Hydrogen is widely used in sintering due to its unique properties that enhance the quality and performance of the final product. Its high purity (>99.9995%) ensures a clean environment for sintering, which is crucial for achieving superior mechanical properties and surface finish. Hydrogen reduces surface oxides, strips impurities like silica, and prevents metal oxidation, all of which contribute to better furnace atmosphere performance. Additionally, hydrogen's ability to remove carbon residues and other contaminants during the sintering process ensures the production of high-quality sintered parts. The use of hydrogen in a sintering furnace is particularly beneficial for materials that require precise control over their microstructure and surface characteristics.
Key Points Explained:
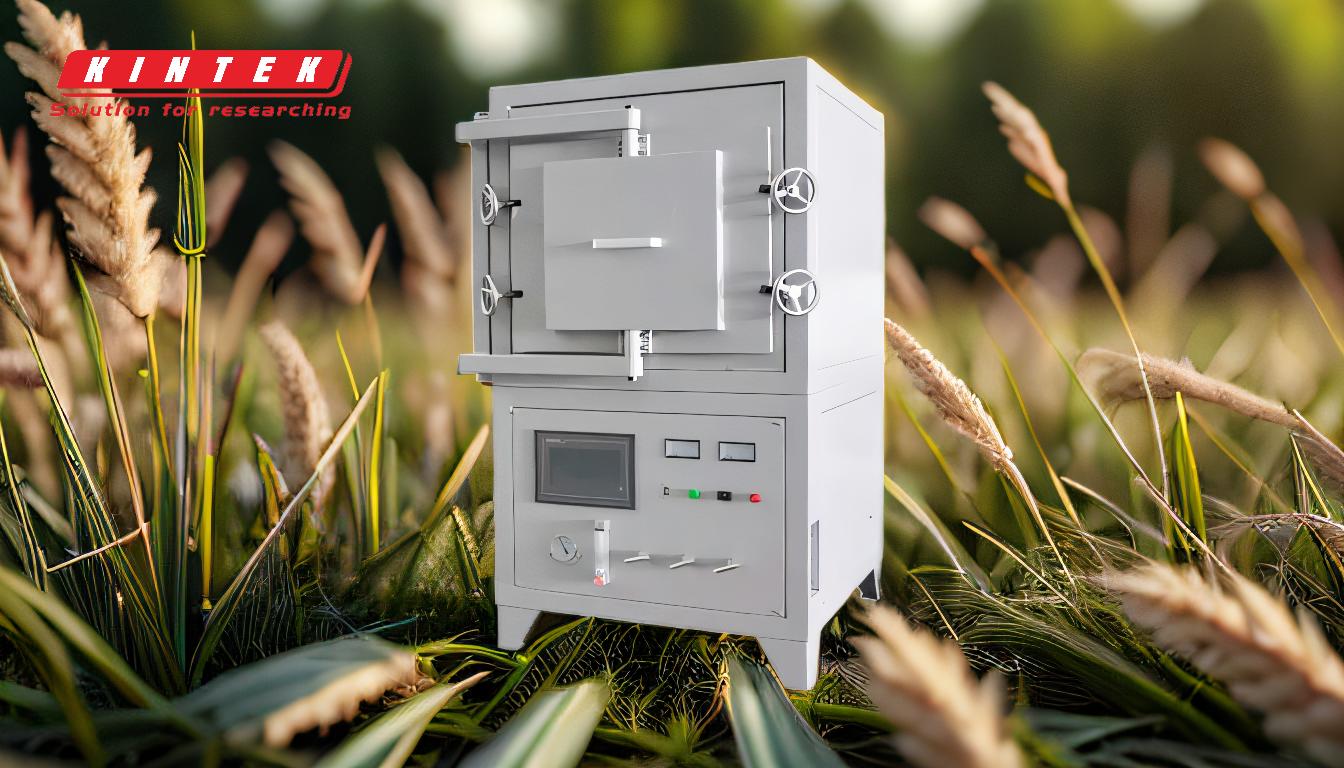
-
High Purity of Hydrogen:
- Hydrogen used in sintering has a purity level of over 99.9995%, making it ideal for creating a clean and controlled atmosphere within the sintering furnace.
- This high purity is essential for sintering materials that are sensitive to impurities, ensuring the final product has excellent mechanical properties and a bright surface finish.
-
Reduction of Surface Oxides:
- Hydrogen acts as a reducing agent, effectively removing surface oxides from the material being sintered.
- This oxide reduction is critical for improving the material's surface quality and preventing defects that could compromise the part's performance.
-
Stripping Impurities:
- Hydrogen helps strip impurities such as silica from the alloy, which can negatively affect the sintering process.
- By removing these impurities, hydrogen ensures a cleaner and more efficient sintering process, leading to higher-quality sintered parts.
-
Prevention of Metal Oxidation:
- Metal oxidation during sintering can reduce the powders' aggregation ratio, leading to weaker and less durable parts.
- Hydrogen creates a protective atmosphere that prevents oxidation, ensuring the material retains its desired properties and structural integrity.
-
Superior Mechanical Qualities:
- The use of hydrogen in sintering results in parts with superior mechanical qualities, such as increased strength and durability.
- This is particularly important for applications where the sintered parts are subjected to high stress or harsh environments.
-
Bright Surface Finish:
- Hydrogen contributes to a bright and smooth surface finish on sintered parts, which is often a requirement for aesthetic or functional purposes.
- This finish is achieved by maintaining a clean and controlled atmosphere within the sintering furnace.
-
Role of Sintering Furnace:
- The sintering furnace plays a crucial role in the sintering process by providing the necessary high temperatures and controlled atmosphere.
- It ensures that the sintering process is carried out efficiently, resulting in parts with the desired properties and performance.
-
Environmental and Efficiency Benefits:
- Using hydrogen in sintering not only improves the quality of the final product but also enhances the efficiency of the manufacturing process.
- It helps reduce harmful by-products and ensures a more environmentally friendly sintering process.
In summary, hydrogen is used in sintering because of its ability to create a high-purity, reducing atmosphere that enhances the quality, performance, and appearance of sintered parts. Its role in preventing oxidation, removing impurities, and improving mechanical properties makes it an indispensable component in the sintering process, particularly when used in conjunction with a sintering furnace.
Summary Table:
Key Benefits of Hydrogen in Sintering | Details |
---|---|
High Purity (>99.9995%) | Ensures a clean, controlled atmosphere for superior mechanical properties and surface finish. |
Reduction of Surface Oxides | Removes oxides to improve surface quality and prevent defects. |
Stripping Impurities | Eliminates silica and other contaminants for cleaner sintering. |
Prevention of Metal Oxidation | Protects material integrity by preventing oxidation. |
Superior Mechanical Qualities | Enhances strength and durability of sintered parts. |
Bright Surface Finish | Achieves smooth, bright finishes for aesthetic and functional purposes. |
Environmental and Efficiency Benefits | Reduces harmful by-products and improves process efficiency. |
Learn how hydrogen can optimize your sintering process—contact us today for expert advice!