Yes, there are different types of annealing processes, each tailored to achieve specific material properties or address particular industrial needs. Annealing is a heat treatment process that involves heating metal to a specific temperature, holding it there, and then cooling it at a controlled rate. This process helps soften materials, improve machinability, reduce internal stresses, and enhance mechanical or electrical properties. The specific types of annealing include Black Annealing, Blue Annealing, Box Annealing, Bright Annealing, Cycle Annealing, Flame Annealing, Full Annealing, Graphitizing, Intermediate Annealing, Isothermal Annealing, Process Annealing, Quench Annealing, and Spheroidizing. Each type is designed for specific applications and materials, ensuring the desired microstructure and properties are achieved.
Key Points Explained:
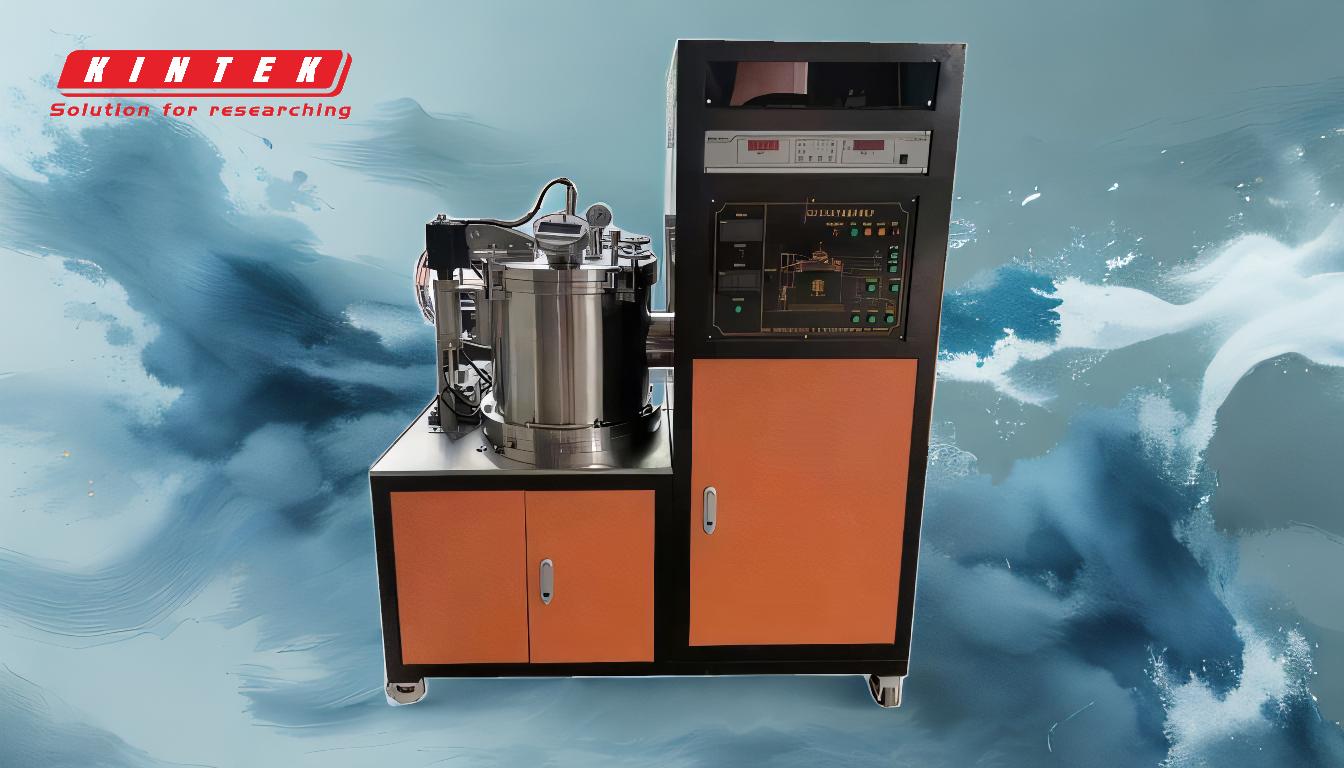
-
Definition of Annealing:
- Annealing is a heat treatment process that involves heating a material to a specific temperature, holding it at that temperature, and then cooling it at a controlled rate. This process is used to soften materials, improve machinability, reduce internal stresses, and enhance mechanical or electrical properties.
-
Stages of Annealing:
- Recovery: This is the first stage where the material is heated to relieve internal stresses without significantly altering its microstructure.
- Recrystallization: In this stage, new grains form in the material, replacing the deformed grains. This occurs at higher temperatures and results in a softer and more ductile material.
- Grain Growth: The final stage involves the growth of these new grains, which can affect the material's mechanical properties. Controlling this stage is crucial to achieving the desired material characteristics.
-
Types of Annealing:
- Black Annealing: Typically used for steel, this process involves heating the material in an open furnace, resulting in a black oxide layer on the surface.
- Blue Annealing: Similar to Black Annealing but performed at a lower temperature, resulting in a blue oxide layer. It is often used for stainless steel.
- Box Annealing: The material is heated in a sealed container to protect it from oxidation. This method is used for materials that require a controlled atmosphere.
- Bright Annealing: Conducted in a controlled atmosphere or vacuum to prevent oxidation, resulting in a bright, clean surface. Commonly used for stainless steel and other non-ferrous metals.
- Cycle Annealing: Involves repeated heating and cooling cycles to achieve specific material properties.
- Flame Annealing: Uses a direct flame to heat the material, often used for localized annealing.
- Full Annealing: Heats the material to a temperature above its upper critical temperature, followed by slow cooling. This process is used to achieve maximum softness and ductility.
- Graphitizing: A specialized annealing process used for cast iron to convert cementite into graphite, improving machinability and reducing brittleness.
- Intermediate Annealing: Performed between cold working stages to restore ductility and reduce hardness.
- Isothermal Annealing: The material is heated to a specific temperature and then held at that temperature until the desired microstructure is achieved, followed by cooling.
- Process Annealing: A lower temperature annealing process used to relieve stresses in cold-worked materials without significantly altering their microstructure.
- Quench Annealing: Involves rapid cooling after heating, often used for stainless steels to achieve a specific microstructure.
- Spheroidizing: A process used to produce a spheroidal microstructure in high-carbon steels, improving machinability and reducing brittleness.
-
Applications of Annealing:
- Improving Machinability: Annealing softens materials, making them easier to machine.
- Facilitating Cold Working: By reducing hardness, annealing makes materials more amenable to cold working processes like rolling or drawing.
- Enhancing Mechanical Properties: Annealing can improve toughness, ductility, and other mechanical properties.
- Increasing Dimensional Stability: By relieving internal stresses, annealing helps maintain the dimensional stability of components.
-
Importance of Controlled Cooling:
- The cooling rate after annealing is critical as it determines the final microstructure and properties of the material. Slow cooling rates are generally used to achieve a soft and ductile material, while faster cooling rates can result in harder and stronger materials.
By understanding the different types of annealing and their specific applications, manufacturers can select the most appropriate process to achieve the desired material properties for their products.
Summary Table:
Type of Annealing | Key Characteristics | Applications |
---|---|---|
Black Annealing | Heating in an open furnace, forms a black oxide layer | Commonly used for steel |
Blue Annealing | Similar to Black Annealing but at lower temperatures, forms a blue oxide layer | Often used for stainless steel |
Box Annealing | Heating in a sealed container to prevent oxidation | Suitable for materials requiring a controlled atmosphere |
Bright Annealing | Conducted in a controlled atmosphere or vacuum to prevent oxidation | Used for stainless steel and non-ferrous metals |
Cycle Annealing | Repeated heating and cooling cycles | Achieves specific material properties |
Flame Annealing | Direct flame heating for localized annealing | Ideal for localized heat treatment |
Full Annealing | Heating above upper critical temperature, followed by slow cooling | Maximizes softness and ductility |
Graphitizing | Converts cementite into graphite in cast iron | Improves machinability and reduces brittleness in cast iron |
Intermediate Annealing | Performed between cold working stages | Restores ductility and reduces hardness |
Isothermal Annealing | Held at a specific temperature until desired microstructure is achieved | Ensures uniform microstructure |
Process Annealing | Lower temperature annealing to relieve stresses in cold-worked materials | Reduces internal stresses without altering microstructure |
Quench Annealing | Rapid cooling after heating | Used for stainless steels to achieve specific microstructures |
Spheroidizing | Produces a spheroidal microstructure in high-carbon steels | Improves machinability and reduces brittleness |
Need help selecting the right annealing process for your materials? Contact our experts today for tailored solutions!