficiency, cleanliness, precision, and versatility. They provide a sustainable and cost-effective solution for modern industrial processes, making them indispensable in foundries and manufacturing facilities worldwide.
Summary Table:
Key Benefits | Details |
---|---|
Energy Efficiency | Generates heat directly within the metal, reducing energy loss. |
Clean Operation | Pollution-free, no dust or smoke, and compliant with environmental regulations. |
Precise Temperature Control | Minimal temperature differences, preserving alloying elements. |
Fast Heating Speed | Reduces melting times, increasing production efficiency. |
Versatility | Suitable for ferrous and non-ferrous metals, alloy manufacturing, and more. |
Improved Working Conditions | Cleaner, safer environment with reduced health risks. |
Cost Savings | Minimizes material loss and reduces operational costs. |
Compact Design | Small footprint and easy regulation for consistent results. |
Ready to enhance your industrial processes with induction furnaces? Contact us today to learn more!