Helium is needed to produce an inert atmosphere for welding because it is chemically inert, meaning it does not react with other elements or compounds under normal conditions. This property makes it ideal for shielding the weld area from atmospheric gases like oxygen and nitrogen, which can cause oxidation, porosity, and other defects in the weld. Helium's high thermal conductivity also helps in achieving deeper penetration and faster welding speeds, especially in processes like TIG (Tungsten Inert Gas) welding. Unlike hydrogen, which can cause hydrogen embrittlement in high-carbon materials, helium does not introduce any harmful effects, making it a safer and more reliable choice for creating an inert welding environment.
Key Points Explained:
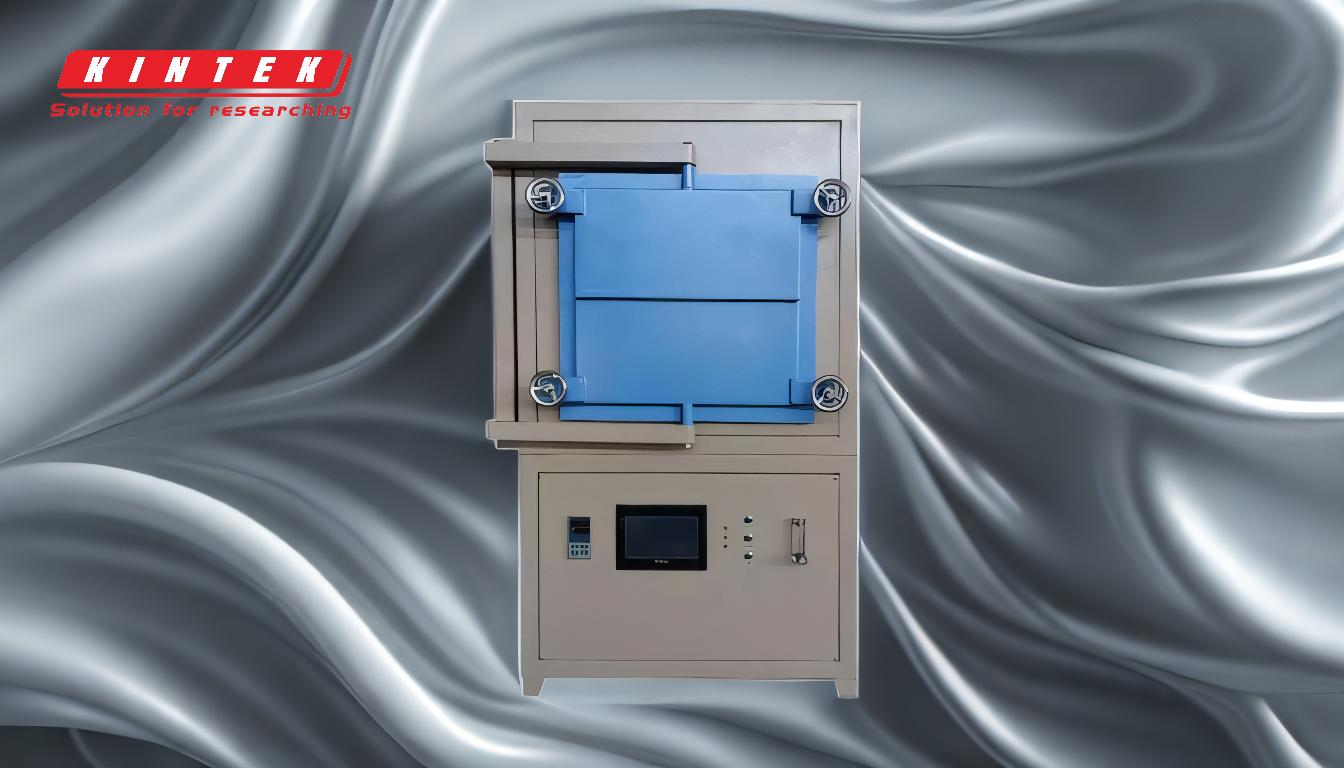
-
Chemical Inertness of Helium:
- Helium is a noble gas, which means it is chemically inert and does not react with other elements or compounds. This property is crucial in welding because it prevents the formation of oxides, nitrides, and other undesirable compounds that can weaken the weld.
- In contrast, gases like oxygen and nitrogen, which are present in the atmosphere, can react with the molten metal during welding, leading to defects such as porosity, brittleness, and reduced mechanical strength.
-
Shielding the Weld Pool:
- During welding, the weld pool is highly susceptible to contamination from atmospheric gases. Helium is used to create a protective shield around the weld pool, effectively displacing these gases and preventing them from interacting with the molten metal.
- This shielding effect is particularly important in processes like TIG welding, where even small amounts of contamination can significantly affect the quality of the weld.
-
Thermal Conductivity and Weld Penetration:
- Helium has a high thermal conductivity, which allows it to transfer heat more efficiently than other shielding gases like argon. This property results in deeper weld penetration and faster welding speeds, making helium an excellent choice for welding thick materials or when high welding speeds are required.
- The increased heat input provided by helium can also improve the fluidity of the weld pool, leading to better fusion and a more uniform weld bead.
-
Comparison with Hydrogen:
- While hydrogen is sometimes used in welding for its deoxidizing properties, it can cause hydrogen embrittlement, especially in high-carbon steels. This phenomenon occurs when hydrogen atoms diffuse into the metal, leading to cracking and reduced ductility.
- Helium, on the other hand, does not introduce any such risks, making it a safer and more reliable option for creating an inert atmosphere in welding.
-
Applications in Specific Welding Processes:
- Helium is commonly used in TIG welding, particularly for welding non-ferrous metals like aluminum and magnesium, where its high thermal conductivity and inert nature are highly beneficial.
- It is also used in combination with argon in gas mixtures to optimize the welding process, balancing the benefits of both gases to achieve the desired weld characteristics.
-
Economic and Practical Considerations:
- While helium is more expensive than other shielding gases like argon, its unique properties often justify the cost, especially in applications where weld quality and performance are critical.
- The availability of helium can also be a consideration, as it is a finite resource. However, its effectiveness in creating an inert atmosphere for welding makes it an indispensable choice in many industrial applications.
In summary, helium is essential for producing an inert atmosphere in welding due to its chemical inertness, ability to shield the weld pool, high thermal conductivity, and safety compared to other gases like hydrogen. These properties make helium a preferred choice for achieving high-quality welds, particularly in demanding applications and processes.
Summary Table:
Property | Benefits in Welding |
---|---|
Chemical Inertness | Prevents oxidation, porosity, and defects by shielding the weld pool from atmospheric gases. |
High Thermal Conductivity | Enables deeper penetration and faster welding speeds, ideal for thick materials. |
Safety | Safer than hydrogen, as it avoids risks like hydrogen embrittlement. |
Applications | Commonly used in TIG welding for non-ferrous metals like aluminum and magnesium. |
Cost vs. Performance | Higher cost justified by superior weld quality and performance in critical applications. |
Interested in optimizing your welding process with helium? Contact our experts today to learn more!