Brazing and welding are both joining processes, but they differ significantly in terms of strength, application, and methodology. Brazing involves joining materials by melting a filler metal into the joint without melting the base materials, while welding involves melting the base materials to form a joint. While brazing can produce strong joints, it generally does not match the strength of welding, especially in high-stress applications. However, brazing offers advantages such as lower heat input, reduced distortion, and the ability to join dissimilar materials. The strength of a brazed joint depends on factors like joint design, filler metal properties, and surface preparation.
Key Points Explained:
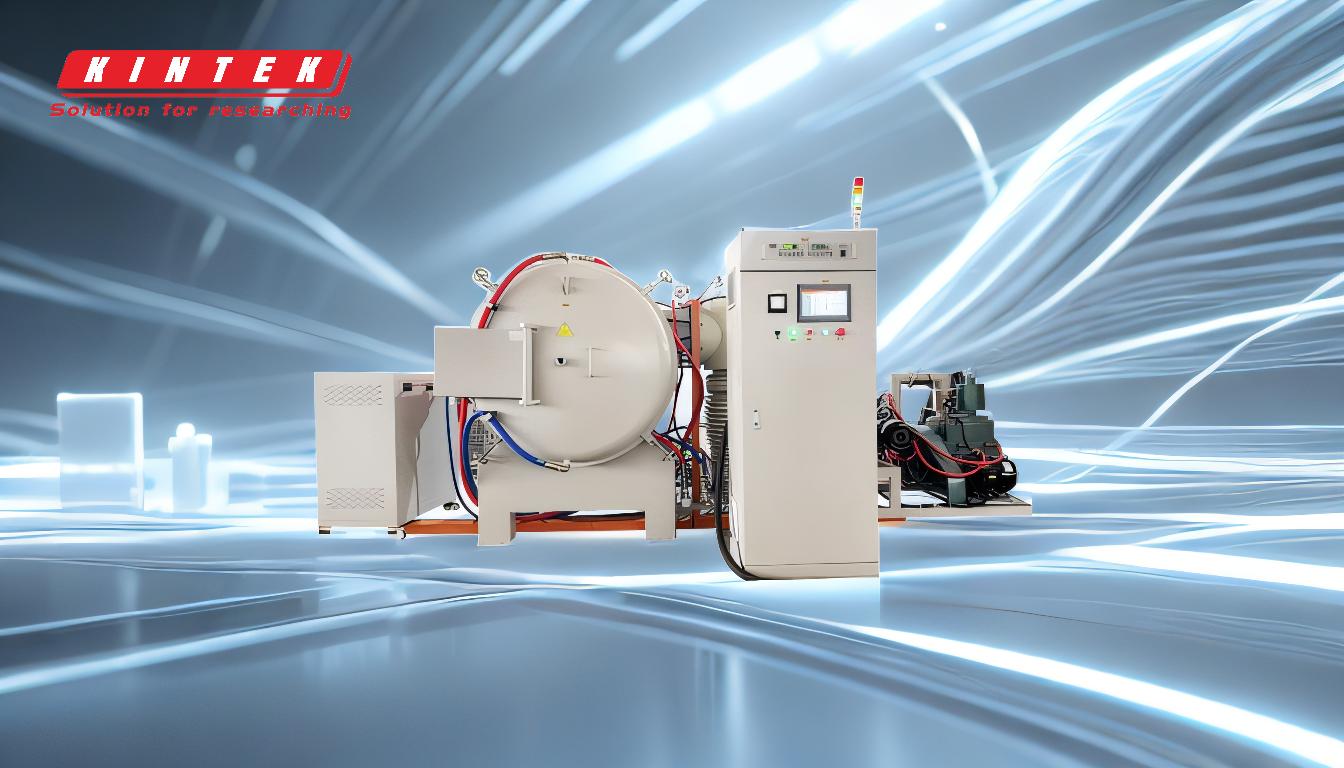
-
Fundamental Differences Between Brazing and Welding:
- Brazing: Uses a filler metal with a lower melting point than the base materials. The base materials do not melt, and the joint is formed through capillary action.
- Welding: Involves melting the base materials to create a fusion joint, often resulting in a stronger bond due to the metallurgical integration of the materials.
-
Strength Comparison:
- Welding Strength: Welded joints typically have higher tensile strength and are better suited for high-stress applications because the base materials are fused together.
- Brazing Strength: Brazed joints are generally strong but not as strong as welded joints. The strength of a brazed joint depends on the filler metal and joint design. For example, a well-designed lap joint in brazing can distribute stress effectively, but it may still fall short of the strength of a welded butt joint.
-
Factors Affecting Brazing Strength:
- Joint Design: Proper joint design, such as lap joints or scarf joints, can enhance the strength of brazed connections by increasing the surface area for bonding.
- Filler Metal: The choice of filler metal (e.g., silver-based, copper-based, or nickel-based alloys) significantly impacts the joint's strength and thermal properties.
- Surface Preparation: Clean and properly prepared surfaces ensure better wetting and bonding of the filler metal, leading to stronger joints.
-
Advantages of Brazing Over Welding:
- Lower Heat Input: Brazing requires less heat, reducing the risk of warping or distortion in the base materials.
- Joining Dissimilar Materials: Brazing can join metals with different melting points, such as copper to steel, which is challenging with welding.
- Complex Geometries: Brazing is suitable for intricate joint designs where welding might be impractical.
-
Applications Where Brazing is Preferred:
- Electronics: Brazing is commonly used in electronics for joining components without damaging sensitive parts.
- Automotive: In automotive manufacturing, brazing is used for joining dissimilar materials like aluminum and steel.
- HVAC Systems: Brazing is ideal for joining copper tubes in refrigeration and air conditioning systems.
-
Limitations of Brazing:
- Temperature Sensitivity: Brazed joints may weaken at high temperatures, making them unsuitable for high-temperature applications.
- Stress Resistance: Brazed joints are less capable of handling high-stress environments compared to welded joints.
In conclusion, while brazing can produce strong and reliable joints, it generally does not match the strength of welding, particularly in high-stress or high-temperature applications. However, brazing offers unique advantages in specific scenarios, such as joining dissimilar materials or working with complex geometries. The choice between brazing and welding ultimately depends on the specific requirements of the application.
Summary Table:
Aspect | Brazing | Welding |
---|---|---|
Process | Uses filler metal; base materials do not melt | Melts base materials to form a fusion joint |
Strength | Strong but generally weaker than welding; depends on joint design | Typically stronger, especially in high-stress applications |
Heat Input | Lower heat input, reducing distortion | Higher heat input, may cause warping |
Material Compatibility | Can join dissimilar materials (e.g., copper to steel) | Limited to similar materials with close melting points |
Applications | Electronics, automotive, HVAC systems | High-stress environments, heavy-duty applications |
Limitations | Weaker at high temperatures; less stress-resistant | Requires higher skill; may damage sensitive components |
Need help choosing between brazing and welding for your project? Contact our experts today for tailored advice!