Diamond-like carbon (DLC) coatings are highly versatile and widely used across industries due to their unique combination of hardness, low friction, and chemical inertness. While DLC is commonly applied to materials like steel, silicon, and polymers, the question arises whether it can be effectively applied to aluminum. The answer is yes, but with certain considerations. Aluminum's lower melting point and softer surface compared to steel or silicon require specialized deposition techniques, such as Plasma-Enhanced Chemical Vapor Deposition (PECVD) or Physical Vapor Deposition (PVD), to ensure proper adhesion and performance. DLC coatings on aluminum can enhance wear resistance, reduce friction, and provide corrosion protection, making them suitable for applications in automotive, aerospace, and optical industries. However, challenges such as thermal mismatch and surface preparation must be addressed to achieve optimal results.
Key Points Explained:
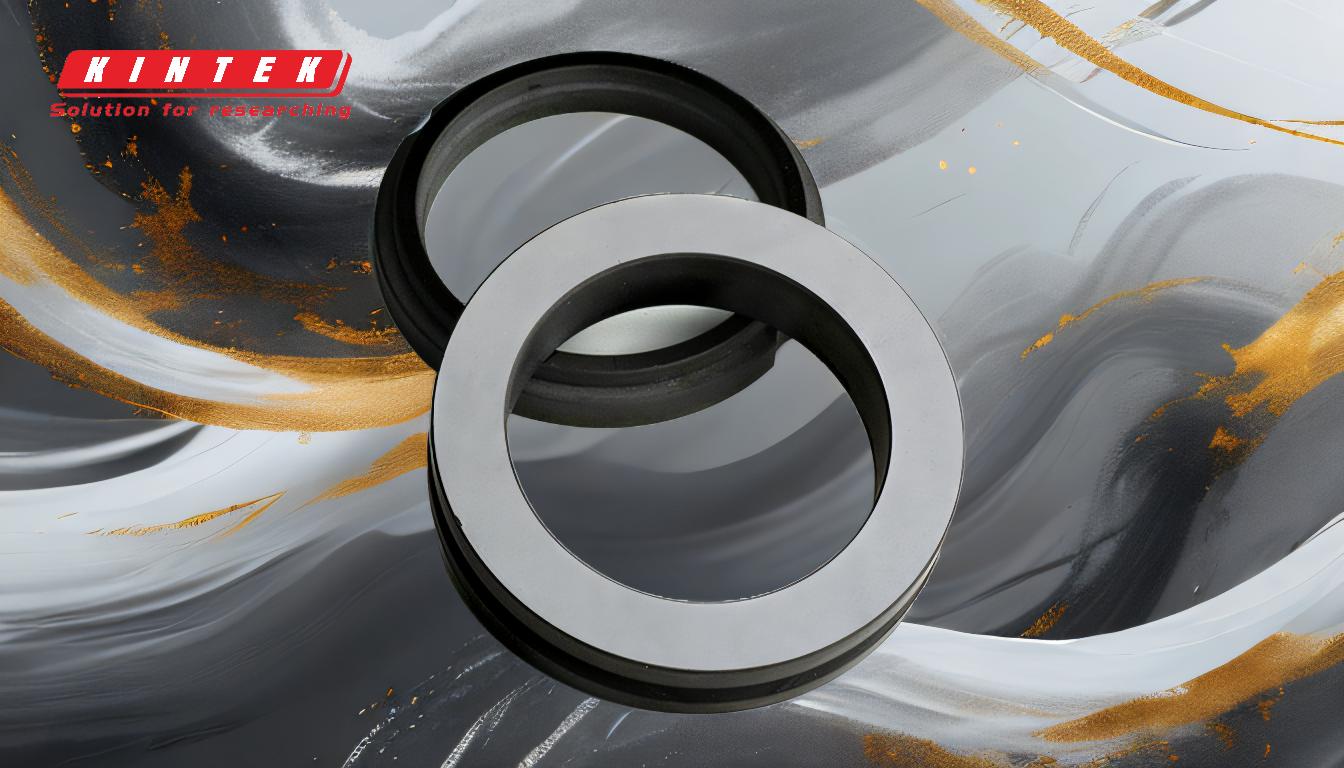
-
What is DLC?
- DLC is an amorphous carbon coating that combines the hardness of diamond with the lubricity of graphite.
- It is used in wear-protective applications, optical coatings, and tribological systems due to its high hardness (1500–3000 HV), low friction, and chemical inertness.
-
Can DLC be applied to aluminum?
- Yes, DLC can be applied to aluminum, but it requires careful consideration of the deposition process and surface preparation.
- Aluminum's lower melting point and softer surface compared to steel or silicon necessitate specialized techniques like PECVD or PVD to ensure proper adhesion and performance.
-
Challenges of applying DLC to aluminum:
- Thermal mismatch: Aluminum has a higher coefficient of thermal expansion than DLC, which can lead to delamination or cracking under thermal stress.
- Surface preparation: Aluminum surfaces must be thoroughly cleaned and often pre-treated (e.g., with an intermediate layer or plasma activation) to improve adhesion.
- Deposition temperature: Techniques like PECVD, which operate at lower temperatures, are preferred to avoid distorting the aluminum substrate.
-
Benefits of DLC coatings on aluminum:
- Wear resistance: DLC enhances the durability of aluminum components, making them suitable for high-wear applications like automotive parts or machinery.
- Friction reduction: The low coefficient of friction of DLC improves the sliding properties of aluminum components, reducing energy loss and wear.
- Corrosion protection: DLC provides a barrier against chemical and environmental degradation, extending the lifespan of aluminum parts.
- Decorative applications: DLC can be used for black coatings with a luxurious finish, combining aesthetics with functional properties.
-
Applications of DLC-coated aluminum:
- Automotive: DLC-coated aluminum components, such as pistons, camshafts, and bearings, benefit from reduced friction and wear.
- Aerospace: Lightweight aluminum parts with DLC coatings are used in aircraft engines and structural components to improve performance and longevity.
- Optical devices: DLC is applied to aluminum mirrors and lenses as a protective and antireflective coating.
- Medical implants: DLC-coated aluminum is used in biocompatible medical devices due to its chemical inertness and biocompatibility.
-
Deposition techniques for DLC on aluminum:
- PECVD (Plasma-Enhanced Chemical Vapor Deposition): Ideal for aluminum due to its low deposition temperature, scalability, and ability to produce high-quality, adherent coatings.
- PVD (Physical Vapor Deposition): Suitable for creating thin, hard DLC films on aluminum with precise control over thickness and properties.
- Surface pre-treatment: Techniques like plasma activation or intermediate layers (e.g., silicon or chromium) are often used to improve adhesion between DLC and aluminum.
-
Future prospects and challenges:
- While DLC coatings on aluminum offer significant benefits, further research is needed to optimize adhesion and address thermal mismatch issues.
- Advances in deposition technologies and surface engineering may expand the use of DLC-coated aluminum in new applications, such as renewable energy systems and advanced manufacturing tools.
In conclusion, DLC can be successfully applied to aluminum, but it requires careful selection of deposition techniques and surface preparation methods. The resulting coatings provide significant functional and aesthetic benefits, making DLC-coated aluminum a valuable material for industries ranging from automotive to medical.
Summary Table:
Key Aspect | Details |
---|---|
What is DLC? | Amorphous carbon coating combining diamond hardness and graphite lubricity. |
Can DLC be applied to Al? | Yes, with specialized techniques like PECVD or PVD. |
Challenges | Thermal mismatch, surface preparation, and deposition temperature control. |
Benefits | Wear resistance, friction reduction, corrosion protection, and aesthetics. |
Applications | Automotive, aerospace, optical devices, and medical implants. |
Deposition Techniques | PECVD and PVD, with surface pre-treatment for better adhesion. |
Discover how DLC coatings can transform your aluminum components—contact our experts today!