Grain growth can indeed affect the sintering rate, as it is closely tied to the microstructure evolution during the process. Sintering involves the densification of powdered materials through heat and sometimes pressure, leading to the formation of a solid structure. Grain growth, which refers to the increase in grain size within the material, can influence the kinetics of sintering by altering the diffusion pathways and the overall energy landscape of the system. Larger grains can reduce the driving force for sintering by decreasing the surface area and grain boundary energy, which are critical for material transport and densification. Conversely, controlled grain growth can enhance densification by optimizing the balance between surface energy reduction and pore elimination. The interplay between grain growth and sintering rate is complex and depends on factors such as temperature, particle size, and the presence of a liquid phase.
Key Points Explained:
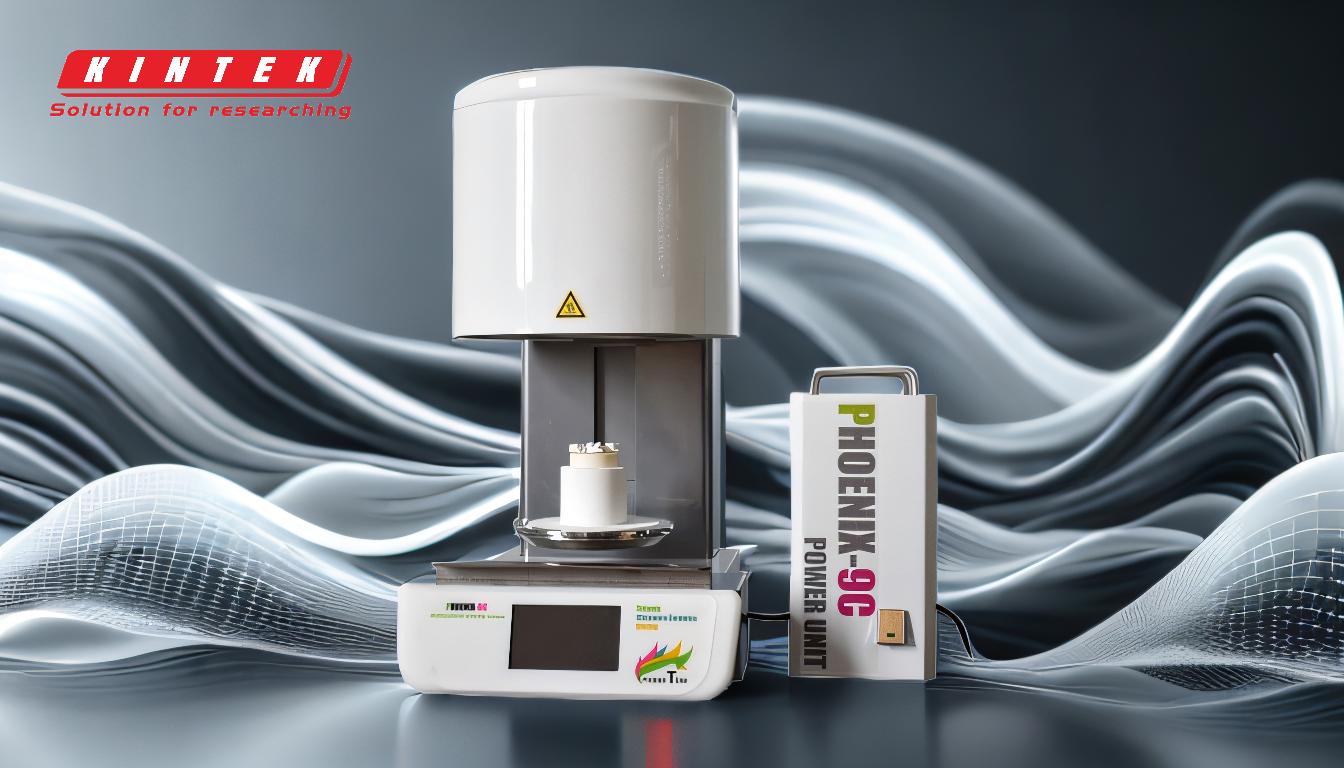
-
Grain Growth and Sintering Kinetics:
- Grain growth occurs when smaller grains merge to form larger ones, reducing the total grain boundary area.
- This process affects sintering kinetics because grain boundaries are primary pathways for atomic diffusion, which is essential for densification.
- As grains grow, the driving force for sintering (surface energy reduction) diminishes, potentially slowing down the sintering rate.
-
Temperature and Grain Growth:
- Higher sintering temperatures accelerate grain growth due to increased atomic mobility.
- While this can enhance densification initially, excessive grain growth can lead to coarsening, where pores become trapped within grains, hindering further densification.
- Optimal temperature control is crucial to balance grain growth and sintering rate.
-
Particle Size and Grain Growth:
- Smaller particles have higher surface energy, promoting faster sintering and finer grain structures.
- However, fine particles are also more prone to rapid grain growth, which can counteract the benefits of high surface energy.
- Controlling particle size distribution is key to managing grain growth and sintering behavior.
-
Liquid Phase Sintering:
- The presence of a liquid phase can significantly accelerate sintering by enhancing material transport and reducing the activation energy for grain boundary movement.
- However, excessive liquid phase can lead to uncontrolled grain growth and uneven densification.
- Careful regulation of the liquid phase content is necessary to optimize sintering outcomes.
-
Pressure-Assisted Sintering:
- Applying external pressure during sintering can counteract the negative effects of grain growth by promoting particle rearrangement and pore elimination.
- Techniques like hot pressing or spark plasma sintering (SPS) combine pressure and heat to achieve high-density materials with controlled grain structures.
-
Impact on Final Material Properties:
- Grain growth affects not only the sintering rate but also the mechanical, thermal, and electrical properties of the final product.
- Excessive grain growth can lead to reduced strength and toughness due to the presence of large grains and residual porosity.
- Optimal sintering conditions aim to achieve a fine, uniform grain structure for superior material performance.
-
Practical Considerations for Equipment and Consumables:
- For equipment and consumables purchasers, understanding the relationship between grain growth and sintering rate is critical for selecting appropriate materials and processes.
- Factors such as furnace type, heating rate, and atmosphere control must be tailored to the specific material and desired properties.
- Advanced sintering techniques, such as field-assisted sintering, may offer better control over grain growth and densification, leading to higher-quality products.
In summary, grain growth is a critical factor in sintering that can either enhance or hinder the process depending on how it is managed. By carefully controlling temperature, particle size, and the presence of a liquid phase, it is possible to optimize the sintering rate and achieve the desired material properties. For equipment and consumables purchasers, this understanding is essential for making informed decisions about sintering processes and materials.
Summary Table:
Factor | Impact on Sintering | Key Consideration |
---|---|---|
Grain Growth | Reduces surface area and grain boundary energy, slowing sintering kinetics. | Controlled growth enhances densification; excessive growth hinders it. |
Temperature | Higher temperatures accelerate grain growth and densification. | Optimal temperature control balances growth and densification. |
Particle Size | Smaller particles sinter faster but are prone to rapid grain growth. | Manage particle size distribution to control grain growth. |
Liquid Phase | Enhances material transport but can lead to uncontrolled grain growth. | Regulate liquid phase content for optimal sintering. |
Pressure-Assisted | Promotes particle rearrangement and pore elimination, counteracting grain growth. | Techniques like hot pressing or SPS improve densification and grain control. |
Final Properties | Excessive grain growth reduces strength and toughness; fine grains improve performance. | Aim for a fine, uniform grain structure for superior material properties. |
Equipment Selection | Tailor furnace type, heating rate, and atmosphere to material and desired properties. | Advanced techniques like field-assisted sintering offer better grain growth control. |
Ready to optimize your sintering process? Contact our experts today to achieve superior material properties!