Hydrogen is widely used in the sintering process due to its unique properties and benefits. It acts as a highly effective reducing agent, capable of stripping surface oxides and impurities like silica from alloys, particularly in stainless steel parts. This results in high-purity sintered products with superior mechanical properties and densities comparable to wrought parts. Additionally, hydrogen provides a high-quality atmosphere for sintering, improving furnace performance and enabling lower dew points, which enhance reducing conditions. Its ability to maximize part properties such as density and corrosion resistance makes it indispensable in high-temperature sintering processes.
Key Points Explained:
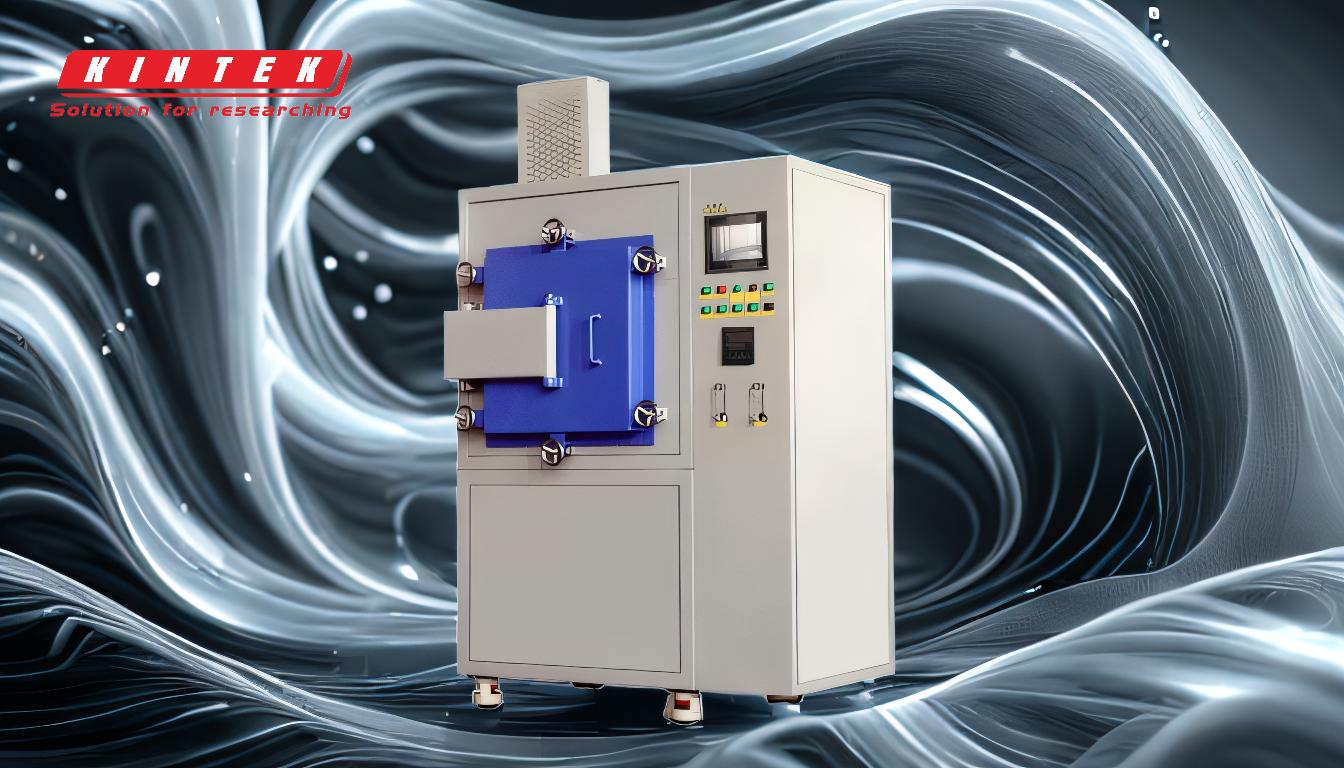
-
High Purity and Reducing Capabilities
- Hydrogen gas, with a purity level of >99.9995%, is ideal for sintering processes.
- It effectively reduces surface oxides and removes impurities like silica (SiO2) from alloys, ensuring cleaner and more uniform material properties.
- This reduction process is particularly critical for stainless steel parts, where surface oxides can compromise the final product's quality.
-
Enhanced Sintering Atmosphere
- Hydrogen creates a high-quality atmosphere within the sintering furnace, improving overall performance.
- It lowers the dew point, which enhances reducing conditions and minimizes the risk of oxidation during the sintering process.
- This controlled environment is essential for achieving consistent and high-quality sintered products.
-
Improved Mechanical Properties
- By removing impurities and reducing oxides, hydrogen sintering helps achieve high densities in the final product, comparable to wrought parts.
- This results in superior mechanical properties, such as increased strength, durability, and corrosion resistance.
- These improvements are critical for applications requiring high-performance materials.
-
Versatility in Sintering Applications
- Hydrogen can be used in various forms, including pure hydrogen, hydrogen/nitrogen gas mixtures, or dissociated ammonia, making it adaptable to different sintering processes.
- Its compatibility with a wide range of materials, including metals and ceramics, makes it a versatile choice for industrial sintering.
-
Economic and Operational Benefits
- The use of hydrogen can lead to better furnace performance, reducing operational costs and improving efficiency.
- Its ability to enhance reducing conditions and lower dew points minimizes the need for additional post-processing steps, saving time and resources.
-
Critical Role in Achieving High-Quality Parts
- Hydrogen sintering is essential for producing parts with high density, corrosion resistance, and mechanical integrity.
- It ensures the final product meets stringent quality standards, making it suitable for demanding applications in industries such as aerospace, automotive, and medical devices.
In summary, hydrogen's unique properties make it an indispensable component in the sintering process, offering benefits such as high purity, effective impurity reduction, and enhanced mechanical properties. Its ability to create a controlled and efficient sintering environment ensures the production of high-quality parts, making it a preferred choice for industrial applications.
Summary Table:
Key Benefit | Description |
---|---|
High Purity | Hydrogen (>99.9995%) reduces oxides and removes impurities like silica. |
Enhanced Atmosphere | Lowers dew points, improves reducing conditions, and minimizes oxidation risks. |
Improved Mechanical Properties | Achieves high density, strength, and corrosion resistance. |
Versatility | Compatible with metals, ceramics, and various gas mixtures. |
Economic Benefits | Reduces operational costs and post-processing needs. |
High-Quality Parts | Ensures parts meet stringent standards for aerospace, automotive, and medical. |
Elevate your sintering process with hydrogen—contact our experts today to learn more!