A hydraulic press can indeed be used for forging, although it is not the most common method. Forging typically involves shaping metal using compressive forces, and a hydraulic press can generate the necessary pressure to deform the metal. However, the suitability of a hydraulic press for forging depends on the specific requirements of the forging process, such as the type of metal, the desired shape, and the required precision. Hydraulic presses are particularly useful for tasks that require consistent pressure and control, making them suitable for certain types of forging operations.
Key Points Explained:
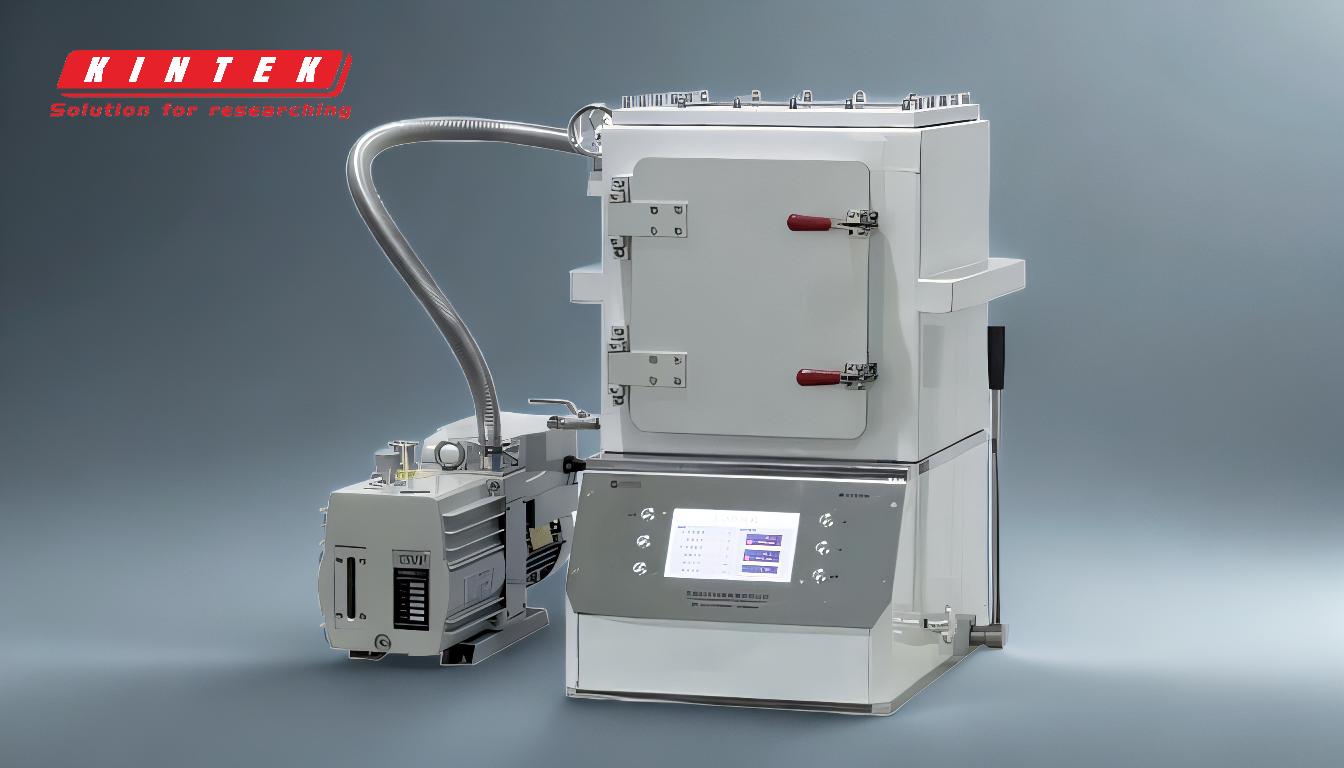
-
Understanding Hydraulic Presses:
- A hydraulic press uses hydraulic cylinders to generate a compressive force. This force can be precisely controlled, making it suitable for applications that require consistent pressure.
- Hydraulic presses are commonly used in laboratories for sample preparation, such as creating pellets for spectroscopic analysis. This demonstrates their ability to handle materials under high pressure, which is also relevant for forging.
-
Applications of Hydraulic Presses in Forging:
- Forging involves shaping metal using compressive forces. A hydraulic press can be used to forge metals by applying the necessary pressure to deform the metal into the desired shape.
- The hydraulic hot press machine is particularly useful for forging operations that require precise control over the pressure and temperature. This is important for ensuring the quality and consistency of the forged product.
-
Advantages of Using Hydraulic Presses for Forging:
- Precision and Control: Hydraulic presses offer precise control over the pressure applied, which is crucial for achieving the desired shape and properties in the forged metal.
- Consistency: The ability to maintain consistent pressure throughout the forging process ensures uniformity in the final product.
- Versatility: Hydraulic presses can be used for a wide range of forging operations, from simple shapes to complex geometries.
-
Limitations of Hydraulic Presses in Forging:
- Speed: Hydraulic presses are generally slower than other forging methods, such as mechanical presses or hammers. This can be a limitation for high-volume production.
- Cost: Hydraulic presses can be more expensive to purchase and maintain compared to other types of forging equipment.
- Energy Consumption: Hydraulic presses may consume more energy, especially when operating at high pressures for extended periods.
-
Comparison with Other Forging Methods:
- Mechanical Presses: These are faster and more suitable for high-volume production but may lack the precision and control offered by hydraulic presses.
- Hammers: Forging hammers are capable of delivering rapid, high-impact blows, which are ideal for certain types of forging but may not offer the same level of control as hydraulic presses.
-
Practical Considerations:
- Material Type: The type of metal being forged will influence the choice of press. Hydraulic presses are well-suited for materials that require precise control over the forging process.
- Shape Complexity: For complex shapes, a hydraulic press may be more appropriate due to its ability to apply consistent pressure and control the deformation process.
- Production Volume: For low to medium production volumes, a hydraulic press may be a good choice. However, for high-volume production, other methods may be more efficient.
In conclusion, while a hydraulic press can be used for forging, its suitability depends on the specific requirements of the forging process. The precision, control, and consistency offered by hydraulic presses make them a viable option for certain types of forging operations, particularly those involving complex shapes or materials that require careful handling. However, considerations such as speed, cost, and energy consumption should also be taken into account when deciding whether to use a hydraulic press for forging.
Summary Table:
Aspect | Details |
---|---|
Precision and Control | Hydraulic presses provide precise control over pressure for accurate forging. |
Consistency | Ensures uniform pressure application for consistent results. |
Versatility | Suitable for a wide range of forging operations, from simple to complex shapes. |
Limitations | Slower speed, higher cost, and greater energy consumption compared to other methods. |
Best For | Low to medium production volumes, complex shapes, and materials requiring precision. |
Discover how a hydraulic press can enhance your forging process—contact us today for expert advice!