Calcination can indeed be performed in a muffle furnace, as it is a heat treatment process that requires high temperatures and controlled conditions. Muffle furnaces are well-suited for this purpose due to their ability to generate and maintain high temperatures in an isolated environment, preventing contamination and ensuring uniform heating. The furnace's design, which includes refractory materials and heating elements, allows for precise temperature control, making it ideal for processes like calcination that involve thermal decomposition or the removal of volatile substances. Below, the key points explaining why and how calcination can be done in a muffle furnace are detailed.
Key Points Explained:
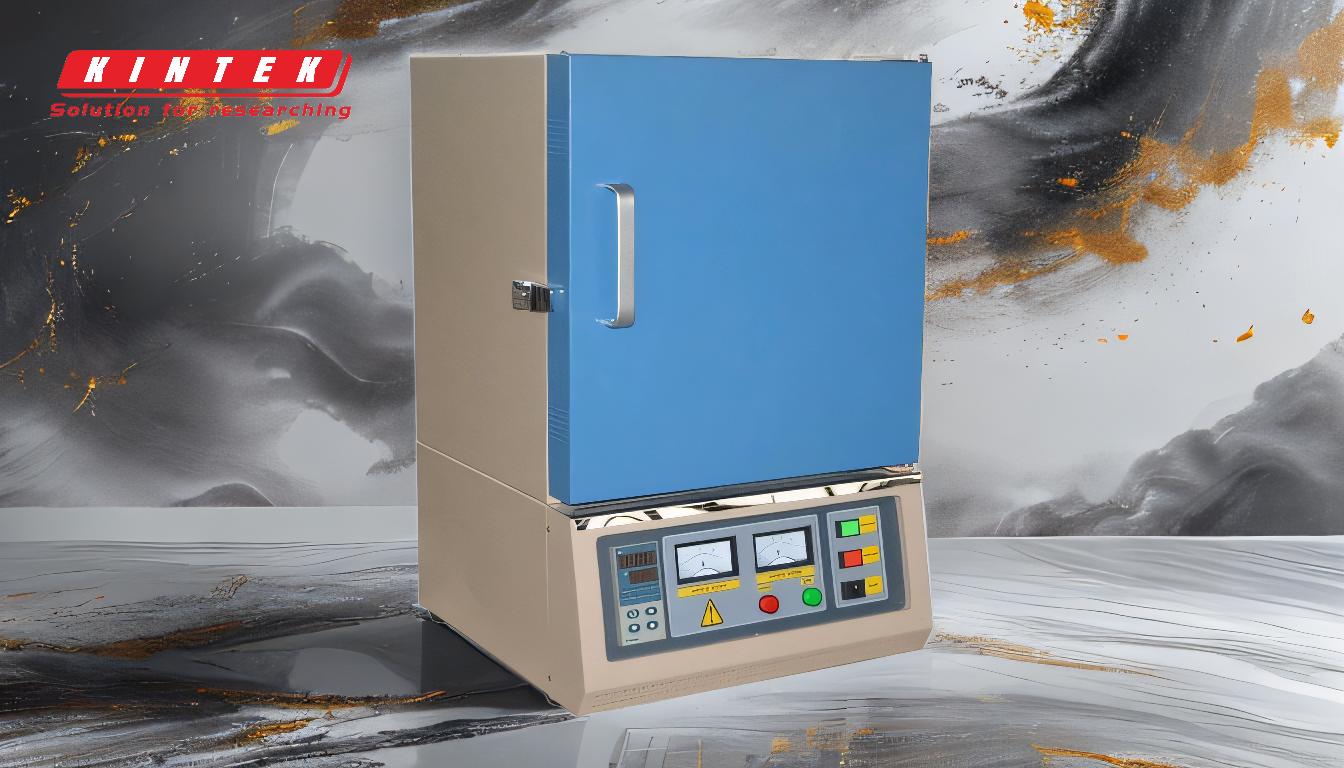
-
Definition and Purpose of Calcination
- Calcination is a thermal treatment process where materials are heated to high temperatures (below their melting point) to induce thermal decomposition, remove volatile components, or transform chemical and physical properties.
- Common applications include extracting metals from ores, decomposing carbonates, and preparing materials for further processing.
- The process often requires an oxygen-free or controlled atmosphere to prevent oxidation or unwanted reactions.
-
Muffle Furnace Design and Functionality
- A muffle furnace is designed to heat materials in an isolated chamber, separating the sample from combustion byproducts or external contaminants.
- It uses heating elements (e.g., Nichrome) located outside the muffle chamber to heat the walls, which then radiate heat to the sample inside.
- The chamber is lined with refractory materials like ceramic fiber or bricks to insulate and minimize heat loss, ensuring efficient and uniform heating.
- Modern muffle furnaces are equipped with PID controllers and thermocouples for precise temperature regulation, which is critical for calcination.
-
Advantages of Using a Muffle Furnace for Calcination
- Temperature Control: Muffle furnaces can achieve and maintain the high temperatures required for calcination (often up to 1200°C or higher).
- Isolation: The closed chamber prevents contamination from external factors, ensuring the purity of the calcined product.
- Uniform Heating: The design promotes even heat distribution, which is essential for consistent results.
- Energy Efficiency: Modern muffle furnaces are designed to be energy-efficient, reducing operational costs.
-
Comparison with Traditional Calciners
- Traditional calciners are cylindrical reactors specifically designed for calcination, often used in industrial settings.
- While calciners are optimized for large-scale operations, muffle furnaces are more versatile and suitable for smaller-scale or laboratory applications.
- Muffle furnaces offer better control over temperature and atmosphere, making them ideal for research and development or precision processes.
-
Process of Calcination in a Muffle Furnace
- Sample Preparation: The material to be calcined is placed in a crucible or container suitable for high temperatures.
- Loading: The sample is loaded into the muffle chamber, ensuring it is positioned for optimal heat exposure.
- Heating: The furnace is set to the desired temperature, and the PID controller ensures precise heating.
- Duration: The sample is held at the target temperature for a specific period to achieve the desired chemical or physical transformation.
- Cooling: After calcination, the furnace is allowed to cool, and the sample is removed for further analysis or use.
-
Applications of Calcination in a Muffle Furnace
- Metallurgy: Extracting metals from ores by decomposing metal oxides or carbonates.
- Ceramics: Preparing raw materials for ceramic production by removing volatile components.
- Chemical Industry: Producing catalysts or other materials with specific properties.
- Research: Studying thermal decomposition or phase transitions in materials.
-
Considerations for Using a Muffle Furnace
- Temperature Range: Ensure the furnace can reach the required temperature for the specific calcination process.
- Atmosphere Control: Some calcination processes may require an inert or controlled atmosphere, which can be achieved with additional accessories.
- Sample Size: The furnace's chamber size should accommodate the sample volume without compromising heating uniformity.
- Safety: Proper ventilation and handling of high-temperature materials are essential to prevent accidents.
In summary, a muffle furnace is an excellent tool for calcination due to its ability to provide high temperatures, precise control, and an isolated environment. While traditional calciners are used for large-scale industrial processes, muffle furnaces are ideal for smaller-scale, laboratory, or research applications where precision and versatility are critical. By understanding the process and the furnace's capabilities, users can effectively perform calcination to achieve desired material transformations.
Summary Table:
Key Aspect | Details |
---|---|
Definition of Calcination | Thermal process for decomposition, removal of volatiles, or property changes. |
Muffle Furnace Design | Isolated chamber, refractory lining, PID controllers for precise heating. |
Advantages | High temperature control, uniform heating, energy efficiency, isolation. |
Applications | Metallurgy, ceramics, chemical industry, research. |
Considerations | Temperature range, atmosphere control, sample size, safety measures. |
Discover how a muffle furnace can optimize your calcination process—contact us today for expert guidance!