Hydrogen gas is widely used in annealing furnaces due to its unique properties, such as high thermal conductivity, strong deoxidizing capabilities, and its ability to create a controlled atmosphere that prevents oxidation and contamination. It is particularly effective for annealing low carbon steels, stainless steels, and other materials, as it ensures a clean and efficient process. However, its use requires careful control to avoid issues like hydrogen embrittlement or decarburization in high-carbon materials. The high heat transfer coefficient of hydrogen also makes the annealing process more efficient, especially for heat-treating cast and welded components.
Key Points Explained:
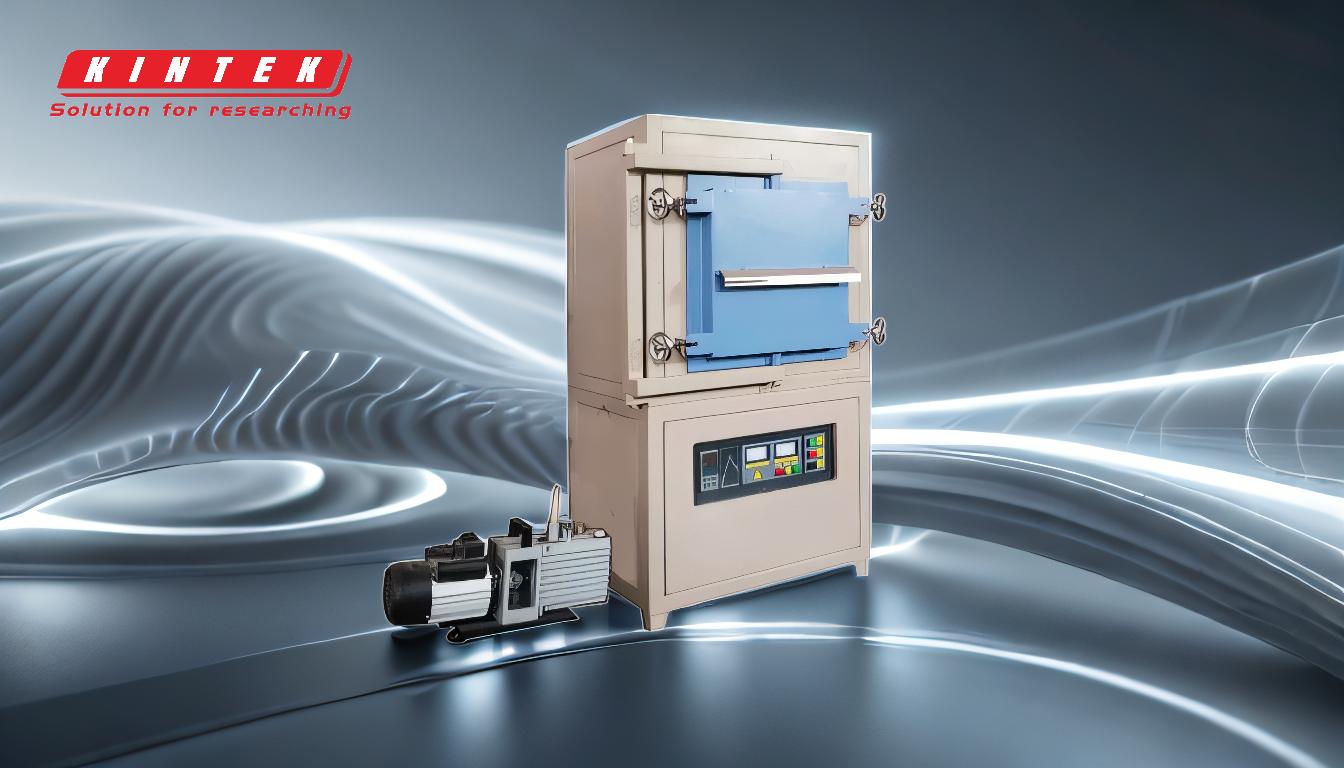
-
High Thermal Conductivity:
- Hydrogen has a thermal conductivity that is seven times higher than that of air. This property allows for faster and more uniform heat transfer during the annealing process, making it more efficient and effective.
- The high heat transfer coefficient ensures that the material being annealed reaches the desired temperature quickly and uniformly, reducing processing time and energy consumption.
-
Deoxidizing Properties:
- Hydrogen acts as a strong deoxidizer, which is crucial in preventing oxidation of the material during annealing. This is particularly important for metals like stainless steel and low carbon steels, where oxidation can degrade the material's properties.
- In a dry state, hydrogen can effectively remove oxygen from the surface of the material, ensuring a clean and oxide-free finish.
-
Controlled Atmosphere:
- Hydrogen is used to create a controlled atmosphere in the annealing furnace, which prevents contamination from other gases like oxygen or nitrogen. This is essential for maintaining the integrity and quality of the material being annealed.
- The controlled atmosphere is particularly beneficial for processes like sintering tungsten carbide, metal powder components, and direct reduction of metal ores.
-
Prevention of Oxidation:
- By using hydrogen as a protective atmosphere, the annealing process can be carried out without the risk of oxidation. This is especially important for materials that are sensitive to oxidation, such as stainless steels and magnetic alloys.
- The absence of oxygen in the furnace atmosphere ensures that the material remains clean and free from surface defects.
-
Efficiency in Heat Treatment:
- The high thermal conductivity and controlled atmosphere provided by hydrogen make the annealing process more efficient. This is particularly beneficial for heat-treating cast and welded components, where uniform heating is critical.
- The efficiency of hydrogen in heat transfer reduces the overall processing time, leading to cost savings and improved productivity.
-
Challenges and Limitations:
- Hydrogen Embrittlement: Hydrogen can cause embrittlement in high-carbon steels and other materials, leading to reduced ductility and potential failure. This is a significant concern and requires careful control of the annealing process.
- Decarburization: In high-carbon materials, hydrogen can lead to decarburization, where carbon is removed from the surface, weakening the material. This is particularly problematic in high-carbon steels.
- Moisture Content: The effectiveness of hydrogen as a deoxidizer is limited by its moisture content. Dry hydrogen is required to achieve the desired deoxidizing effect.
-
Applications in Various Industries:
- Hydrogen annealing furnaces are used in a wide range of industries, including the processing of hard alloys, ceramic materials, magnetic materials, and rare refractory metals.
- They are also used for sintering powder metallurgy, semiconductor alloy processing, and the annealing and purification of glass parts for sealing metal parts.
-
Operational Characteristics of Hydrogen Annealing Furnaces:
- These furnaces are equipped with automatic and manual control systems, allowing for precise temperature regulation.
- They can reach maximum temperatures of up to 1600℃, with automatic temperature control precision of ±1℃ and temperature uniformity of ±3℃ to ±10℃, depending on user requirements.
- The ability to store multiple heating programs makes these furnaces versatile and capable of meeting various process requirements.
In summary, hydrogen gas is used in annealing furnaces due to its high thermal conductivity, deoxidizing properties, and ability to create a controlled atmosphere that prevents oxidation and contamination. While it offers significant advantages in terms of efficiency and material quality, its use must be carefully managed to avoid issues like hydrogen embrittlement and decarburization. The versatility and precision of hydrogen annealing furnaces make them indispensable in various industrial applications.
Summary Table:
Property | Benefits |
---|---|
High Thermal Conductivity | 7x higher than air; ensures faster, uniform heat transfer. |
Deoxidizing Properties | Prevents oxidation, ideal for stainless steel and low carbon steels. |
Controlled Atmosphere | Prevents contamination, essential for sintering and metal powder processes. |
Prevention of Oxidation | Ensures clean, oxide-free finishes for sensitive materials. |
Efficiency in Heat Treatment | Reduces processing time and energy consumption. |
Challenges | Risk of hydrogen embrittlement and decarburization in high-carbon steels. |
Ready to optimize your annealing process with hydrogen furnaces? Contact our experts today to learn more!