Graphene is grown on copper using Chemical Vapor Deposition (CVD) because copper serves as an ideal substrate for this process. CVD is widely used due to its simplicity, scalability, and cost-effectiveness, making it a preferred method for both research and industrial applications. Copper's catalytic properties, low carbon solubility, and ability to produce high-quality, single-layer graphene make it a suitable choice. Additionally, the ecological and economic advantages of CVD further enhance its appeal for graphene synthesis.
Key Points Explained:
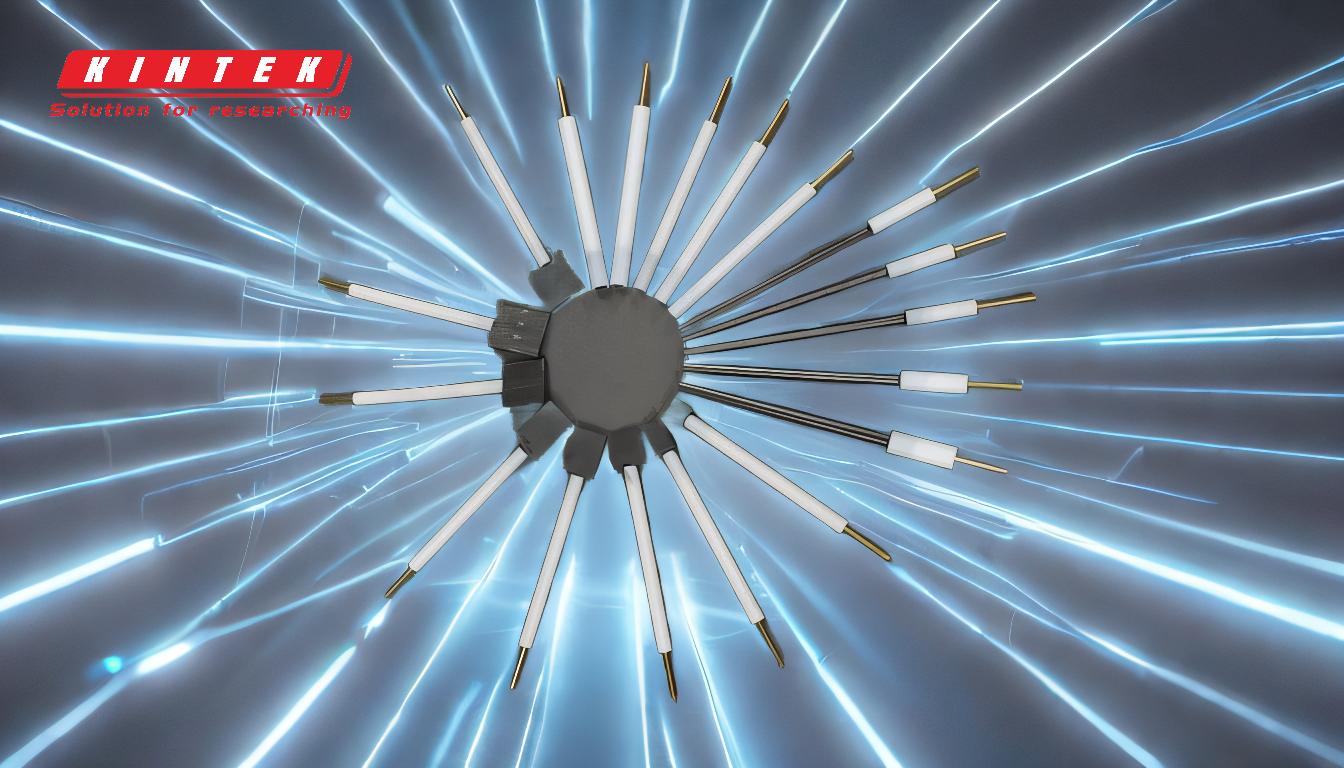
-
Chemical Vapor Deposition (CVD) as a Preferred Method:
- CVD is a popular technique for graphene growth due to its ease of setup in research laboratories and its successful long-term use in industrial settings.
- The method is scalable, allowing for the production of large-area graphene films, which is crucial for commercial applications.
- CVD is also considered environmentally friendly and cost-effective, making it a sustainable choice for graphene synthesis.
-
Copper's Catalytic Properties:
- Copper acts as an excellent catalyst for the decomposition of carbon-containing gases, such as methane, during the CVD process.
- This catalytic activity facilitates the formation of graphene layers on the copper surface, ensuring uniform and high-quality graphene growth.
-
Low Carbon Solubility in Copper:
- One of the key reasons for choosing copper as a substrate is its low carbon solubility.
- Unlike other metals, such as nickel, copper does not absorb significant amounts of carbon, which prevents the formation of multiple graphene layers and ensures the production of single-layer graphene.
-
High-Quality Graphene Production:
- The use of copper in CVD results in the synthesis of high-quality, defect-free graphene with excellent electrical and mechanical properties.
- This is essential for applications in electronics, sensors, and other advanced technologies where graphene's unique properties are required.
-
Ecological and Economic Advantages:
- The CVD process, when combined with copper substrates, offers ecological benefits by minimizing waste and reducing the need for harmful chemicals.
- Economically, the use of copper is advantageous due to its relatively low cost and availability, making it a practical choice for large-scale graphene production.
In summary, the combination of CVD and copper substrates provides a reliable, scalable, and cost-effective method for producing high-quality graphene, making it a preferred approach in both research and industrial applications.
Summary Table:
Key Aspect | Details |
---|---|
CVD Advantages | Simple, scalable, cost-effective, eco-friendly, and suitable for industries |
Copper's Role | Catalytic properties, low carbon solubility, and uniform graphene growth |
Graphene Quality | High-quality, defect-free, single-layer graphene with excellent properties |
Ecological & Economic Benefits | Minimizes waste, reduces harmful chemicals, and uses affordable copper |
Interested in graphene production solutions? Contact our experts today to learn more!