Powder metallurgy (PM) is a versatile manufacturing method capable of producing parts from a wide range of materials, including metals and ceramics. However, it is primarily limited to producing small parts due to several factors. The most significant limitation is the size of the presses used in the industry, which are typically around 1,500 tons, restricting the planar area of parts to about 40-50 square inches. Additionally, while PM can produce complex shapes, it is more challenging compared to other methods like casting or forging. Furthermore, PM parts often lack the strength and ductility of cast or forged parts, which can be a disadvantage for larger components requiring higher mechanical performance. Despite these limitations, PM remains a viable option for materials that are difficult to melt, contain, or deform, making it suitable for specific applications like deep well drilling tools.
Key Points Explained:
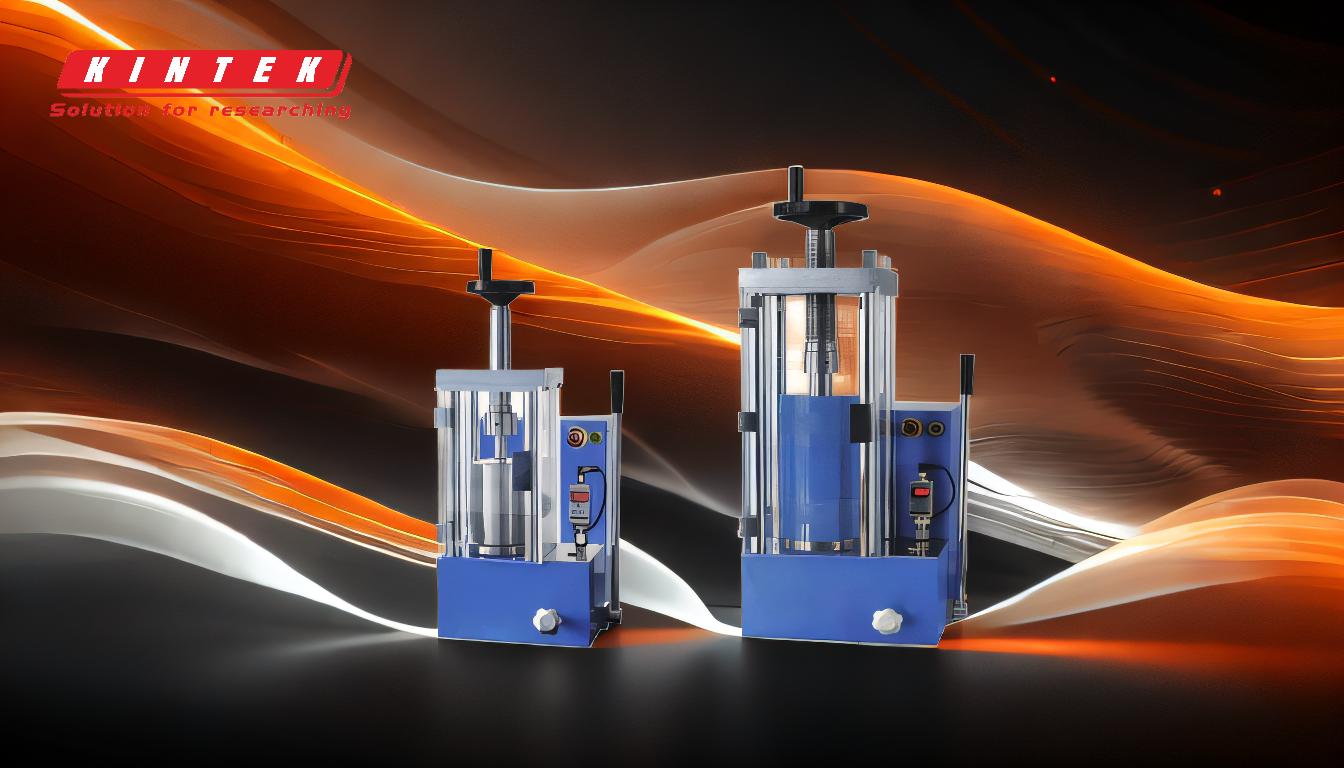
-
Press Size Limitations:
- The largest presses used in powder metallurgy are about 1,500 tons, which limits the practical size of parts to approximately 40-50 square inches of planar area.
- This constraint is due to the need for uniform pressure distribution during the compaction process, which becomes increasingly difficult with larger parts.
- Larger presses would be required to produce bigger parts, but such equipment is not commonly available in the industry.
-
Challenges with Complex Shapes:
- While powder metallurgy can produce complex shapes, it is more challenging compared to other manufacturing methods like casting or forging.
- Skilled manufacturers can overcome some of these challenges, but the process inherently requires precise control over powder distribution and compaction, which becomes more difficult with increasing complexity and size.
-
Mechanical Properties:
- PM parts generally do not achieve the same level of strength and ductility as parts produced by casting or forging.
- This is due to the nature of the PM process, which involves compacting and sintering powders, leading to potential porosity and weaker inter-particle bonds.
- For larger parts that require higher mechanical performance, these limitations make PM less suitable compared to traditional methods.
-
Material Versatility:
- Despite its limitations, powder metallurgy is highly versatile in terms of the materials it can process, including metals and ceramics.
- This makes PM an attractive option for materials that are difficult to melt, contain, or deform using traditional methods.
-
Specialized Applications:
- For larger parts, alternative methods like infiltration casting are used, where a mixture of metal or ceramic powders with a binder is filled into molds.
- This approach is employed in specialized applications, such as the manufacture of Polycrystalline Diamond Composite (PDC) drill bits for deep well drilling, where PM's unique advantages are leveraged despite its size limitations.
In summary, powder metallurgy's limitations in producing large parts are primarily due to press size constraints, challenges with complex shapes, and relatively lower mechanical properties compared to other methods. However, its versatility in material processing and suitability for specialized applications make it a valuable manufacturing technique within its operational limits.
Summary Table:
Key Limitation | Explanation |
---|---|
Press Size Constraints | Largest presses are ~1,500 tons, limiting part size to 40-50 sq. in. |
Complex Shapes | More challenging to produce compared to casting or forging. |
Mechanical Properties | Lower strength and ductility than cast or forged parts. |
Material Versatility | Can process metals and ceramics, ideal for hard-to-melt or deform materials. |
Specialized Applications | Used in deep well drilling tools like PDC bits, despite size limitations. |
Learn how powder metallurgy can meet your specialized needs—contact us today!