RF sputtering is often considered superior to DC sputtering due to its ability to handle insulating materials, operate at lower pressures, and prevent charge buildup on the target surface. Unlike DC sputtering, which is limited to conductive materials, RF sputtering uses an alternating current (AC) power source, typically at 13.56 MHz, to sputter both conductive and non-conductive materials. This makes RF sputtering more versatile, especially for dielectric targets. Additionally, RF sputtering operates at lower pressures, reducing collisions between target material particles and gas ions, which enhances the quality of the deposited layer. While RF sputtering has a lower deposition rate and higher cost compared to DC sputtering, its advantages in material compatibility and process stability make it the preferred choice for applications involving insulating materials and smaller substrates.
Key Points Explained:
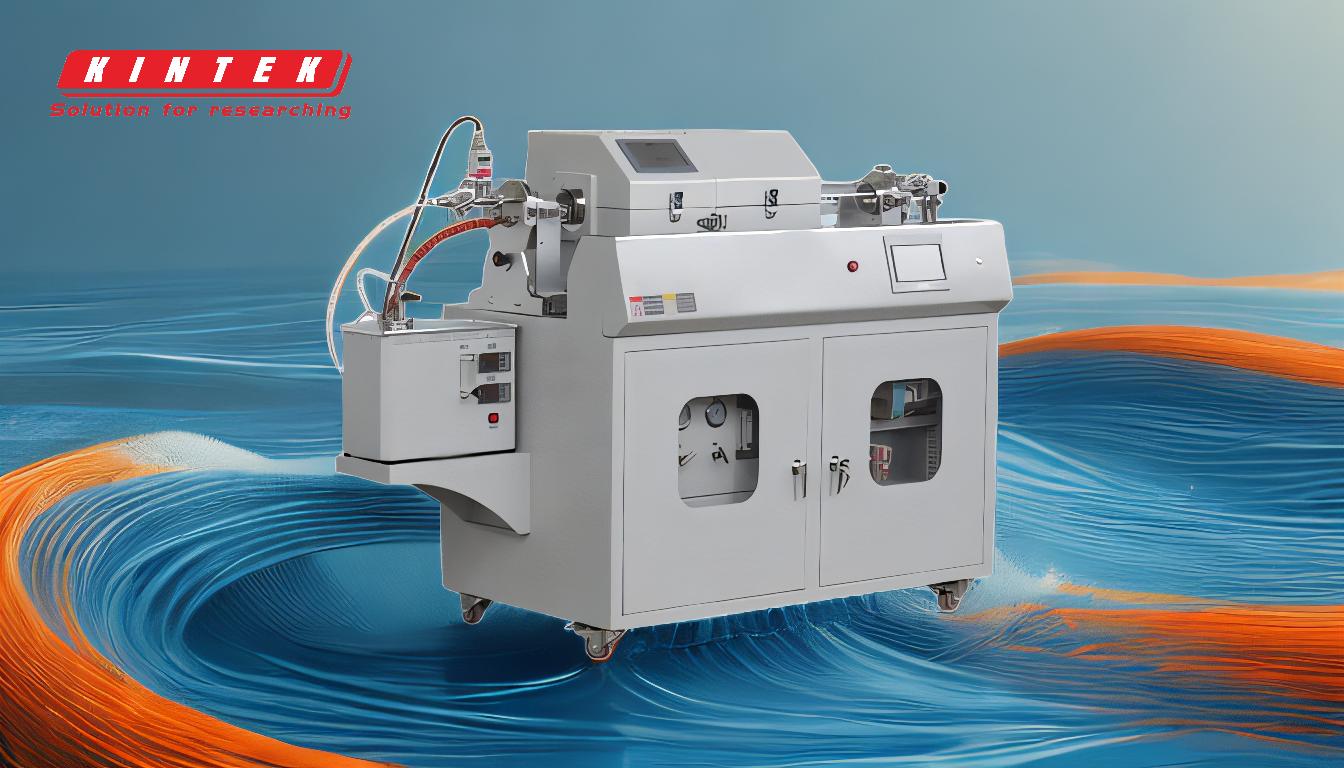
-
Material Compatibility:
- DC Sputtering: Limited to conductive materials due to charge accumulation on insulating targets, which disrupts the sputtering process.
- RF Sputtering: Can sputter both conductive and non-conductive materials. The alternating current prevents charge buildup on insulating targets, making it ideal for dielectric materials.
-
Operating Pressure:
- DC Sputtering: Operates at higher pressures (around 100 mTorr), leading to more collisions between target material particles and gas ions, which can reduce deposition efficiency and layer quality.
- RF Sputtering: Operates at lower pressures (less than 15 mTorr), reducing collisions and allowing a more direct pathway for particles to reach the substrate, resulting in higher-quality layers.
-
Charge Buildup and Plasma Stability:
- DC Sputtering: Prone to charge accumulation on the target surface, especially with insulating materials, which can lead to arcing and unstable plasma.
- RF Sputtering: The alternating current eliminates charge buildup, preventing arcing and ensuring a stable plasma, which improves the quality and uniformity of the deposited layer.
-
Deposition Rate and Cost:
- DC Sputtering: Offers higher deposition rates and is more cost-effective, making it suitable for large-scale production and conductive materials.
- RF Sputtering: Has a lower deposition rate and is more expensive, but its advantages in material compatibility and process stability make it more suitable for specialized applications, particularly with insulating materials and smaller substrates.
-
Plasma Formation and Target Utilization:
- DC Sputtering: Plasma formation is limited to the cathode or target surface, leading to localized erosion (Race Track Erosion) and shorter target lifetimes.
- RF Sputtering: Plasma formation extends throughout the vacuum chamber, involving a larger surface area of the target. This reduces localized erosion, extends target lifetime, and improves process efficiency.
-
Frequency and Voltage:
- DC Sputtering: Uses a direct current (DC) power source with high voltage (2,000-5,000 volts).
- RF Sputtering: Uses an alternating current (AC) power source at a fixed frequency of 13.56 MHz, with higher voltage requirements (1,012 volts or higher). The AC power source enables the sputtering of insulating materials and maintains a stable plasma at lower pressures.
In summary, RF sputtering is better than DC sputtering for applications involving insulating materials, lower operating pressures, and higher process stability. While it may have a lower deposition rate and higher cost, its advantages in material compatibility, plasma stability, and target utilization make it the preferred choice for specialized applications.
Summary Table:
Feature | DC Sputtering | RF Sputtering |
---|---|---|
Material Compatibility | Limited to conductive materials | Works with conductive and non-conductive materials |
Operating Pressure | Higher (~100 mTorr) | Lower (<15 mTorr) |
Charge Buildup | Prone to charge accumulation | Prevents charge buildup |
Deposition Rate | Higher | Lower |
Cost | More cost-effective | More expensive |
Plasma Stability | Less stable | Highly stable |
Target Utilization | Localized erosion, shorter target life | Reduced erosion, longer target life |
Interested in RF sputtering for your precision applications? Contact us today to learn more!