Yes, aluminum can be melted using an induction coil, as induction melting furnaces are specifically designed for this purpose. These furnaces utilize alternating current to generate a magnetic field, which induces eddy currents in the aluminum, causing it to heat up and eventually melt. The process is efficient and allows for the separation of impurities, which rise to the surface due to their lower density, leaving behind pure aluminum. Induction melting is widely used in industries for its precision, energy efficiency, and ability to produce high-quality metal.
Key Points Explained:
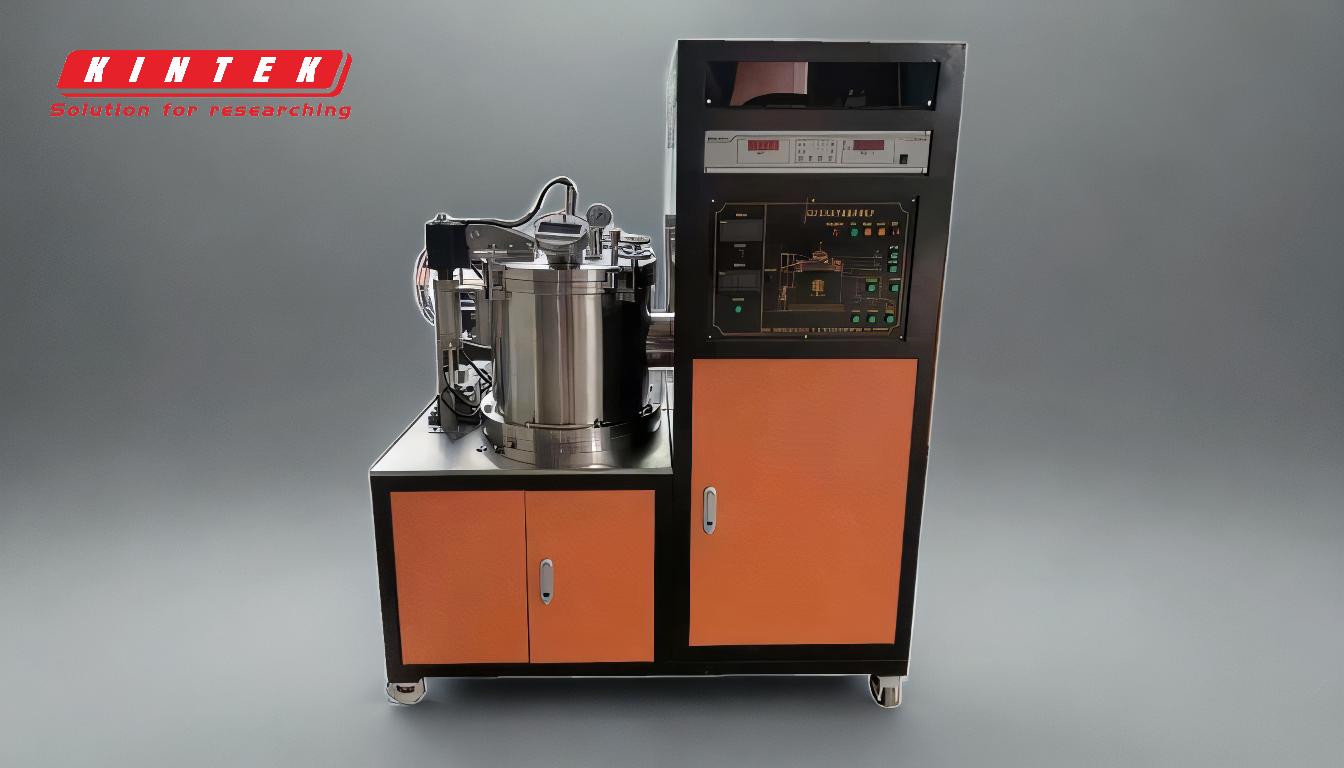
-
How Induction Melting Works:
- Induction melting relies on the principle of electromagnetic induction. An alternating current passes through the induction coil, creating a fluctuating magnetic field.
- When aluminum (or any conductive material) is placed within this field, eddy currents are induced within the metal. These currents generate heat due to the metal's electrical resistance, causing the aluminum to melt.
-
Advantages of Induction Melting for Aluminum:
- Efficiency: Induction melting is highly energy-efficient because it directly heats the metal without significant heat loss to the surrounding environment.
- Precision: The process allows for precise temperature control, which is crucial for achieving consistent melting results and maintaining the desired properties of the aluminum.
- Purity: As the aluminum melts, impurities (such as oxides and other non-metallic inclusions) rise to the surface due to their lower density. These impurities can be easily removed, leaving behind high-purity aluminum.
-
Equipment Requirements:
- Induction Coil: The coil is the core component of the induction furnace. It must be designed to handle the specific frequency and power requirements for melting aluminum.
- Power Supply: An alternating current power supply is needed to generate the magnetic field. The frequency of the current can vary depending on the size of the furnace and the volume of aluminum being melted.
- Crucible: A crucible made of refractory material is used to hold the aluminum during the melting process. It must withstand high temperatures and the chemical properties of molten aluminum.
-
Process of Melting Aluminum with an Induction Coil:
- Loading: Aluminum is loaded into the crucible, which is placed inside the induction coil.
- Heating: The induction coil is energized, creating a magnetic field that induces eddy currents in the aluminum. The metal heats up and begins to melt.
- Separation of Impurities: As the aluminum melts, impurities float to the surface. These can be skimmed off or removed using a tilting mechanism.
- Casting: Once the aluminum is fully melted and purified, it can be poured into molds or used for further processing.
-
Applications of Induction-Melted Aluminum:
- Manufacturing: Induction-melted aluminum is used in the production of automotive parts, aerospace components, and other high-performance applications where material purity and consistency are critical.
- Recycling: Induction melting is also used in aluminum recycling, as it efficiently separates impurities from scrap aluminum, allowing it to be reused in new products.
-
Considerations for Purchasing Equipment:
- Capacity: Ensure the induction furnace has the capacity to handle the volume of aluminum you intend to melt.
- Frequency: The frequency of the induction coil should match the size of the aluminum pieces being melted. Lower frequencies are suitable for larger volumes, while higher frequencies are better for smaller, more precise applications.
- Energy Efficiency: Look for furnaces with high energy efficiency ratings to reduce operating costs.
- Safety Features: Ensure the equipment includes safety mechanisms, such as temperature controls and emergency shut-off systems, to prevent accidents.
In summary, melting aluminum with an induction coil is a proven and efficient method, widely used in industries for its ability to produce high-quality, pure aluminum. The process involves precise control of electromagnetic fields to generate heat, making it suitable for both manufacturing and recycling applications. When purchasing equipment, consider factors like capacity, frequency, energy efficiency, and safety to ensure optimal performance.
Summary Table:
Key Aspect | Details |
---|---|
How It Works | Electromagnetic induction heats aluminum via eddy currents, causing melting. |
Advantages | High efficiency, precise temperature control, and impurity removal. |
Equipment Needed | Induction coil, power supply, and refractory crucible. |
Applications | Manufacturing (automotive, aerospace) and aluminum recycling. |
Purchase Considerations | Capacity, frequency, energy efficiency, and safety features. |
Ready to enhance your aluminum melting process? Contact us today to find the perfect induction furnace for your needs!