Yes, PVD (Physical Vapor Deposition) coating can be applied to aluminum. PVD coatings are highly versatile and can be deposited on various substrates, including metals like aluminum, to enhance their surface properties. Aluminum, being a lightweight and widely used material in industries such as aerospace, automotive, and consumer electronics, benefits significantly from PVD coatings. These coatings improve aluminum's hardness, wear resistance, corrosion resistance, and aesthetic appeal. The process involves depositing a thin layer of material (ranging from 0.5 to 5 microns) onto the aluminum surface using techniques such as cathode arc evaporation, magnetron sputtering, or electron beam evaporation. PVD coatings on aluminum are used in applications like automotive parts, aerospace components, and consumer electronics, where durability and performance are critical.
Key Points Explained:
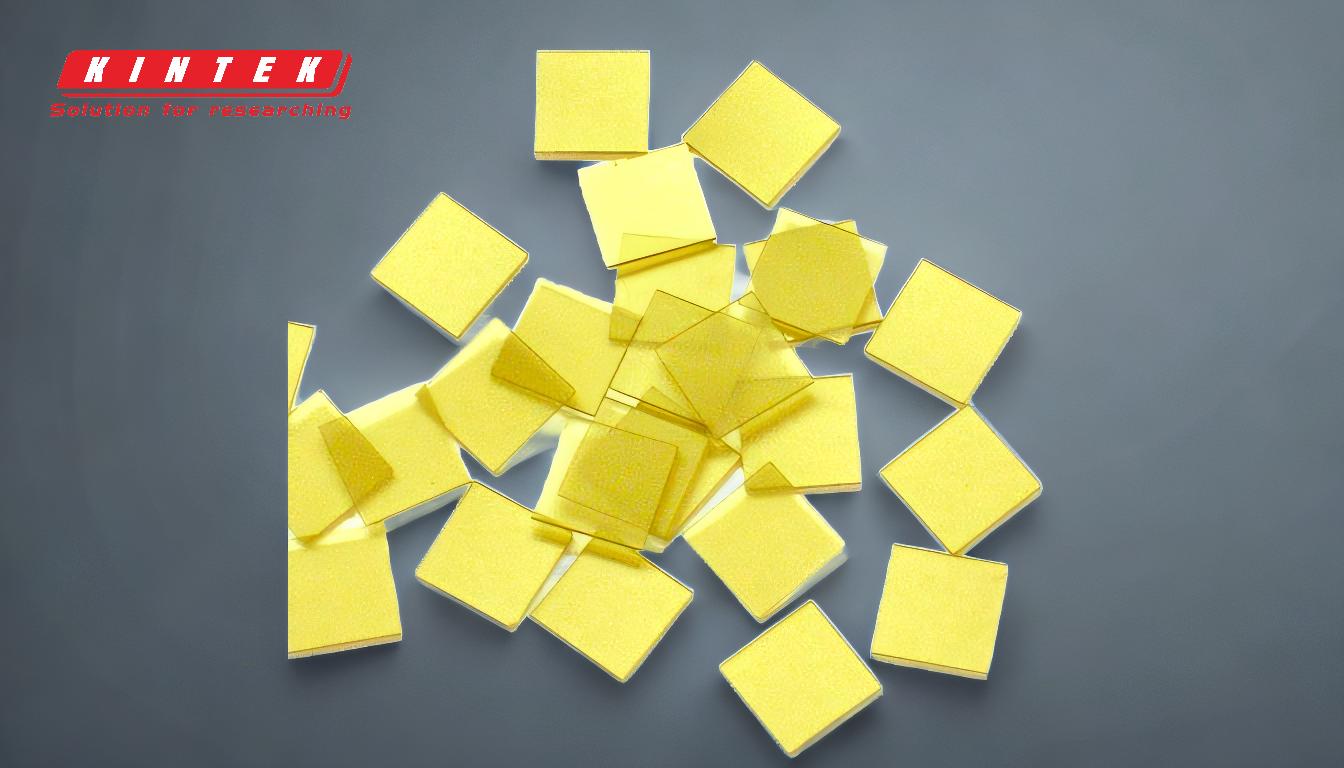
-
PVD Coating Compatibility with Aluminum
- PVD coatings can be applied to aluminum due to its compatibility with a wide range of substrates, including metals, polymers, and ceramics.
- Aluminum's surface properties, such as its lightweight nature and corrosion resistance, make it an ideal candidate for PVD coating to further enhance its performance.
-
Benefits of PVD Coating on Aluminum
- Improved Hardness and Wear Resistance: PVD coatings like titanium nitride (TiN) or chromium nitride (CrN) significantly increase the surface hardness of aluminum, making it more resistant to wear and abrasion.
- Enhanced Corrosion Resistance: The thin, dense layers of PVD coatings protect aluminum from oxidation and corrosion, extending its lifespan in harsh environments.
- Aesthetic Appeal: PVD coatings can replicate finishes such as gold, black, or metallic colors, enhancing the visual appeal of aluminum products.
- Environmental Benefits: PVD is a greener alternative to traditional plating methods like chrome plating, as it avoids the use of toxic chemicals.
-
Applications of PVD-Coated Aluminum
- Aerospace: Aluminum components coated with PVD are used in aircraft parts to improve durability and resistance to extreme conditions.
- Automotive: PVD coatings are applied to aluminum wheels, pistons, and other parts to enhance performance and longevity.
- Consumer Electronics: Aluminum casings for smartphones, laptops, and other devices are often PVD-coated for both durability and aesthetic purposes.
- Medical Devices: Surgical tools and implants made from aluminum benefit from PVD coatings due to their biocompatibility and resistance to wear.
-
PVD Coating Techniques for Aluminum
- Cathode Arc Evaporation: This method uses an electric arc to vaporize the coating material, which then deposits onto the aluminum surface.
- Magnetron Sputtering: A high-energy plasma is used to eject atoms from the target material, which then form a thin film on the aluminum substrate.
- Electron Beam Evaporation: An electron beam heats the coating material, causing it to vaporize and deposit onto the aluminum.
-
Challenges and Considerations
- Surface Preparation: Aluminum surfaces must be thoroughly cleaned and sometimes pre-treated to ensure proper adhesion of the PVD coating.
- Coating Thickness: The thin nature of PVD coatings (0.5 to 5 microns) requires precise control to achieve the desired properties without compromising the substrate's integrity.
- Cost: While PVD coating offers numerous benefits, it can be more expensive than traditional coating methods, depending on the complexity of the process and the materials used.
-
Performance Enhancements
- Studies have shown that PVD coatings can significantly improve the fatigue limit and endurance of aluminum alloys, making them suitable for high-stress applications.
- The hardness of the coating plays a critical role in determining its durability, with materials like TiN and CrN being popular choices for aluminum substrates.
-
Future Trends
- The use of PVD coatings on aluminum is expected to grow, particularly in industries like renewable energy (e.g., solar panels) and advanced electronics, where lightweight, durable materials are in high demand.
- Ongoing research aims to develop new PVD coating materials and techniques to further enhance the performance of aluminum in various applications.
By leveraging PVD coatings, aluminum can be transformed into a high-performance material suitable for a wide range of demanding applications, combining durability, aesthetics, and environmental sustainability.
Summary Table:
Aspect | Details |
---|---|
Compatibility | PVD coatings are compatible with aluminum, enhancing its surface properties. |
Benefits | Improved hardness, wear resistance, corrosion resistance, and aesthetic appeal. |
Applications | Aerospace, automotive, consumer electronics, and medical devices. |
Techniques | Cathode arc evaporation, magnetron sputtering, and electron beam evaporation. |
Challenges | Surface preparation, precise coating thickness, and cost considerations. |
Future Trends | Growth in renewable energy and advanced electronics industries. |
Unlock the potential of PVD-coated aluminum for your projects—contact us today to learn more!