PVD (Physical Vapor Deposition) coatings are highly regarded for their durability, resistance to tarnishing, and ability to withstand harsh environmental conditions. These coatings are applied in a vacuum environment, resulting in a thin, pure, and highly adherent layer that provides exceptional protection against corrosion, abrasion, and high temperatures. Due to their robust properties, PVD coatings are widely used in industries such as electronics, optics, medical devices, and more. Their resistance to tarnishing makes them an ideal choice for applications requiring long-lasting aesthetic and functional performance.
Key Points Explained:
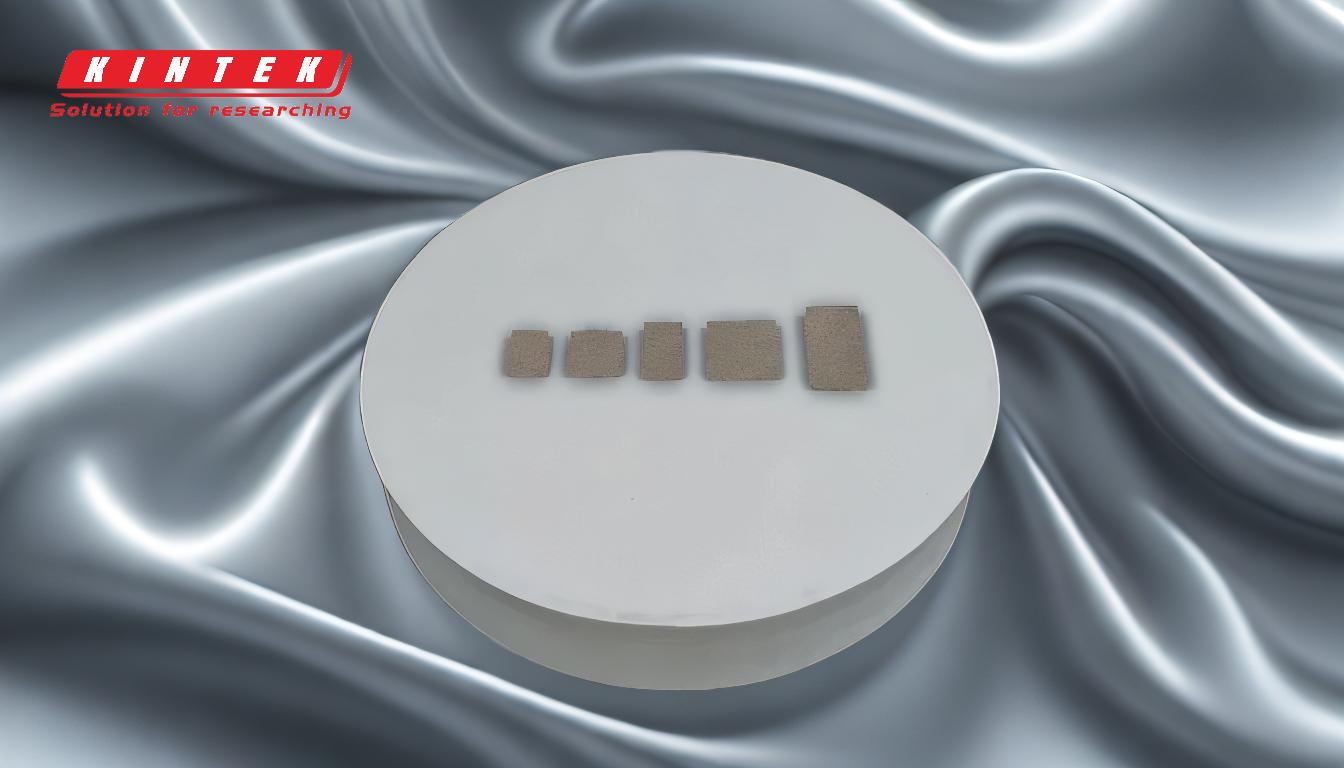
-
Durability and Resistance to Tarnishing:
- PVD coatings are highly resistant to tarnishing due to their chemical inertness and strong adhesion to the substrate. The process involves depositing a thin layer of material in a vacuum, which ensures purity and uniformity, reducing the likelihood of oxidation or chemical reactions that cause tarnishing.
- The coatings are designed to withstand exposure to moisture, chemicals, and UV radiation, making them suitable for environments where tarnishing is a concern.
-
Corrosion and Abrasion Resistance:
- PVD coatings provide excellent protection against corrosion and abrasion, which are common causes of tarnishing in metals. The coatings act as a barrier, preventing the underlying material from reacting with environmental factors.
- Their hardness and wear resistance contribute to maintaining the coating's integrity over time, ensuring that the surface remains free from tarnish and degradation.
-
Temperature Tolerance:
- PVD coatings can withstand high temperatures without degrading, which is crucial for applications exposed to heat. This thermal stability prevents the breakdown of the coating, which could otherwise lead to tarnishing or discoloration.
-
Versatility and Applications:
- PVD coatings are versatile and can be applied to a wide range of substrates, including metals, ceramics, and plastics. This adaptability makes them suitable for various industries, from consumer electronics to medical devices.
- Their ability to produce different finishes, such as matte, glossy, or textured, ensures that they meet both functional and aesthetic requirements without compromising on tarnish resistance.
-
Cost-Effectiveness and Efficiency:
- The efficient use of materials in the PVD process reduces waste and lowers costs, making it an economical choice for long-term applications. The durability of PVD coatings also means fewer replacements or repairs, further enhancing their cost-effectiveness.
In summary, PVD coatings are highly resistant to tarnishing due to their durability, chemical inertness, and ability to withstand harsh conditions. Their versatility and cost-effectiveness make them a preferred choice for applications requiring both functional performance and aesthetic appeal.
Summary Table:
Feature | Description |
---|---|
Tarnish Resistance | Highly resistant due to chemical inertness and strong adhesion. |
Corrosion Resistance | Acts as a barrier against environmental factors, preventing tarnish. |
Temperature Tolerance | Withstands high temperatures without degrading, ensuring long-term stability. |
Versatility | Suitable for metals, ceramics, and plastics across various industries. |
Cost-Effectiveness | Reduces waste and lowers long-term costs due to durability and efficiency. |
Ensure your materials are protected with PVD coatings—contact us today to learn more!