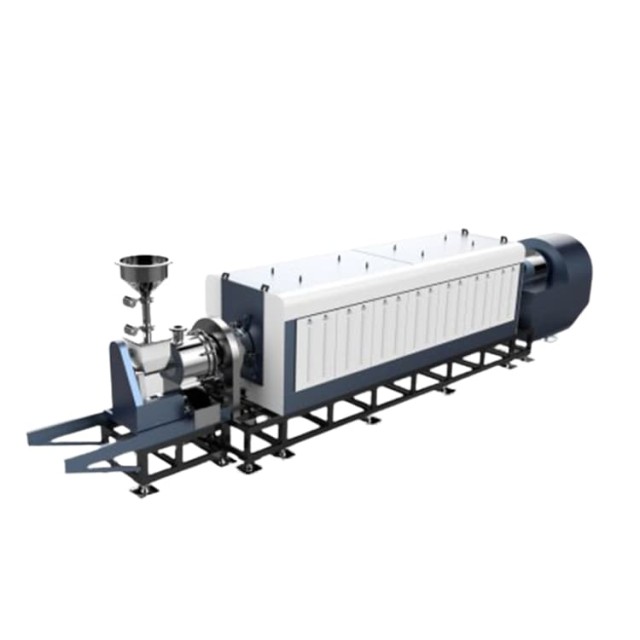
Electric Rotary Kiln
Electric Rotary Kiln Small Rotary Furnace Biomass Pyrolysis Plant
Item Number : RBPF
Price varies based on specs and customizations
- Working temperature
- 200-1100 ℃
- Controller
- PID
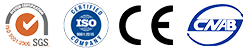
Shipping:
Contact us to get shipping details Enjoy On-time Dispatch Guarantee.
Why Choose Us
Reliable PartnerEasy ordering process, quality products, and dedicated support for your business success.
Introduction
A Rotary Biomass Pyrolysis Furnace Plant is a device used to convert biomass into biochar, bio-oil, and syngas through a thermochemical process known as pyrolysis. Pyrolysis involves heating biomass in the absence of oxygen to break it down into its constituent components. The resulting products can be used for various applications, such as energy production, soil amendment, and the production of biofuels and chemicals.
The Rotary Biomass Pyrolysis Furnace Plant consists of a rotating cylindrical reactor where the biomass is heated and decomposed. The reactor is typically heated using an external heat source, such as an electric heater or a gas burner. The rotation of the reactor ensures uniform heating of the biomass and promotes efficient heat transfer.
The products of pyrolysis are separated and collected based on their physical and chemical properties. Biochar, a solid residue rich in carbon, is discharged from the reactor, while bio-oil and syngas are condensed and collected. The bio-oil can be further refined into biofuels or used as a feedstock for chemical production. Syngas, a mixture of gases including hydrogen, carbon monoxide, and methane, can be used as a fuel or as feedstock for the production of chemicals.
Rotary Biomass Pyrolysis Furnace Plants offer several advantages, including high efficiency, low emissions, and the ability to process a wide range of biomass feedstocks. They are widely used in industries such as agriculture, forestry, and waste management for the production of renewable energy and value-added products from biomass.
Applications
Rotary Biomass Pyrolysis Furnace Plants are widely used in various industries due to their versatility and efficiency in converting organic materials into valuable products. Here are the main application areas of this equipment:
- Waste management: Pyrolysis furnaces play a crucial role in waste management by converting biomass waste, such as wood, bamboo, coconut shells, rice hulls, and garden waste, into biochar. This process helps reduce the amount of waste sent to landfills and promotes sustainable waste disposal practices.
- Biofuel production: Rotary Biomass Pyrolysis Furnace Plants are employed in the production of biofuels, such as bio-oil and syngas, from biomass sources. These fuels are renewable and environmentally friendly alternatives to fossil fuels, contributing to the reduction of greenhouse gas emissions.
- Chemical production: The pyrolysis process can be utilized to produce a range of valuable chemicals, including activated carbon, biochar, and other carbon-based materials. These products find applications in various industries, such as pharmaceuticals, cosmetics, and agriculture.
- Research and development: Rotary Biomass Pyrolysis Furnace Plants are widely used in research and development laboratories to study the thermal behavior and decomposition characteristics of various organic materials. This knowledge aids in the optimization of pyrolysis processes and the development of new applications.
- Carbon sequestration: Pyrolysis can contribute to carbon sequestration efforts by converting biomass into stable carbon-rich biochar. This biochar can be used as a soil amendment, enhancing soil fertility and reducing atmospheric carbon dioxide levels.
Detail&Parts
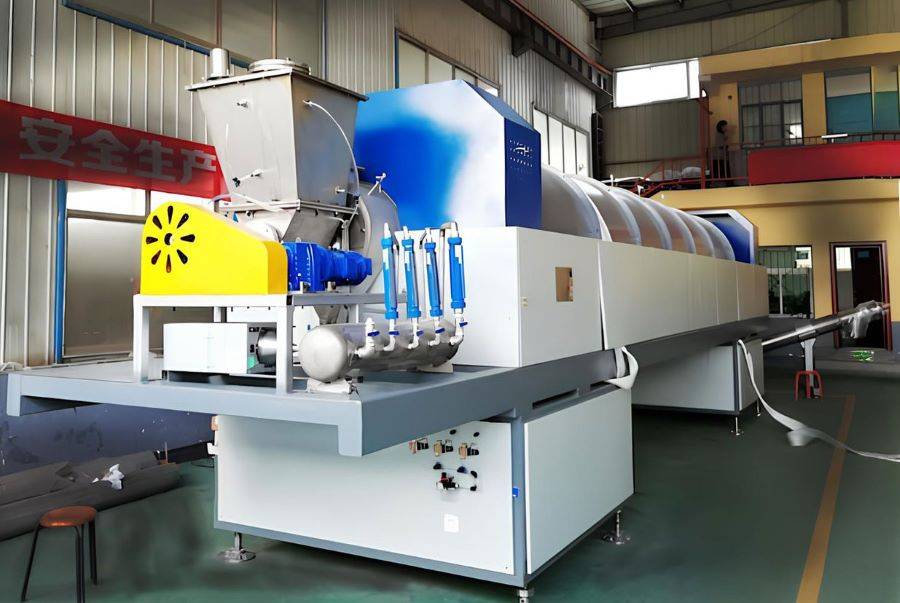
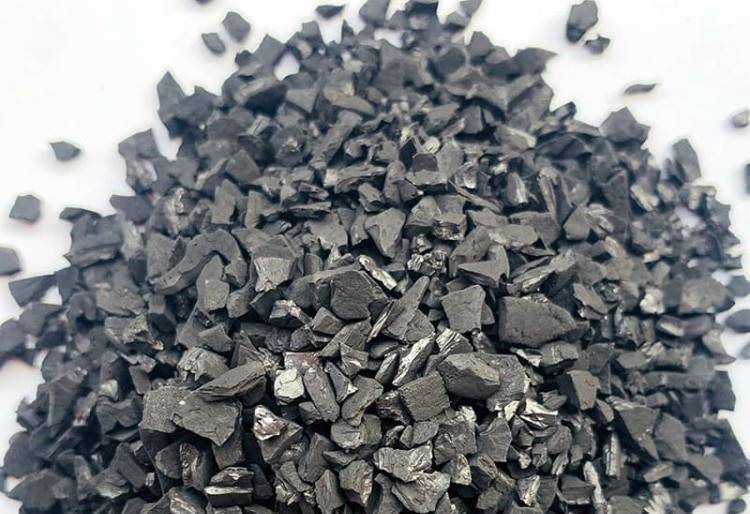
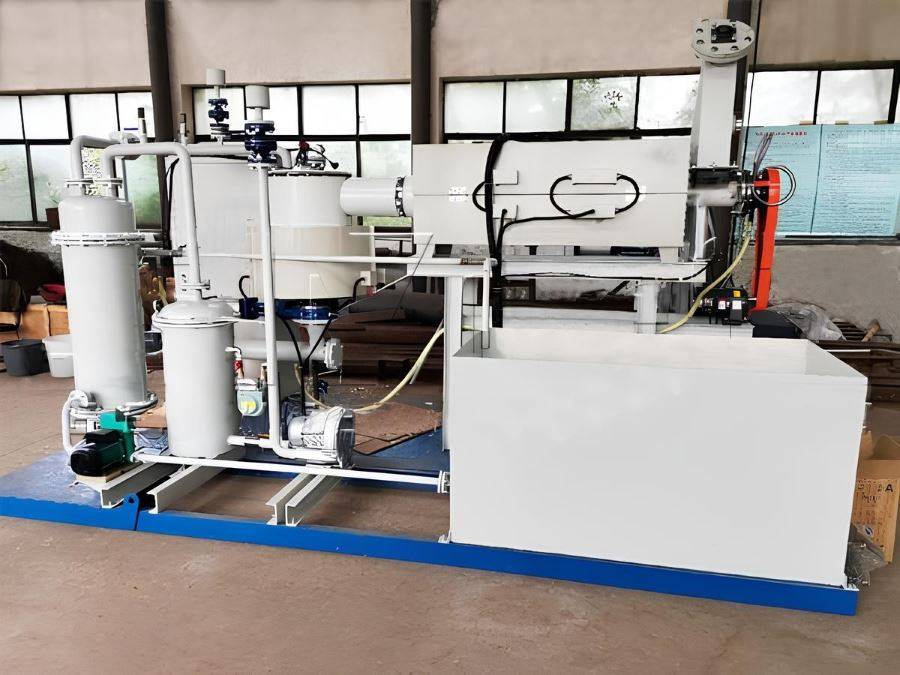
Features
- Wide range working temperature from 200℃ to 1100℃:** Allows for precise control of the pyrolysis process for optimal results.
- High accurate temperature control with PID thermal controller:** Ensures consistent and accurate temperature maintenance, critical for successful pyrolysis.
- Excellent vacuum sealed system, precise controlled atmosphere:** Prevents oxygen from entering the furnace, creating an ideal environment for pyrolysis.
- Compact full system setup, ideal for researching labs small batch or pilot production:** Saves space and resources, making it suitable for various applications.
- Automatic batch type continuous feeding device for even material feeding and distributing:** Automates the feeding process, ensuring uniform material distribution for efficient pyrolysis.
- Indirect heating tube chamber with rotating and tilting function, premium heating uniformity:** Distributes heat evenly throughout the material, maximizing pyrolysis efficiency.
- Dynamic rotary vacuum sealing for the target pyrolysis solids discharging and collecting:** Facilitates easy and efficient collection of pyrolysis solids.
- Pre-heating and assisting heating for accurate collecting of the target decomposing gases:** Captures target gases effectively, allowing for further analysis or utilization.
- Optional cold trap and condenser device setup for easy control of target liquids produced:** Condenses and collects liquid products, providing additional options for product recovery.
- Optional gas emissions ignition device to burn the harmful gases before releasing to the air:** Minimizes environmental impact by eliminating harmful gas emissions.
- Optional syngas online detecting and monitoring function for various target gases like CO, CO2, CH4, H2, N2, C2H6, C3H8:** Allows for real-time monitoring of syngas composition, enabling process optimization and product quality control.
Advantages
Wide range working temperature from 200℃ to 1100℃:** This allows the furnace to be used for a variety of applications, including the processing of different types of biomass materials.
High accurate temperature control with PID thermal controller:** This ensures precise control of the furnace temperature, which is important for achieving optimal pyrolysis results.
- Excellent vacuum sealed system, precise controlled atmosphere:** This helps to create an oxygen-free environment inside the furnace, which is essential for the pyrolysis process.
- Compact full system setup, ideal for researching labs small batch or pilot production:** The furnace is compact and easy to set up, making it ideal for use in research laboratories or for small-scale production.
- Automatic batch type continuous feeding device for even material feeding and distributing:** This helps to ensure that the biomass material is evenly distributed inside the furnace, which promotes consistent pyrolysis results.
- Indirect heating tube chamber with rotating and tilting function, premium heating uniformity:** This provides uniform heating of the biomass material, which helps to improve the efficiency of the pyrolysis process.
- Dynamic rotary vacuum sealing for the target pyrolysis solids discharging and collecting:** This allows for easy removal of the pyrolysis solids from the furnace, which simplifies the collection process.
- Pre-heating and assisting heating for accurate collecting of the target decomposing gases:** This helps to ensure that the target gases are collected efficiently, which is important for maximizing the yield of valuable products.
- Optional cold trap and condenser device setup for easy control of target liquids produced:** This allows for the easy collection of target liquids, which can be further processed or used for other purposes.
- Optional gas emissions ignition device to burn the harmful gases before releasing to the air:** This helps to reduce the environmental impact of the pyrolysis process by minimizing the release of harmful gases.
- - **Optional syngas online detecting and monitoring function for various target gases like CO,CO2,CH4,H2,N2,C2H6,C3H8:** This allows for real-time monitoring of the target gases, which is important for optimizing the pyrolysis process and ensuring the production of high-quality products.
- Overall, pyrolysis furnaces are an important tool for converting organic materials into valuable products, and they have a wide range of applications in industry and research. However, it's important to carefully consider the potential impacts and to ensure that they are operated and maintained in a responsible manner.
Continuous production rotary pyrolysis furnace
Features of Biomass pyrolysis furnace by KINTEK
- Wide range working temperature from 200℃ to 1100℃
- High accurate temperature control with PID thermal controller
- Excellent vacuum sealed system, precise controlled atmosphere
- Compact full system setup, ideal for researching labs small batch or pilot production
- Automatic batch type continuous feeding device for even material feeding and distributing
- Indirect heating tube chamber with rotating and tilting function, premium heating uniformity
- Dynamic rotary vacuum sealing for the target pyrolysis solids discharging and collecting
- Pre-heating and assisting heating for accurate collecting of the target decomposing gases
- Optional cold trap and condenser device setup for easy control of target liquids produced
- Optional gas emissions ignition device to burn the harmful gases before releasing to the air
- Optional syngas online detecting and monitoring function for various target gases like CO,CO2,CH4,H2,N2,C2H6,C3H8
Warnings
Operator safety is the top important issue! Please operate the equipment with cautions. Working with inflammable& explosive or toxic gases is very dangerous, operators must take all necessary precautions before starting the equipment. Working with positive pressure inside the reactors or chambers is dangerous, operator must fellow the safety procedures strictly. Extra caution must also be taken when operating with air-reactive materials, especially under vacuum. A leak can draw air into the apparatus and cause a violent reaction to occur.
Designed for You
KinTek provide deep custom made service and equipment to worldwide customers, our specialized teamwork and rich experienced engineers are capable to undertake the custom tailoring hardware and software equipment requirements, and help our customer to build up the exclusive and personalized equipment and solution!
Would you please drop your ideas to us, our engineers are ready for you now!
FAQ
What Is A Pyrolysis Plant?
What Types Of Materials Can Be Processed In A Rotary Furnace?
What Is A Pyrolysis Furnace?
What Is A Rotary Tube Furnace?
How Does A Pyrolysis Plant Work?
What Are The Rotary Furnace Types?
How Does A Pyrolysis Furnace Work?
How Does A Rotary Tube Furnace Work?
What Are The Main Applications Of Pyrolysis Plants?
What Are The Advantages Of Rotor Furnace?
What Are The Applications Of Pyrolysis Furnaces?
What Are The Advantages Of A Rotary Tube Furnace?
What Is The Function Of Rotary Tube Furnace?
What Is The Efficiency Of A Rotary Furnace?
What Are The Advantages Of Using Pyrolysis Furnaces?
What Are The Advantages Of Rotary Tube Furnace?
Can A Rotary Furnace Be Used For Continuous Production?
What Factors Should Be Considered When Selecting A Pyrolysis Furnace?
How Can The Performance Of A Rotary Furnace Be Optimized?
What Safety Precautions Should Be Followed When Using A Pyrolysis Furnace?
4.8
out of
5
The equipment is excellent and serves its purpose well. I highly recommend this product to anyone interested in pyrolysis.
4.9
out of
5
I am very happy with the way this product works. It's efficient and easy to use. KINTEK SOLUTION is the best!
4.7
out of
5
The product arrived quickly and in perfect condition. I am very satisfied with my purchase.
4.9
out of
5
This product is a great value for the price. It's well-made and works great. I highly recommend it.
5.0
out of
5
I am very happy with this product. It is durable and works perfectly. I would definitely recommend it.
4.8
out of
5
The product is of high quality and works very well. I am very satisfied with my purchase.
5.0
out of
5
This product is amazing! It's easy to use and works like a charm. I'm so glad I bought it.
4.7
out of
5
The product is very well-made and works perfectly. I am very happy with my purchase.
4.8
out of
5
This product is a great investment. It's durable and works great. I highly recommend it.
4.9
out of
5
I am very happy with this product. It's easy to use and works perfectly. I would definitely recommend it.
5.0
out of
5
This product is top-notch! It's well-made and works flawlessly. I'm very satisfied with my purchase.
4.8
out of
5
I am very happy with this product. It's durable and works great. I would definitely recommend it.
Products
Electric Rotary Kiln Small Rotary Furnace Biomass Pyrolysis Plant
REQUEST A QUOTE
Our professional team will reply to you within one business day. Please feel free to contact us!
Related Products
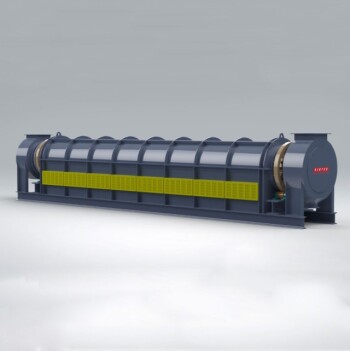
Electric Rotary Kiln Pyrolysis Furnace Plant Machine Calciner Small Rotary Kiln Rotating Furnace
Electric rotary kiln - precisely controlled, it's ideal for calcination and drying of materials like lithium cobalate, rare earths, and non-ferrous metals.
Electric Rotary Kiln Continuous Working Small Rotary Furnace Heating Pyrolysis Plant
Efficiently calcine and dry bulk powder and lump fluid materials with an electric heating rotary furnace. Ideal for processing lithium ion battery materials and more.
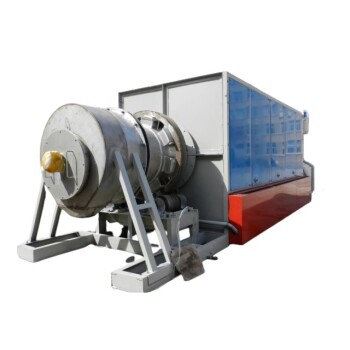
Electric Rotary Kiln Small Rotary Furnace for Activated Carbon Regeneration
Revitalize your activated carbon with KinTek's Electric Regeneration Furnace. Achieve efficient and cost-effective regeneration with our highly automated rotary kiln and intelligent thermal controller.
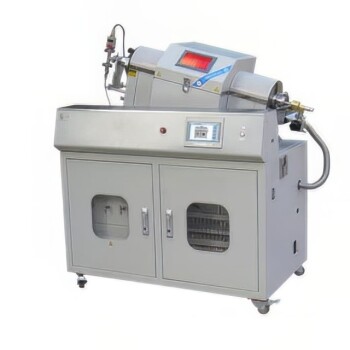
Inclined Rotary Plasma Enhanced Chemical Vapor Deposition PECVD Equipment Tube Furnace Machine
Introducing our inclined rotary PECVD furnace for precise thin film deposition. Enjoy automatic matching source, PID programmable temperature control, and high accuracy MFC mass flowmeter control. Built-in safety features for peace of mind.
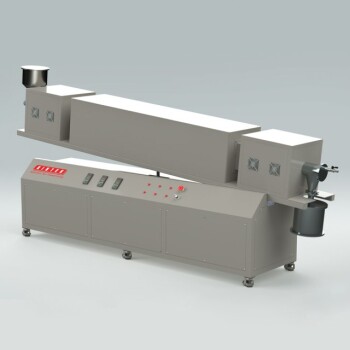
Vacuum Sealed Continuous Working Rotary Tube Furnace Rotating Tube Furnace
Experience efficient material processing with our vacuum-sealed rotary tube furnace. Perfect for experiments or industrial production, equipped with optional features for controlled feeding and optimized results. Order now.
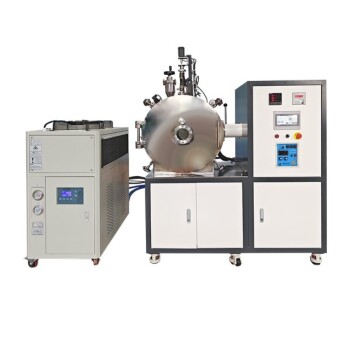
Lab-Scale Vacuum Induction Melting Furnace
Get precise alloy composition with our Vacuum Induction Melting Furnace. Ideal for aerospace, nuclear energy, and electronic industries. Order now for effective smelting and casting of metals and alloys.
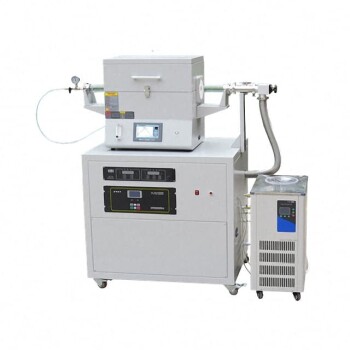
Efficient split chamber CVD furnace with vacuum station for intuitive sample checking and quick cooling. Up to 1200℃ max temperature with accurate MFC mass flowmeter control.
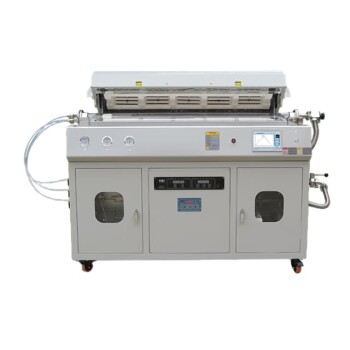
Multi Heating Zones CVD Tube Furnace Machine Chemical Vapor Deposition Chamber System Equipment
KT-CTF14 Multi Heating Zones CVD Furnace - Precise Temperature Control and Gas Flow for Advanced Applications. Max temp up to 1200℃, 4 channels MFC mass flow meter, and 7" TFT touch screen controller.
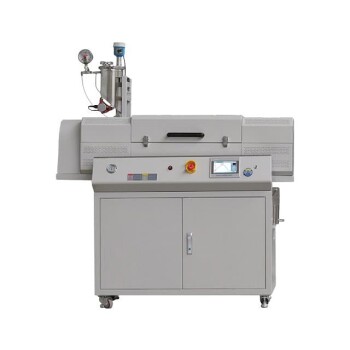
Laboratory Vacuum Tilt Rotary Tube Furnace Rotating Tube Furnace
Discover the versatility of Laboratory Rotary Furnace: Ideal for calcination, drying, sintering, and high-temperature reactions. Adjustable rotating and tilting functions for optimal heating. Suitable for vacuum and controlled atmosphere environments. Learn more now!
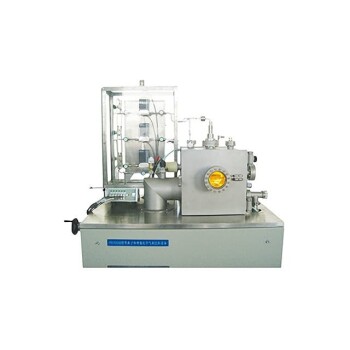
Inclined Rotary Plasma Enhanced Chemical Vapor Deposition PECVD Equipment Tube Furnace Machine
Upgrade your coating process with PECVD coating equipment. Ideal for LED, power semiconductors, MEMS and more. Deposits high-quality solid films at low temps.
Related Articles
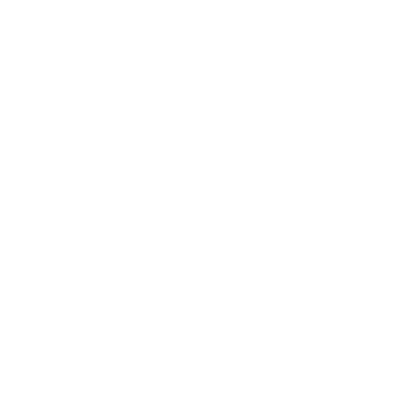
Electric Rotary Kiln Pyrolysis Furnace: A Comprehensive Guide to Pyrolysis Technology
Discover the principles, applications, and advantages of electric rotary kiln pyrolysis furnaces. Explore various heating methods, factors affecting efficiency, and the environmental benefits of this technology.
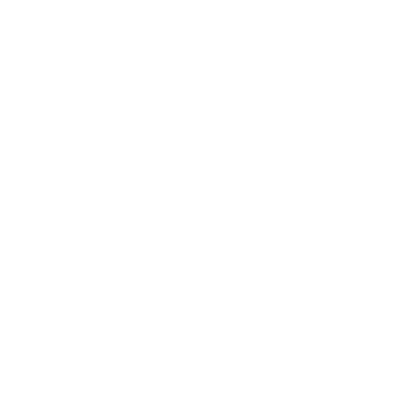
Electric Rotary Kiln Pyrolysis Furnace: Design, Operation, and Applications
Explore the comprehensive guide on electric rotary kiln pyrolysis furnaces, including their design, operation, efficiency factors, and diverse applications in industries like waste processing and biofuel production.
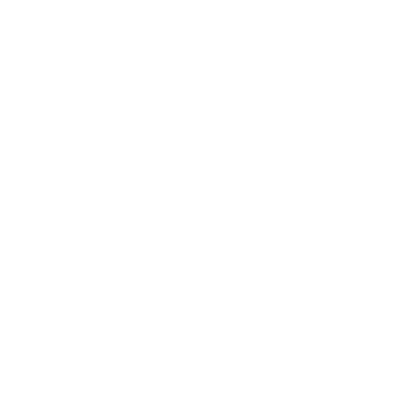
How Biomass Pyrolysis Machines Work A Comprehensive Overview
Biomass pyrolysis machines are designed to convert biomass materials into useful products such as biochar, bio-oil, and syngas.
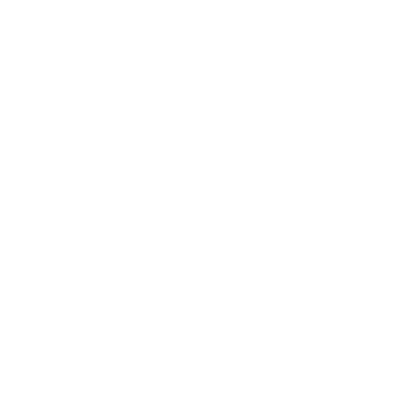
Biomass Pyrolysis Equipment A Sustainable Solution for Waste Management
Biomass pyrolysis has gained increased attention as a sustainable solution for waste management and renewable energy generation.
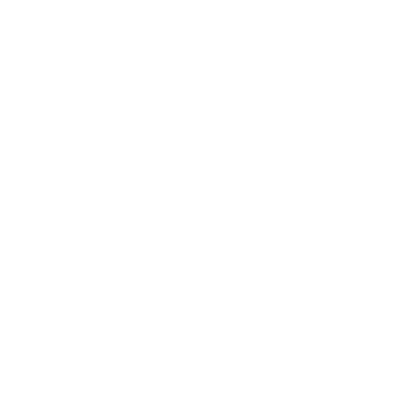
Biomass Pyrolysis An Effective Means of Producing Biofuels
Biomass pyrolysis is a process that involves heating organic matter in the absence of oxygen to break it down into smaller molecules. This technology has gained popularity due to its potential to produce biofuels.
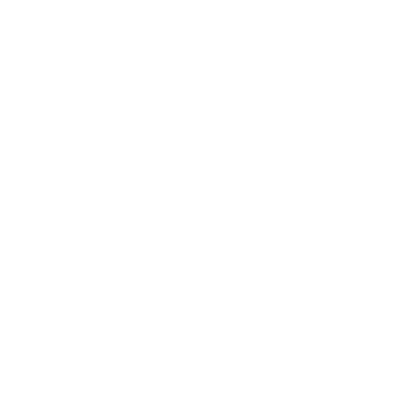
The Advantages and Disadvantages of Different Biomass Feedstocks for Pyrolysis
Different feedstocks have their own unique advantages and disadvantages for pyrolysis, which must be carefully considered when selecting the most suitable feedstock for a particular application.
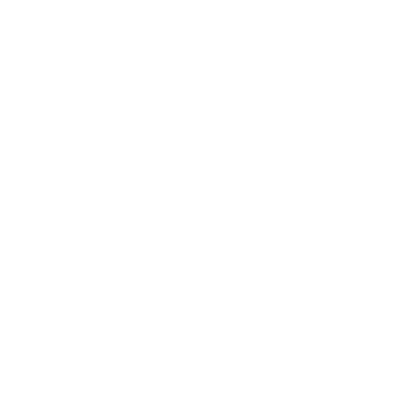
Exploring the Functions and Advantages of Rotary Tube Furnaces
Discover how rotary tube furnaces work and why they are used in advanced materials processing. Learn about the basic technique of rotary furnaces and their customizable features. Explore the advantages of rotary tube furnaces over other furnace types.
markdown to html 用
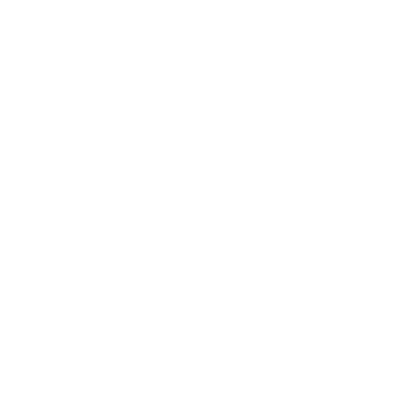
Exploring the Benefits and Applications of Rotary Furnaces: A Comprehensive Guide
Rotary tube furnaces are highly versatile tools that can be used for a wide range of physicochemical processing applications in the laboratory.
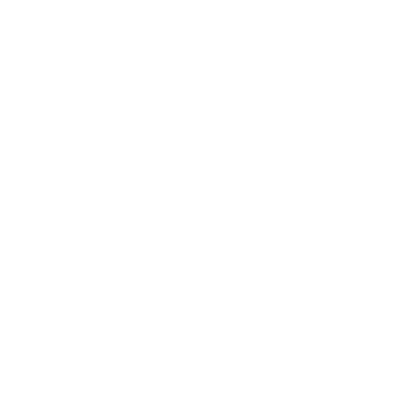
Optimizing Industrial Processes: Rotary Kiln and Laboratory Furnace Solutions
Discover how rotary kilns and laboratory furnaces revolutionize industrial processes. Learn about rotary kiln sizing and design, laboratory furnace features, and industries served. Explore the production of carbon products like biochar and activated carbon.
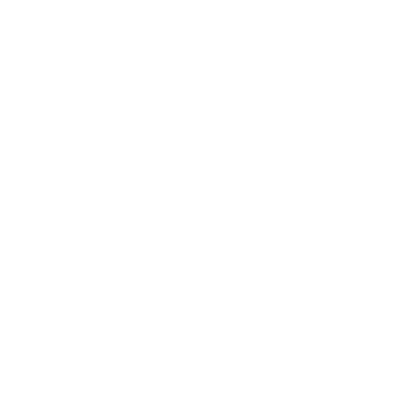
Rotary Furnaces: A Comprehensive Guide to Advanced Materials Processing
Rotary furnaces are widely used for advanced materials processing due to their versatility, temperature uniformity, and energy efficiency. This guide provides an overview of rotary furnace technology, including its working principle, applications, design improvements, and control systems.
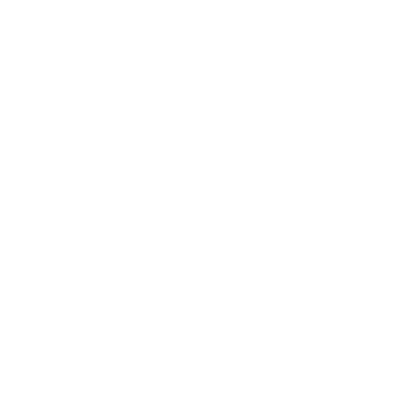
Rotary Furnaces: Advanced Materials Processing and Applications
Rotary furnaces are versatile and efficient thermal processing systems used in various industries. This comprehensive guide explores the basics of rotary furnaces, their applications, advantages, and key components. Discover how rotary furnaces contribute to advanced materials processing and enhance productivity.