Controlling the atmosphere during sintering is essential to achieve the desired properties of the sintered material. The sintering atmosphere directly influences the chemical and physical processes occurring during sintering, such as oxidation, reduction, and diffusion. By selecting an appropriate atmosphere—whether inert, protective, or reducing—manufacturers can prevent unwanted reactions, such as oxidation, and promote beneficial ones, such as the reduction of surface oxides. This ensures the final product has the required mechanical, thermal, and chemical properties. Additionally, the atmosphere affects the consistency of temperature during sintering, which is critical for controlling grain boundary and bulk diffusion, ultimately determining the material's microstructure and performance.
Key Points Explained:
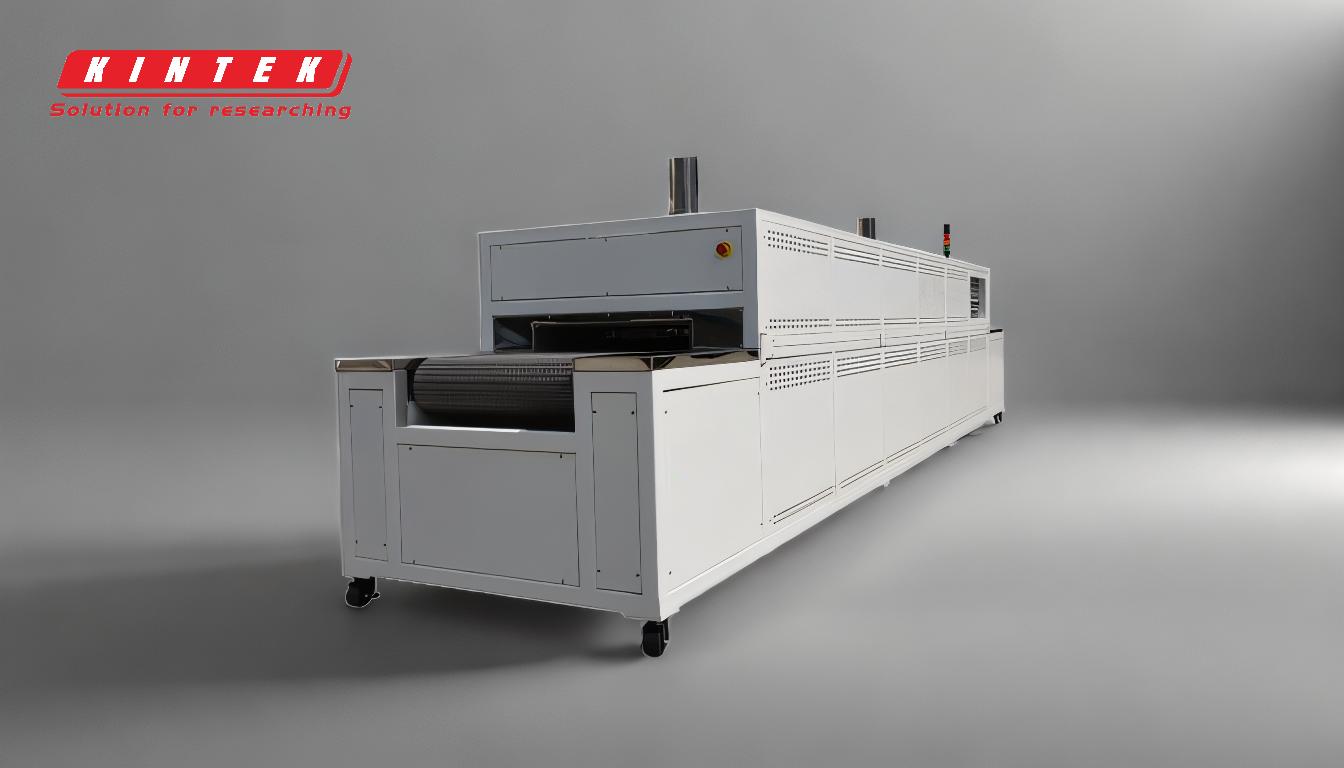
-
Prevention of Oxidation and Contamination:
- Sintering often involves metallic compounds that are prone to oxidation when exposed to air at high temperatures. Oxidation can degrade the material's properties, such as strength and ductility.
- An inert or protective atmosphere (e.g., argon, nitrogen) prevents oxidation by excluding oxygen from the sintering environment.
- A reducing atmosphere (e.g., hydrogen) can actively reduce surface oxides, ensuring a clean and oxide-free surface, which is critical for achieving strong interparticle bonding.
-
Control of Chemical Reactions:
- The sintering atmosphere influences the chemical reactions that occur during the process. For example, in a reducing atmosphere, hydrogen can react with oxides on the powder surfaces, converting them back to pure metal.
- This control is particularly important for materials like tungsten, molybdenum, and certain ceramics, where oxide formation can significantly alter the material's properties.
-
Optimization of Diffusion Processes:
- Sintering relies on diffusion mechanisms, such as grain boundary diffusion and bulk diffusion, to achieve densification and bonding between particles.
- The atmosphere affects the rate and effectiveness of these diffusion processes. For instance, a reducing atmosphere can enhance diffusion by removing oxide barriers, while an inert atmosphere ensures consistent diffusion without introducing impurities.
-
Temperature Consistency and Control:
- The sintering atmosphere helps maintain consistent temperature profiles, especially during critical phases like heating from 900°C to the top temperature, holding at the peak temperature, and cooling back to 900°C.
- Consistent temperature control is vital for achieving uniform microstructures and avoiding defects such as warping or cracking.
-
Achieving Desired Material Properties:
- The choice of sintering atmosphere directly impacts the final properties of the sintered material, including density, strength, hardness, and thermal conductivity.
- For example, sintering in a hydrogen atmosphere can improve the density and mechanical properties of certain metals by promoting better particle bonding and reducing porosity.
-
Cost-Effectiveness and Efficiency:
- Selecting the right atmosphere can optimize the sintering process, reducing energy consumption and material waste.
- For instance, using a reducing atmosphere can eliminate the need for additional post-sintering treatments to remove oxides, saving time and resources.
-
Material-Specific Requirements:
- Different materials require specific sintering atmospheres. For example:
- Inert atmospheres are suitable for materials like titanium and zirconia, which are highly reactive with oxygen.
- Reducing atmospheres are ideal for metals like copper and iron, where oxide reduction is necessary for optimal sintering.
- Understanding these requirements ensures the sintering process is tailored to the material, yielding the best results.
- Different materials require specific sintering atmospheres. For example:
In summary, controlling the sintering atmosphere is critical for preventing oxidation, optimizing chemical reactions, ensuring consistent temperature profiles, and achieving the desired material properties. It also enhances process efficiency and cost-effectiveness, making it an indispensable aspect of sintering technology.
Summary Table:
Key Factor | Impact on Sintering |
---|---|
Oxidation Prevention | Inert or protective atmospheres (e.g., argon, nitrogen) prevent oxidation. |
Chemical Reaction Control | Reducing atmospheres (e.g., hydrogen) convert oxides to pure metal. |
Diffusion Optimization | Enhances grain boundary and bulk diffusion for better densification. |
Temperature Consistency | Ensures uniform heating and cooling, preventing defects like warping. |
Material Properties | Influences density, strength, hardness, and thermal conductivity. |
Cost-Effectiveness | Reduces energy consumption and eliminates post-sintering treatments. |
Material-Specific Requirements | Tailors atmosphere to materials like titanium, zirconia, copper, and iron. |
Ready to optimize your sintering process? Contact our experts today for tailored solutions!