PVD (Physical Vapor Deposition) coatings are renowned for their exceptional durability, corrosion resistance, and wear resistance. These coatings are applied in a vacuum environment, which prevents oxidation and contamination, ensuring a strong bond with the substrate material. As a result, PVD coatings are highly resistant to rust and corrosion, making them ideal for applications in harsh environments. However, the rust resistance of a PVD coating also depends on the substrate material and the specific type of coating applied. While PVD coatings themselves do not rust, improper application or damage to the coating can expose the underlying substrate to corrosion.
Key Points Explained:
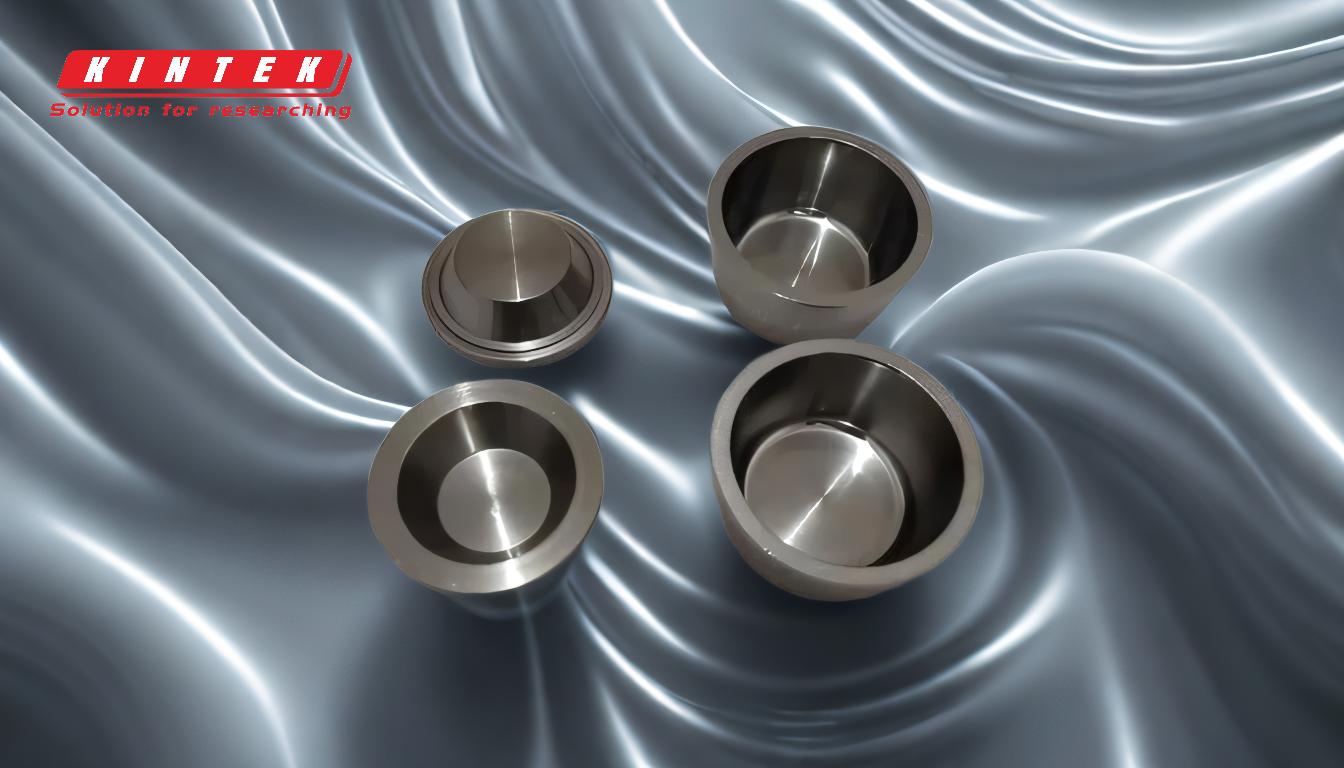
-
PVD Coating Properties and Rust Resistance:
- PVD coatings are known for their high corrosion resistance, which is a key factor in preventing rust.
- The vacuum environment during the PVD process eliminates oxygen and moisture, which are primary causes of oxidation and rust.
- The coatings form a strong, durable bond with the substrate, providing a protective barrier against environmental factors that cause rust.
-
Dependence on Substrate Material:
- The rust resistance of a PVD-coated object also depends on the substrate material. If the substrate is prone to corrosion (e.g., certain types of steel), any damage to the coating can expose the underlying material to rust.
- Proper surface preparation and coating application are critical to ensure the substrate is fully protected.
-
Types of PVD Coatings and Their Effectiveness:
- Different PVD coatings, such as TiN (Titanium Nitride), CrN (Chromium Nitride), and AlTiN (Aluminum Titanium Nitride), offer varying levels of corrosion resistance.
- For example, CrN coatings are particularly known for their excellent corrosion resistance, making them suitable for marine and industrial applications.
-
Real-World Applications:
- PVD coatings are widely used in industries where rust and corrosion resistance are critical, such as automotive, aerospace, and medical devices.
- Their ability to withstand harsh environments and maintain their protective properties over time makes them a reliable choice for equipment and components exposed to moisture and chemicals.
-
Limitations and Maintenance:
- While PVD coatings are highly durable, they are not indestructible. Physical damage, such as scratches or impacts, can compromise the coating and expose the substrate to rust.
- Regular maintenance and inspection are recommended to ensure the integrity of the coating and prevent rust formation.
-
Advantages Over Other Coatings:
- Compared to traditional coatings, PVD coatings offer superior rust resistance due to their hardness, thinness, and strong adhesion to the substrate.
- Their ability to replicate the original finish of materials with minimal effort also makes them aesthetically appealing for applications where appearance matters.
In summary, PVD coatings are highly resistant to rust due to their corrosion-resistant properties and the vacuum application process. However, their effectiveness in preventing rust also depends on the substrate material and proper application. For equipment and consumable purchasers, PVD coatings are a reliable choice for applications requiring durability and rust resistance, provided that the coatings are maintained and inspected regularly to ensure their protective integrity.
Summary Table:
Key Aspect | Details |
---|---|
Rust Resistance | High corrosion resistance due to vacuum application and strong substrate bond. |
Substrate Dependence | Rust resistance depends on the substrate material and proper application. |
Coating Types | TiN, CrN, and AlTiN offer varying levels of corrosion resistance. |
Applications | Used in automotive, aerospace, and medical industries for rust prevention. |
Maintenance | Regular inspection and care are required to maintain coating integrity. |
Advantages | Superior rust resistance, durability, and aesthetic appeal. |
Interested in PVD coatings for rust resistance? Contact us today to learn more!