Yes, you can melt aluminum in an induction furnace. Induction furnaces are highly efficient and effective for melting metals like aluminum due to their ability to generate precise and controlled heat through electromagnetic induction. The process involves using a coil to create a magnetic field that induces eddy currents in the aluminum, heating it from within. This method ensures uniform melting, efficient energy use, and the ability to remove impurities effectively. Induction furnaces are particularly suitable for melting aluminum because they can handle the metal's relatively low melting point (660°C or 1220°F) and provide the necessary stirring action for alloy production.
Key Points Explained:
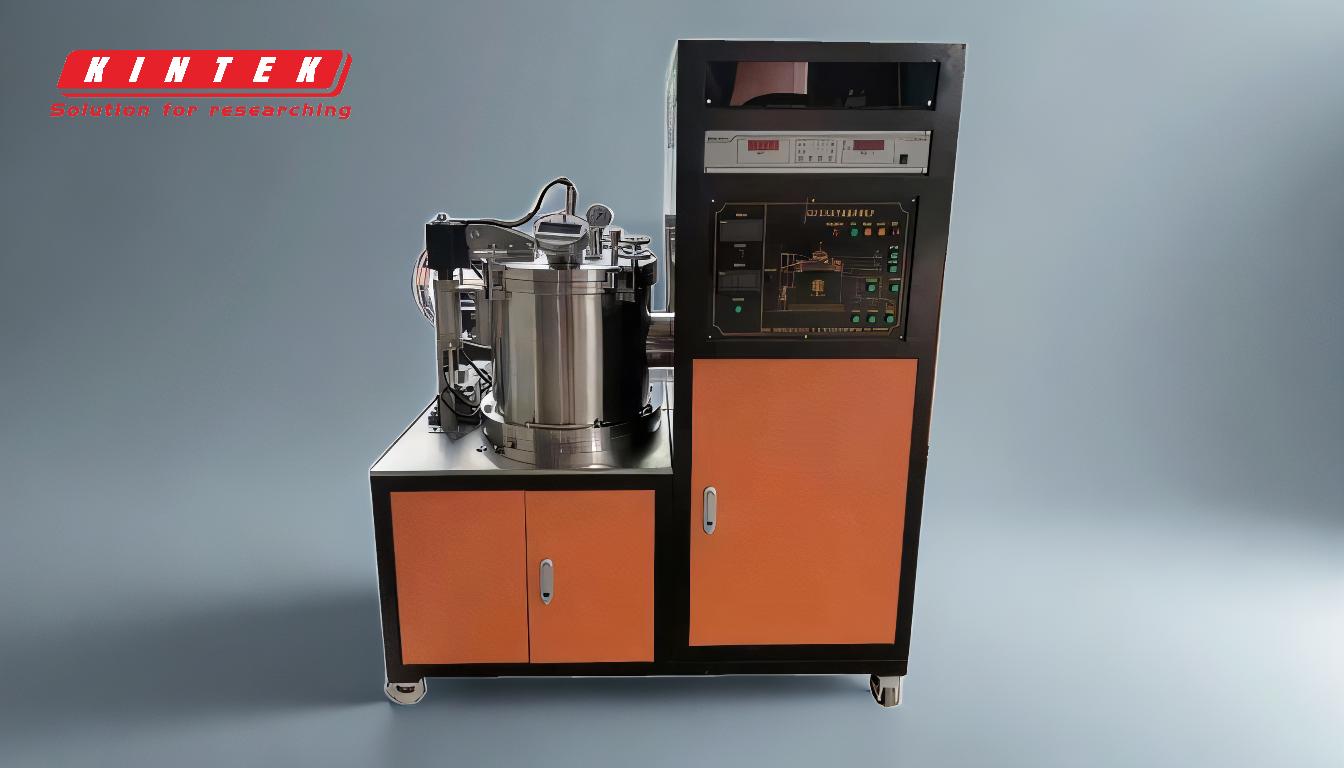
-
How Induction Furnaces Work
- Induction furnaces use a coil made of conductive material (e.g., copper) to generate a magnetic field when an alternating current passes through it.
- This magnetic field induces eddy currents in the metal (in this case, aluminum), which generate heat through Joule heating.
- The heat is produced directly within the metal, ensuring efficient and uniform melting.
-
Suitability for Aluminum Melting
- Aluminum has a relatively low melting point (660°C or 1220°F), which is well within the temperature range that induction furnaces can achieve.
- The stirring action caused by the eddy currents ensures proper mixing of the molten aluminum, which is crucial for producing uniform alloys.
- Impurities in the aluminum rise to the surface due to their lower density, allowing them to be easily removed using a tilting mechanism.
-
Energy Efficiency and Clean Process
- Induction furnaces are energy-efficient, making them ideal for melting aluminum, a process that typically consumes significant energy.
- The heat is generated directly within the metal, reducing heat loss and improving overall efficiency.
- The process is clean, as there is no direct contact between the heat source and the metal, minimizing contamination.
-
Applications in Aluminum Alloy Production
- Induction furnaces are commonly used in foundries and metal casting operations to produce aluminum alloys.
- The continuous stirring action ensures proper mixing of alloying elements, resulting in alloys of exact composition.
- The ability to control the frequency of the alternating current allows for precise control over the melting process.
-
Advantages Over Other Melting Methods
- Induction furnaces offer faster melting times compared to traditional methods like gas or resistance furnaces.
- They provide better temperature control, reducing the risk of overheating or underheating the aluminum.
- The stirring action ensures uniform temperature distribution, which is critical for producing high-quality aluminum products.
-
Considerations for Using Induction Furnaces
- The frequency of the alternating current affects the depth of heat penetration. Higher frequencies are suitable for smaller batches, while lower frequencies are better for larger volumes.
- Proper crucible selection is essential to withstand the high temperatures and chemical reactivity of molten aluminum.
- Regular maintenance of the coil and other components is necessary to ensure consistent performance and longevity of the furnace.
In summary, induction furnaces are an excellent choice for melting aluminum due to their efficiency, precision, and ability to produce high-quality alloys. Their clean and controlled process makes them a preferred option in industries requiring reliable and consistent aluminum melting.
Summary Table:
Key Aspect | Details |
---|---|
How It Works | Uses electromagnetic induction to generate heat directly within the metal. |
Suitability for Aluminum | Handles aluminum's low melting point (660°C/1220°F) and ensures uniformity. |
Energy Efficiency | Direct heating reduces energy loss, making it highly efficient. |
Applications | Ideal for aluminum alloy production in foundries and metal casting. |
Advantages | Faster melting, precise temperature control, and uniform heat distribution. |
Considerations | Requires proper crucible selection and regular maintenance for longevity. |
Ready to enhance your aluminum melting process? Contact us today to learn more about induction furnaces!