Plasma is a critical component in the sputtering process, primarily because it enables the efficient transfer of energy to the target material, facilitating the deposition of thin films. The plasma is created by ionizing inert gas atoms, such as argon, which then collide with the target material, dislodging atoms that subsequently deposit onto a substrate. This process is enhanced by the ionization of gas atoms, which creates a high-energy environment necessary for sputtering. The plasma also plays a role in maintaining a stable and controlled environment within the deposition chamber, ensuring consistent and high-quality thin film deposition.
Key Points Explained:
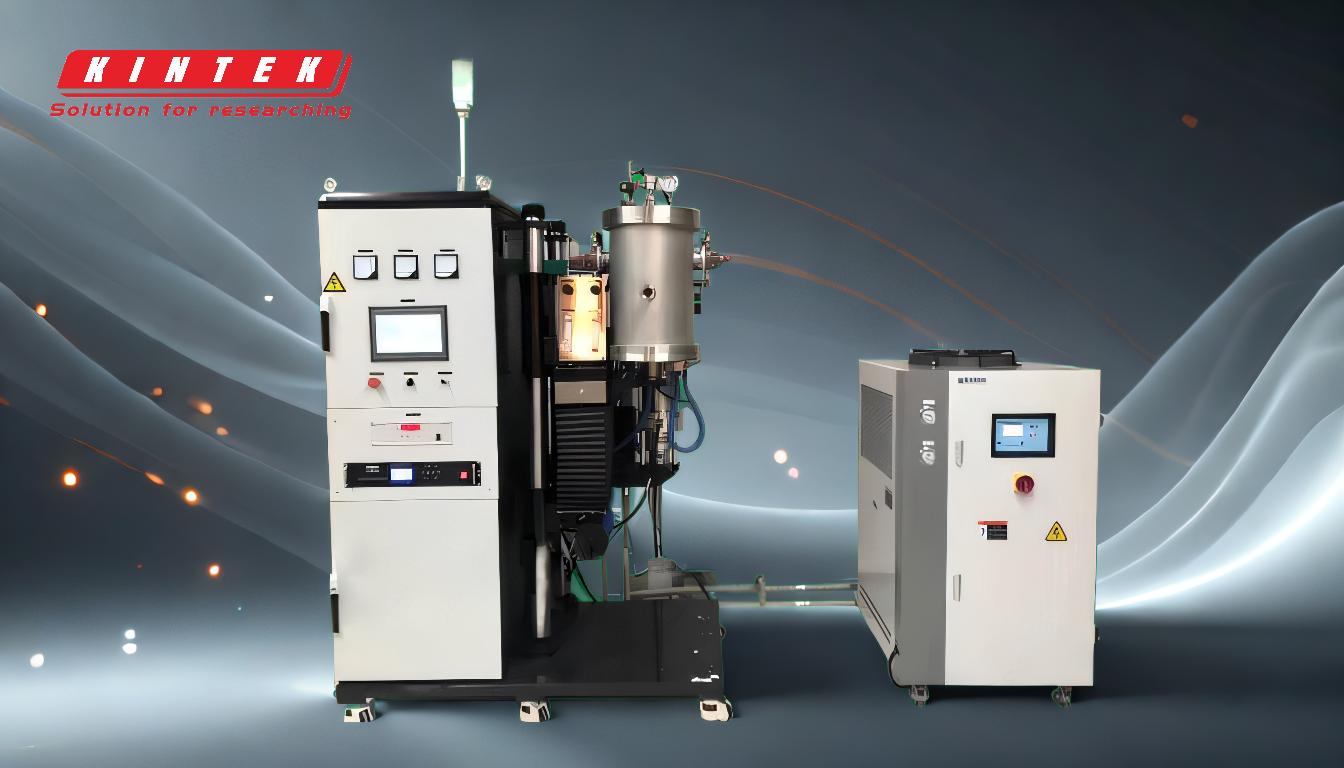
-
Creation of Plasma:
- Plasma is generated by ionizing inert gas atoms, such as argon, within the deposition chamber. This ionization process is typically achieved through the application of an electric field or radio frequency (RF) energy.
- The ionization of gas atoms results in the formation of positively charged ions and free electrons. When these ions recombine with electrons, they release energy in the form of light, producing the characteristic plasma glow observed during sputtering.
-
Role of Plasma in Sputtering:
- The primary role of plasma in sputtering is to provide the energy necessary to dislodge atoms from the target material. The ionized gas atoms (plasma) collide with the target material, transferring kinetic energy that is sufficient to knock atoms off the surface.
- These dislodged atoms are then vaporized and travel through the vacuum chamber, eventually condensing onto the substrate to form a thin film.
-
Energy Transfer and Deposition:
- The plasma ensures that the energy transfer process is efficient and controlled. The ionized gas atoms have enough kinetic energy to overcome the binding energy of the atoms in the target material, allowing for the effective sputtering of the target.
- The vaporized atoms from the target material are transported through the vacuum chamber and deposited onto the substrate, forming a uniform and adherent thin film.
-
Stability and Control:
- Plasma helps maintain a stable environment within the deposition chamber. The continuous flow of inert gas atoms and the ionization process ensure a consistent plasma density, which is crucial for uniform thin film deposition.
- The controlled environment provided by the plasma allows for precise control over the deposition process, enabling the production of high-quality thin films with desired properties.
-
Enhanced Deposition Techniques:
- In processes like plasma-enhanced chemical vapor deposition (PECVD) or plasma-assisted CVD (PACVD), plasma is used to excite the deposition precursor to an ion, radical, or excited neutral species. This excitation enhances the deposition process, leading to improved film quality and deposition rates.
- The use of plasma in these techniques allows for lower processing temperatures and higher deposition rates compared to traditional CVD methods, making it advantageous for various applications.
-
Non-Uniform Plasma Distribution:
- In some sputtering systems, such as those using low-pressure CVD (LPCVD), the plasma may be radially nonuniform, with greater intensity near the coil's surface. This nonuniformity can be advantageous for trapping ions and electrons close to the surface, which is essential for the deposition of thin films and nanostructured materials.
- The localized high-intensity plasma near the coil surface can enhance the deposition process by increasing the density of ionized species available for sputtering.
In summary, plasma is indispensable in the sputtering process due to its ability to efficiently transfer energy to the target material, facilitate the deposition of thin films, and maintain a stable and controlled deposition environment. Its role in enhancing deposition techniques and ensuring high-quality film production makes it a critical component in various thin film deposition applications.
Summary Table:
Key Aspect | Role of Plasma in Sputtering |
---|---|
Creation of Plasma | Ionizes inert gas atoms (e.g., argon) using electric fields or RF energy, producing ions and electrons. |
Energy Transfer | Transfers kinetic energy to dislodge target atoms, enabling thin film deposition. |
Stability & Control | Maintains a stable environment for consistent plasma density and uniform film deposition. |
Enhanced Deposition Techniques | Excites precursors in PECVD/PACVD, improving film quality and deposition rates at lower temperatures. |
Non-Uniform Plasma Distribution | Localized high-intensity plasma near surfaces enhances ion density for better sputtering. |
Want to optimize your thin film deposition process? Contact our experts today to learn more!