Yes, an electric furnace, including an electric muffle furnace, can melt steel under the right conditions. However, the ability to melt steel depends on the furnace's temperature range, heating elements, and insulation. Steel typically melts at temperatures between 1370°C and 1540°C (2500°F to 2800°F), so the furnace must be capable of reaching and maintaining these high temperatures. Electric muffle furnaces are primarily designed for applications like annealing, tempering, and material analysis, but certain high-temperature models can achieve the temperatures required for melting steel. Proper safety precautions and equipment specifications must be considered to ensure successful and safe melting.
Key Points Explained:
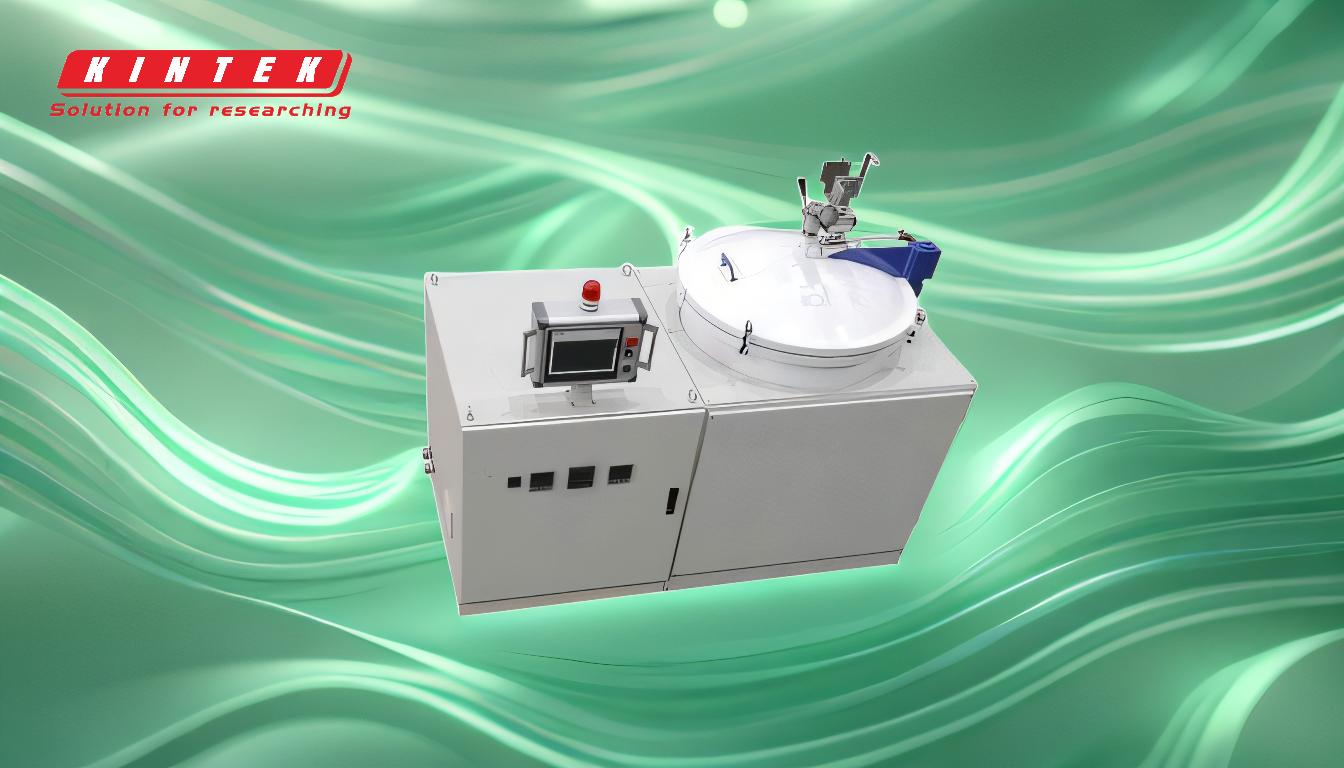
-
Temperature Requirements for Melting Steel:
- Steel melts at temperatures between 1370°C and 1540°C (2500°F to 2800°F). An electric furnace must be capable of reaching and maintaining these temperatures to melt steel effectively.
- Standard electric muffle furnaces are often designed for lower-temperature applications like annealing, tempering, and material analysis. However, specialized high-temperature models can achieve the necessary heat levels for melting steel.
-
Capabilities of Electric Muffle Furnaces:
- Electric muffle furnaces are versatile and used in various industries, including laboratories, food processing, and pharmaceuticals. They are ideal for processes like alkali fusion, flameless ashing, and high-temperature material analysis.
- While they are not primarily designed for melting metals, certain high-temperature models can reach the temperatures needed for melting steel.
-
Heating Elements and Insulation:
- The ability to melt steel depends on the furnace's heating elements and insulation. High-quality heating elements, such as silicon carbide or molybdenum disilicide, are required to sustain the extreme temperatures needed.
- Proper insulation ensures heat retention and energy efficiency, which are critical for maintaining the high temperatures required for melting steel.
-
Safety Considerations:
- Melting steel in an electric furnace requires careful safety measures. The furnace must be equipped with temperature controls and safety features to prevent overheating or damage.
- Operators should wear protective gear and follow safety protocols to handle molten steel safely.
-
Applications Beyond Melting:
- While an electric muffle furnace can melt steel, its primary applications include annealing, tempering, and material analysis. It is also used for processes like brazing, ash melting point analysis, and quality control in various industries.
-
Alternative Furnaces for Melting Steel:
- If the primary goal is to melt steel, other types of furnaces, such as induction furnaces or arc furnaces, may be more suitable. These furnaces are specifically designed for high-temperature metal melting and offer better efficiency for such tasks.
In conclusion, while an electric muffle furnace can melt steel, it is not the most efficient or common choice for this purpose. Specialized high-temperature models are required, and safety precautions must be strictly followed. For frequent or large-scale steel melting, alternative furnace types may be more appropriate.
Summary Table:
Key Factor | Details |
---|---|
Melting Temperature | 1370°C to 1540°C (2500°F to 2800°F) |
Furnace Requirements | High-temperature models with quality heating elements and insulation |
Primary Applications | Annealing, tempering, material analysis |
Safety Considerations | Temperature controls, protective gear, and safety protocols required |
Alternative Furnaces | Induction or arc furnaces for efficient steel melting |
Need help choosing the right furnace for your needs? Contact our experts today!