Yes, you can braze under a vacuum, and this process is known as vacuum brazing. It is a highly effective method for joining metals, especially in industries where precision, cleanliness, and high-quality joints are critical. Vacuum brazing involves heating the materials in a vacuum environment, which prevents oxidation and contamination, leading to superior joint quality. This method is widely used in industries such as aerospace, medical, and semiconductor manufacturing due to its ability to produce clean, strong, and precise joints without the need for post-processing.
Key Points Explained:
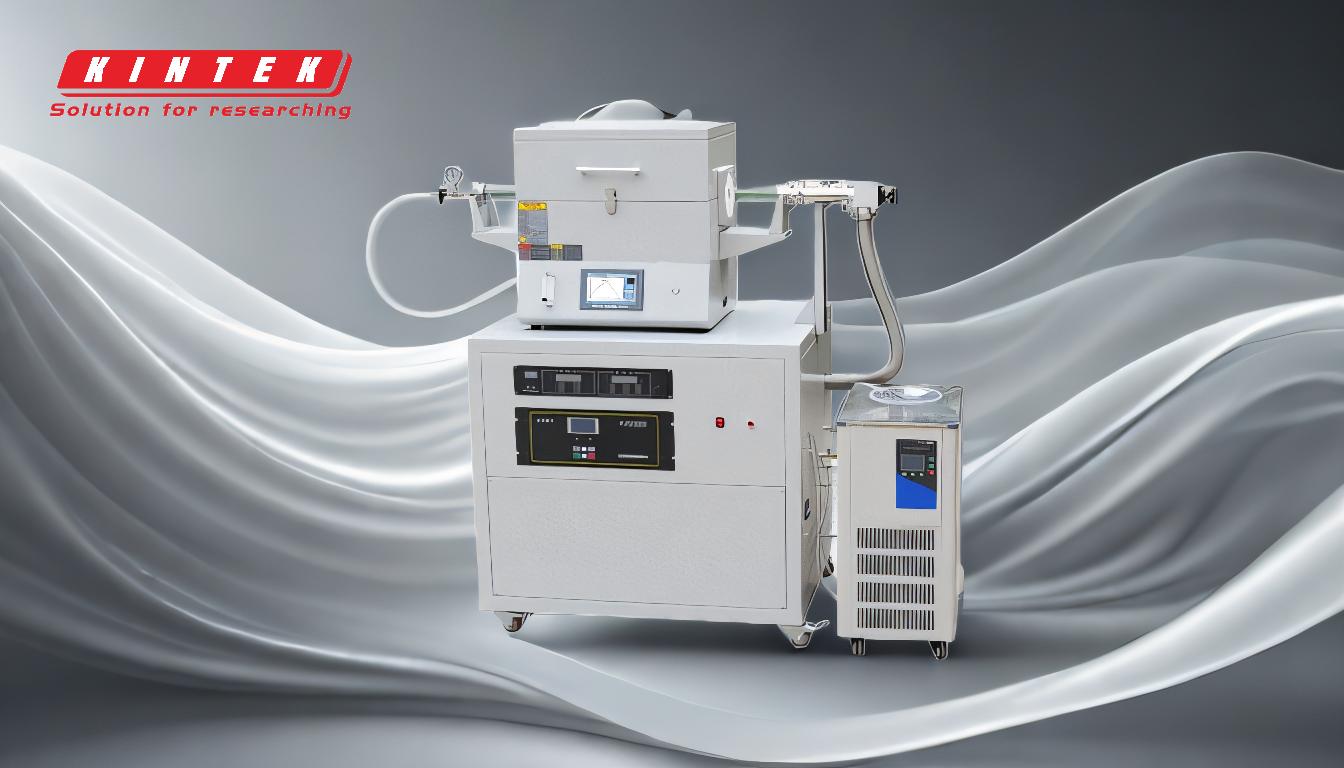
-
What is Vacuum Brazing?
- Vacuum brazing is a process where two metal pieces are joined by heating them just below their melting points and using a filler metal to create a smooth, flawless joint. The process takes place in a vacuum environment, which eliminates the presence of air and other gases that could cause oxidation or contamination.
-
Advantages of Vacuum Brazing:
- Multiple Seam Welding: Vacuum brazing allows for the simultaneous welding of multiple seams, which increases efficiency.
- Minimal Deformation: The process results in minimal deformation under high pressure, ensuring the integrity of the parts.
- Uniform Heating: The uniform heating provided by the vacuum environment ensures consistent thermal stress distribution.
- No Oxidation or Contamination: The vacuum environment prevents oxidation and contamination, leading to high-quality joints.
- Complex Designs: The ability to design complex runways allows for superior product performance.
-
Vacuum Brazing Furnace Components:
- Vacuum System: The vacuum system in a vacuum brazing furnace includes components such as vacuum valves, mechanical pumps, diffusion pumps, and Roots pumps. These components work together to achieve the required vacuum level, which is typically around 7 × 10^-3 Pa.
- Heating System: The heating system is responsible for heating the parts and melting the brazing material to complete the brazing process. The temperature is controlled automatically by a temperature control instrument.
-
Working Principle of Vacuum Brazing:
- The process begins by placing the assembled workpiece into the vacuum chamber.
- The mechanical vacuum pump is started to evacuate the air from the chamber.
- Once a certain vacuum level is reached, the diffusion pump is connected to achieve a higher vacuum.
- The workpiece is then heated while maintaining the vacuum, allowing the brazing material to melt and flow into the joint.
- After the brazing is complete, the workpiece is cooled to a safe temperature before removal to avoid oxidation.
-
Applications of Vacuum Brazing:
- Aerospace: Vacuum brazing is used to create strong, lightweight joints in aerospace components.
- Medical: The clean, precise nature of vacuum brazing makes it ideal for medical devices.
- Semiconductor: The semiconductor industry benefits from the tight tolerances and high-quality joints produced by vacuum brazing.
-
Comparison with Other Brazing Methods:
- Furnace Brazing: In furnace brazing, the entire assembly is heated to a temperature where the braze alloy melts and flows into the joint. While this method allows for the simultaneous creation of many joints, it does not offer the same level of cleanliness and precision as vacuum brazing.
- Vacuum Sintering: Vacuum sintering involves placing ceramic materials in a furnace and evacuating the air to create a vacuum state. The furnace is then heated to high temperatures, allowing chemical reactions and crystallization to occur. While similar in its use of a vacuum environment, vacuum sintering is primarily used for ceramics rather than metal joining.
-
Benefits of Vacuum Brazing:
- Clean Process: The vacuum environment removes oxides and prevents undesirable reactions, resulting in high-quality braze-joints.
- Time and Cost Savings: The ability to hold tight tolerances and produce bright, clean parts without post-processing saves time and reduces costs.
- Superior Product Performance: The uniform heating and controlled thermal stress lead to superior product performance, especially in complex designs.
In conclusion, vacuum brazing is a highly effective method for joining metals, offering numerous advantages over traditional brazing methods. Its ability to produce clean, strong, and precise joints makes it a preferred choice in many high-tech industries. The use of a vacuum brazing furnace ensures that the process is carried out under optimal conditions, resulting in high-quality products with minimal defects.
Summary Table:
Aspect | Details |
---|---|
Process | Joins metals in a vacuum environment, preventing oxidation and contamination. |
Advantages | - Multiple seam welding |
- Minimal deformation
- Uniform heating
- No oxidation or contamination
- Supports complex designs | | Key Components | - Vacuum system (valves, pumps)
- Heating system (temperature control) | | Applications | Aerospace, medical devices, semiconductor manufacturing | | Benefits | Clean process, time and cost savings, superior product performance |
Ready to enhance your metal joining process? Contact us today to learn more about vacuum brazing solutions!