Vacuum is essential for thin film deposition processes like CVD (Chemical Vapor Deposition) and PVD (Physical Vapor Deposition) because it creates a controlled environment that ensures uniform layer formation, reduces contamination, and optimizes the deposition process. In vacuum conditions, gas pressure is significantly lower than atmospheric pressure, which minimizes collisions between atoms and ions, enhances the mean free path, and influences the energy distribution in the plasma. Vacuum systems, including vacuum cleaning furnace, are used to maintain the required low-pressure environment, ensuring proper vaporization, transport, and condensation of the target material. Additionally, fixturing in vacuum deposition ensures uniform coating over complex surfaces or multiple substrates, directly impacting process throughput.
Key Points Explained:
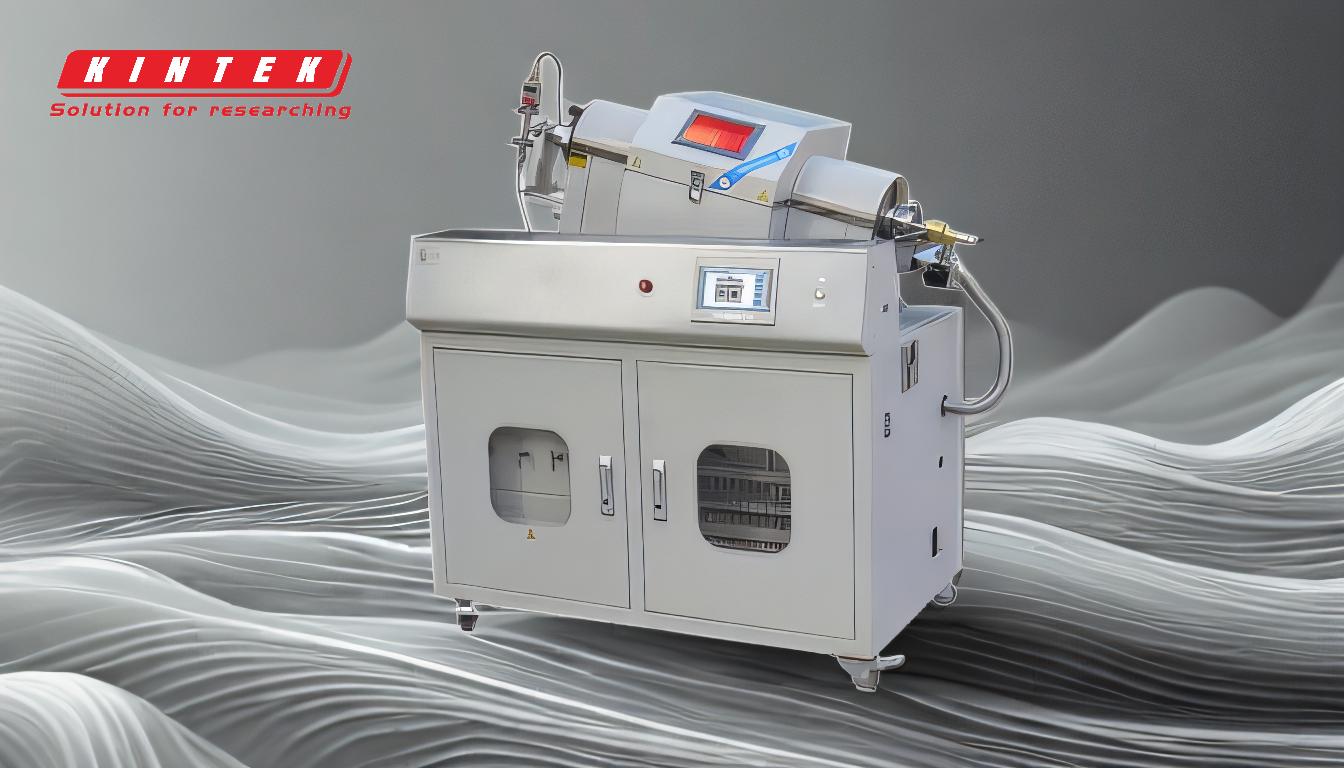
-
Controlled Environment for Uniform Deposition:
- In both CVD and PVD processes, a vacuum chamber is used to create a controlled environment. This ensures that the deposition material forms a uniform layer on the substrate.
- In CVD, precursors break down and exit the chamber via diffusion, while in PVD, metals form a layer capable of attenuating electromagnetic interference (EMI).
-
Reduction of Gaseous Contamination:
- Vacuum conditions significantly reduce gaseous contamination, which is critical for achieving high-quality thin films.
- Lower gas pressure minimizes the presence of impurities that could otherwise interfere with the deposition process.
-
Optimization of Mean Free Path and Energy Distribution:
- Vacuum plays a crucial role in determining the mean free path for collisions of atoms and high-energy ions.
- It influences the enthalpy, density of charged and uncharged particles, and energy distribution in the plasma, which are essential for efficient deposition.
-
Role of Vacuum Systems:
- Vacuum systems and pumping systems are used to maintain the necessary low-pressure environment, typically less than 10^-5 torr for processes like Thermal Evaporation.
- These systems ensure proper vaporization, transport, and condensation of the target material.
-
Importance of Fixturing:
- Fixturing in vacuum deposition holds the substrates to be coated and provides motion relative to the vaporization source.
- This motion is often necessary to ensure uniform deposition over large areas, complex surfaces, or multiple substrates.
- The design and process cycle times of the fixturing directly determine the throughput of the deposition process.
-
Vacuum Cleaning Furnace:
- A vacuum cleaning furnace is an example of equipment used to maintain the necessary vacuum conditions.
- It helps in achieving the desired low-pressure environment, which is critical for the success of thin film deposition processes.
By understanding these key points, it becomes clear why vacuum is indispensable in thin film deposition. It not only ensures the quality and uniformity of the deposited layers but also enhances the efficiency and throughput of the entire process.
Summary Table:
Key Benefit | Explanation |
---|---|
Controlled Environment | Ensures uniform layer formation in CVD and PVD processes. |
Reduction of Gaseous Contamination | Minimizes impurities, critical for high-quality thin films. |
Optimized Mean Free Path | Enhances collision efficiency and energy distribution in plasma. |
Role of Vacuum Systems | Maintains low-pressure environment (<10^-5 torr) for proper material transport. |
Fixturing for Uniform Coating | Ensures even deposition on complex surfaces or multiple substrates. |
Vacuum Cleaning Furnace | Maintains necessary vacuum conditions for successful deposition. |
Ready to optimize your thin film deposition process? Contact us today to learn more about vacuum solutions!