Nitrogen is widely used in heat treatment processes due to its ability to create a controlled atmosphere that prevents oxidation and decarburization of metal parts. It acts as a blanketing gas, purging existing atmospheres, and can serve as a carrier gas for carbon-controlled environments. While not completely inert, nitrogen is often mixed with small amounts of hydrogen to enhance its protective properties. This combination ensures a stable and controlled environment, crucial for achieving desired material properties during heat treatment.
Key Points Explained:
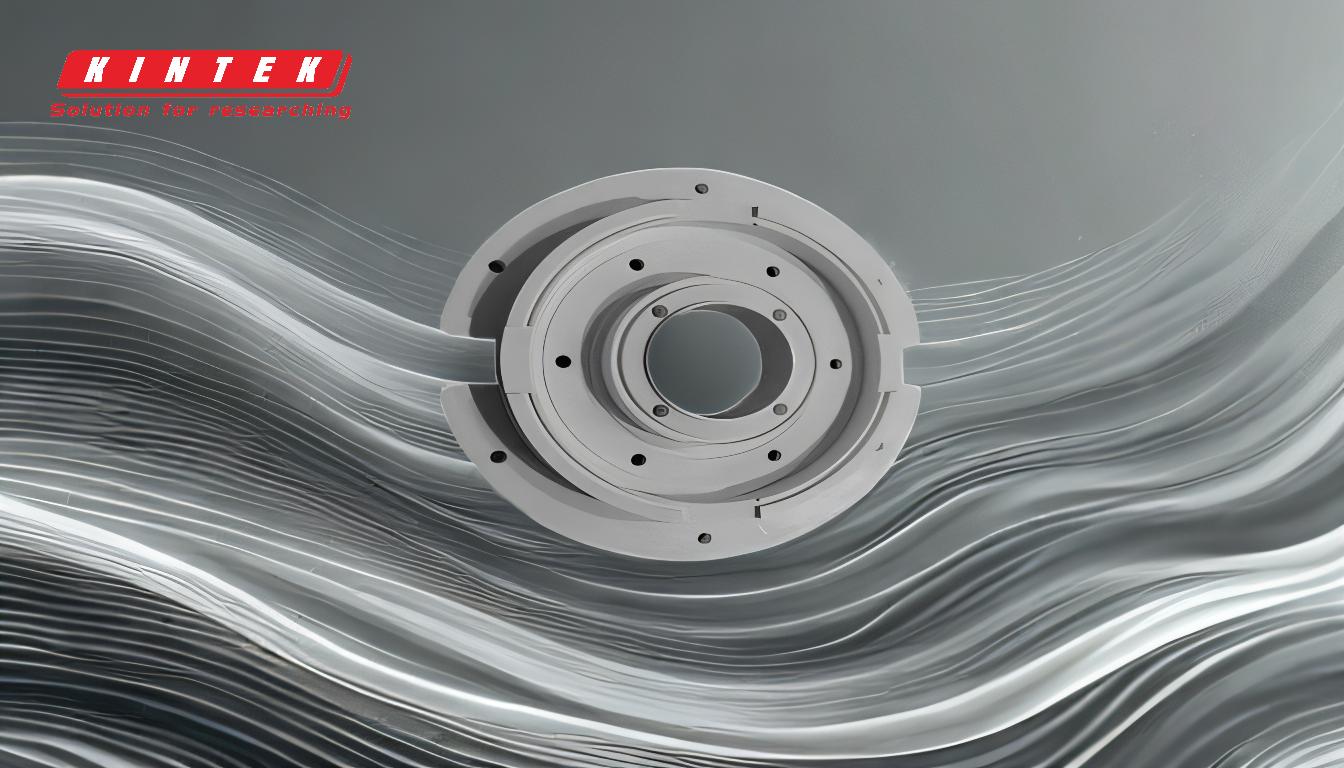
-
Blanketing Effect of Nitrogen
- Nitrogen creates a protective layer around the part being heat treated, shielding it from exposure to oxygen and other reactive gases.
- This prevents oxidation, which can lead to surface degradation, and decarburization, which weakens the material by reducing carbon content.
- The blanketing effect is essential for maintaining the integrity and quality of the treated part.
-
Purging Existing Atmospheres
- Nitrogen is used to displace unwanted gases, such as oxygen, from the heat treatment chamber.
- This ensures a clean and controlled environment, free from contaminants that could negatively affect the heat treatment process.
- Purging is particularly important in processes like annealing, where precise control over the atmosphere is critical.
-
Carrier Gas for Carbon-Controlled Atmospheres
- Nitrogen can act as a carrier gas for carbon-rich atmospheres, facilitating the introduction of carbon into the material during processes like carburizing.
- This helps achieve the desired surface hardness and wear resistance in treated parts.
- The use of nitrogen as a carrier gas ensures uniform distribution of carbon, leading to consistent results.
-
Nitrogen's Limited Inertness
- While nitrogen is often referred to as an inert gas, it is not completely inert and can react under certain conditions.
- To enhance its protective properties, nitrogen is typically delivered with a low dew point (between -75°F and -110°F) to minimize moisture content.
- This reduces the risk of unwanted reactions during heat treatment.
-
Hydrogen Blending for Enhanced Performance
- Nitrogen is often mixed with hydrogen in a 90/10 blend to improve its effectiveness as a protective atmosphere.
- Hydrogen helps reduce surface oxides and enhances the overall quality of the treated part.
- Recent guidelines recommend limiting hydrogen content to 3% or less to ensure the gas mixture remains inert and safe.
-
Importance of Controlled Atmospheres
- The use of nitrogen and nitrogen-hydrogen blends ensures a stable and controlled environment during heat treatment.
- This is critical for achieving consistent material properties, such as hardness, strength, and durability.
- Controlled atmospheres also minimize the risk of defects, ensuring high-quality outcomes in industrial applications.
By understanding these key points, it becomes clear why nitrogen is a preferred choice in heat treatment processes. Its ability to create a controlled, protective environment makes it indispensable for achieving optimal results in various industrial applications.
Summary Table:
Key Role of Nitrogen in Heat Treatment | Benefits |
---|---|
Blanketing Effect | Prevents oxidation and decarburization, ensuring part integrity. |
Purging Existing Atmospheres | Displaces oxygen and contaminants for a clean environment. |
Carrier Gas for Carbon-Controlled Atmospheres | Ensures uniform carbon distribution for hardness and wear resistance. |
Limited Inertness | Delivered with low dew point to minimize moisture and reactions. |
Hydrogen Blending | Enhances protective properties by reducing surface oxides. |
Controlled Atmospheres | Achieves consistent material properties and minimizes defects. |
Optimize your heat treatment process with nitrogen—contact our experts today to learn more!