Vacuum plays a critical role in thin film coating processes, such as Physical Vapor Deposition (PVD) and Electron Beam (E-beam) deposition, by creating an environment that minimizes contamination, enhances material transport, and ensures high-quality film formation. A vacuum reduces the density of gas molecules, allowing evaporated material to travel longer distances without collisions, which improves directional deposition and film purity. Additionally, it prevents unwanted chemical reactions and contamination from ambient gases, ensuring strong adhesion and high-quality thin films. The vacuum environment is essential for achieving the desired film properties, such as uniformity, purity, and adhesion, making it indispensable in thin film coating processes.
Key Points Explained:
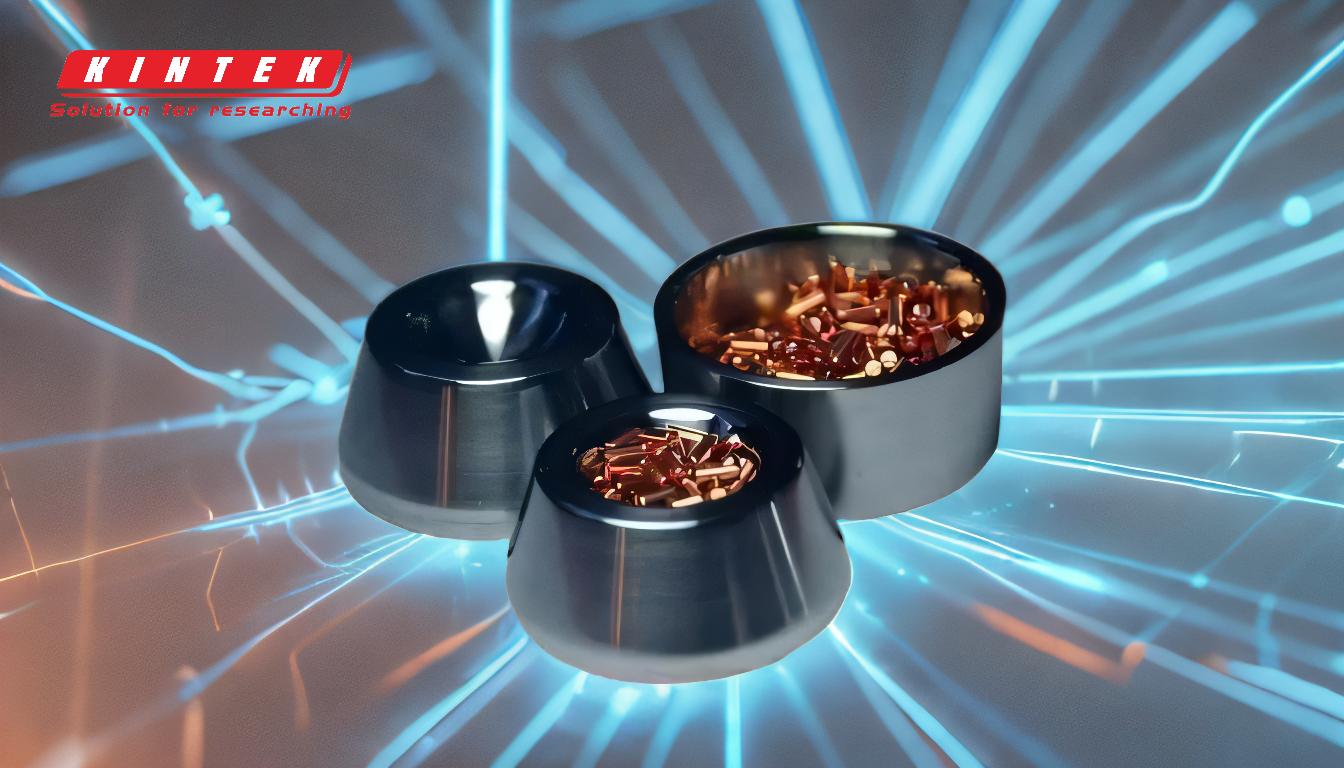
-
Minimizing Contamination:
- A vacuum environment reduces the presence of unwanted gases like oxygen, nitrogen, and carbon dioxide, which can react with the film material or cause defects.
- By maintaining a high vacuum (typically less than 10^-5 Torr), the system minimizes contamination from background gases, ensuring high-purity thin films.
-
Increasing Mean Free Path:
- In a vacuum, the mean free path of evaporated atoms or molecules increases significantly. For example, at 10^-5 Torr, the mean free path is approximately 1 meter.
- This allows the evaporated material to travel in a straight line to the substrate without colliding with gas molecules, ensuring efficient and directional deposition.
-
Enhancing Film Quality:
- A vacuum environment ensures that the evaporated material condenses uniformly on the substrate, leading to high-quality thin films with excellent adhesion and uniformity.
- It prevents the formation of defects caused by gas molecule collisions or chemical reactions, which can weaken the film's structural integrity.
-
Controlling Gas and Vapor Composition:
- A vacuum allows precise control over the composition of gases and vapors in the processing chamber, which is critical for achieving specific film properties.
- This control is essential for processes like reactive sputtering, where the introduction of reactive gases must be carefully managed.
-
Reducing Particle Density:
- By lowering the particle density in the chamber, a vacuum ensures that the evaporated material is the dominant species, reducing the likelihood of impurities being incorporated into the film.
- This is particularly important in applications requiring ultra-pure films, such as semiconductor manufacturing.
-
Supporting High Thermal Evaporation Rates:
- A vacuum environment facilitates high thermal evaporation rates by reducing the energy loss of evaporated atoms due to collisions with gas molecules.
- This is crucial for processes like resistive evaporation, where high evaporation rates are necessary for efficient deposition.
-
Preventing Chemical Reactions:
- A vacuum minimizes the presence of reactive gases, preventing unwanted chemical reactions between the film material and ambient gases.
- This is especially important for materials that are highly reactive with oxygen or nitrogen, ensuring the film retains its desired properties.
-
Achieving Ultra-High Vacuum for Advanced Applications:
- For advanced applications, achieving ultra-high vacuum (UHV) conditions (10^-9 Torr or lower) is necessary to eliminate trace gases that can cause defects.
- UHV environments are critical for producing defect-free thin films in high-precision industries like optics and microelectronics.
In summary, a vacuum is essential in thin film coating processes because it ensures a clean, controlled environment that enhances material transport, minimizes contamination, and enables the formation of high-quality, uniform, and adherent thin films. These benefits are critical for meeting the stringent requirements of modern applications in industries such as semiconductors, optics, and aerospace.
Summary Table:
Key Benefit | Explanation |
---|---|
Minimizing Contamination | Reduces unwanted gases, ensuring high-purity thin films. |
Increasing Mean Free Path | Allows evaporated material to travel longer distances without collisions. |
Enhancing Film Quality | Ensures uniform condensation and strong adhesion of thin films. |
Controlling Gas Composition | Enables precise control of gases for specific film properties. |
Reducing Particle Density | Lowers impurity incorporation, critical for ultra-pure films. |
Supporting High Evaporation | Facilitates high thermal evaporation rates for efficient deposition. |
Preventing Chemical Reactions | Minimizes reactive gases, preserving film properties. |
Achieving Ultra-High Vacuum | Eliminates trace gases for defect-free films in advanced applications. |
Learn how vacuum technology can elevate your thin film coating processes—contact our experts today!