Molybdenum disilicide (MoSi₂) undergoes sintering at temperatures typically ranging from 1500°C to 1900°C, depending on the specific sintering method and conditions. Cold press sintering involves firing the green body at 1500~1900°C in a non-oxidizing atmosphere, while hot press sintering occurs at slightly lower temperatures of 1550~1750°C under pressure. The sintering process is influenced by factors such as the presence of binders, the atmosphere (e.g., hydrogen, nitrogen, or argon), and the addition of materials like SiO₂, which can enhance the working temperature. Proper sintering ensures the material achieves its desired mechanical and thermal properties, making it suitable for high-temperature applications.
Key Points Explained:
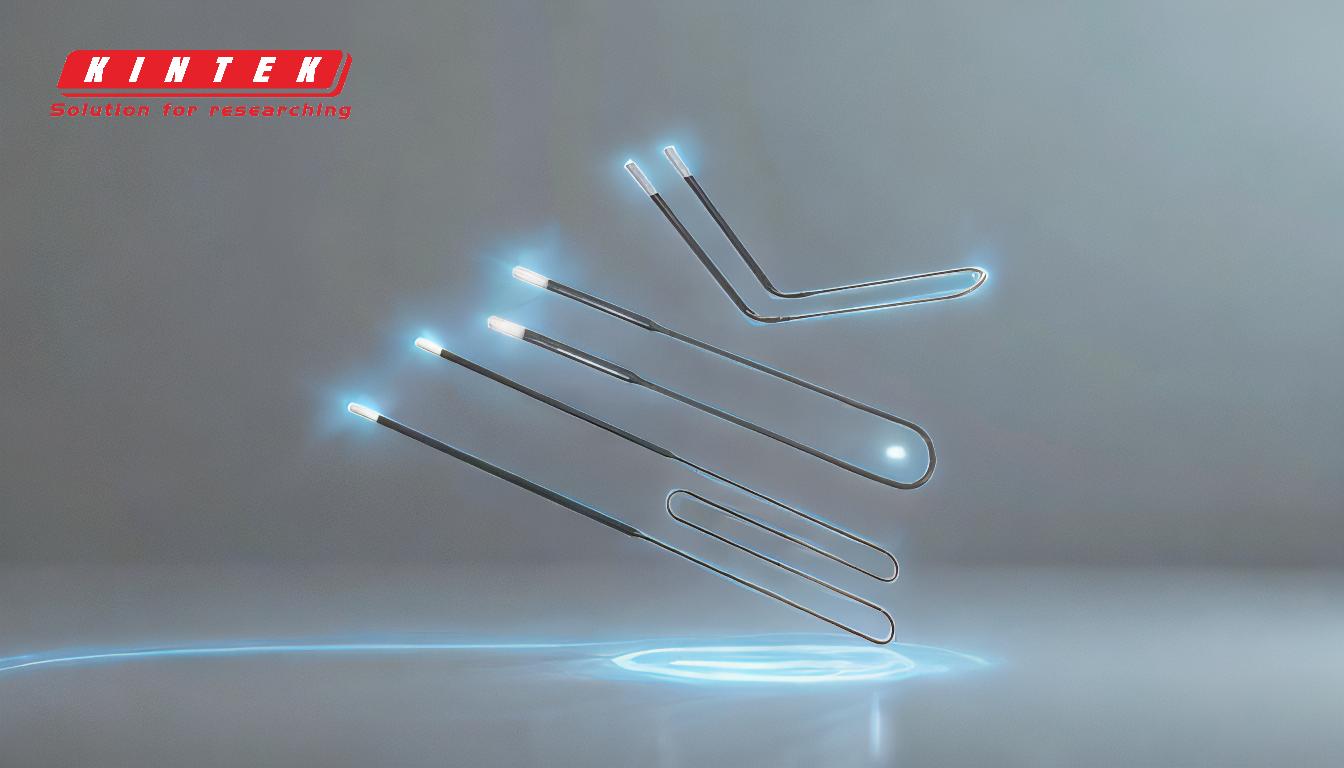
-
Sintering Temperature Range for MoSi₂:
- Molybdenum disilicide typically sinters between 1500°C and 1900°C.
- The exact temperature depends on the sintering method (cold press or hot press) and the specific conditions used during the process.
-
Cold Press Sintering:
- In cold press sintering, the green body is formed under high pressure (80 MPa) and then fired at 1500~1900°C in a non-oxidizing atmosphere (e.g., hydrogen, nitrogen, or argon).
- This method requires the use of binding agents like batter, starch, or glycerin to form the green body.
- Cold-pressed sintered products may have poor mechanical strength, but adding SiO₂ can increase the working temperature to 1710~1780°C.
-
Hot Press Sintering:
- Hot press sintering occurs at 1550~1750°C under a pressure of 10~80 MPa.
- Graphite molds are typically used in this process.
- This method allows for the direct synthesis of materials, and the temperature can be lower if elements are used to synthesize the material directly.
- A mixture of MoSi₂ and alumina (Al₂O₃) can be used to produce materials with varying properties.
-
Importance of Atmosphere:
- Sintering must occur in a non-oxidizing atmosphere (e.g., hydrogen, nitrogen, or argon) to prevent oxidation and ensure proper densification.
- Carbon-containing or neutral atmospheres are unsuitable for sintering MoSi₂.
-
Role of Additives:
- Adding a small amount of SiO₂ can improve the material's performance by increasing its working temperature to 1710~1780°C.
- Additives like Al₂O₃ can also be used to tailor the properties of the final product.
-
Mechanical and Thermal Properties:
- MoSi₂ exhibits excellent high-temperature resistance, corrosion resistance, and thermal shock resistance.
- It forms a protective SiO₂ layer on its surface, which enhances its oxidation resistance and allows it to operate continuously at 1700°C in air for thousands of hours.
-
Challenges and Considerations:
- MoSi₂ is brittle and prone to breaking at high temperatures, which presents challenges during transportation and installation.
- Proper handling and installation techniques are required to mitigate these issues.
By understanding these key points, purchasers and users of MoSi₂ equipment can make informed decisions about the sintering process and ensure the material meets their specific application requirements.
Summary Table:
Aspect | Details |
---|---|
Sintering Temperature | 1500°C to 1900°C (varies by method) |
Cold Press Sintering | 1500~1900°C, non-oxidizing atmosphere, requires binders |
Hot Press Sintering | 1550~1750°C, 10~80 MPa pressure, uses graphite molds |
Atmosphere | Non-oxidizing (e.g., hydrogen, nitrogen, argon) |
Additives | SiO₂ increases working temperature to 1710~1780°C; Al₂O₃ tailors properties |
Key Properties | High-temperature, corrosion, and thermal shock resistance |
Challenges | Brittle at high temperatures; requires careful handling and installation |
Need help optimizing your MoSi₂ sintering process? Contact our experts today for tailored solutions!