Induction heating does work on titanium, as titanium is a conductive material. Induction heating relies on the principle of electromagnetic induction, where eddy currents are induced in conductive materials, generating heat. Titanium, being a metal with relatively low electrical resistivity, can be effectively heated using induction heating. This method is particularly useful for applications such as heat treatment, melting, and surface hardening of titanium and its alloys. However, the efficiency of induction heating on titanium depends on factors like the frequency of the alternating magnetic field, the geometry of the workpiece, and the specific application requirements.
Key Points Explained:
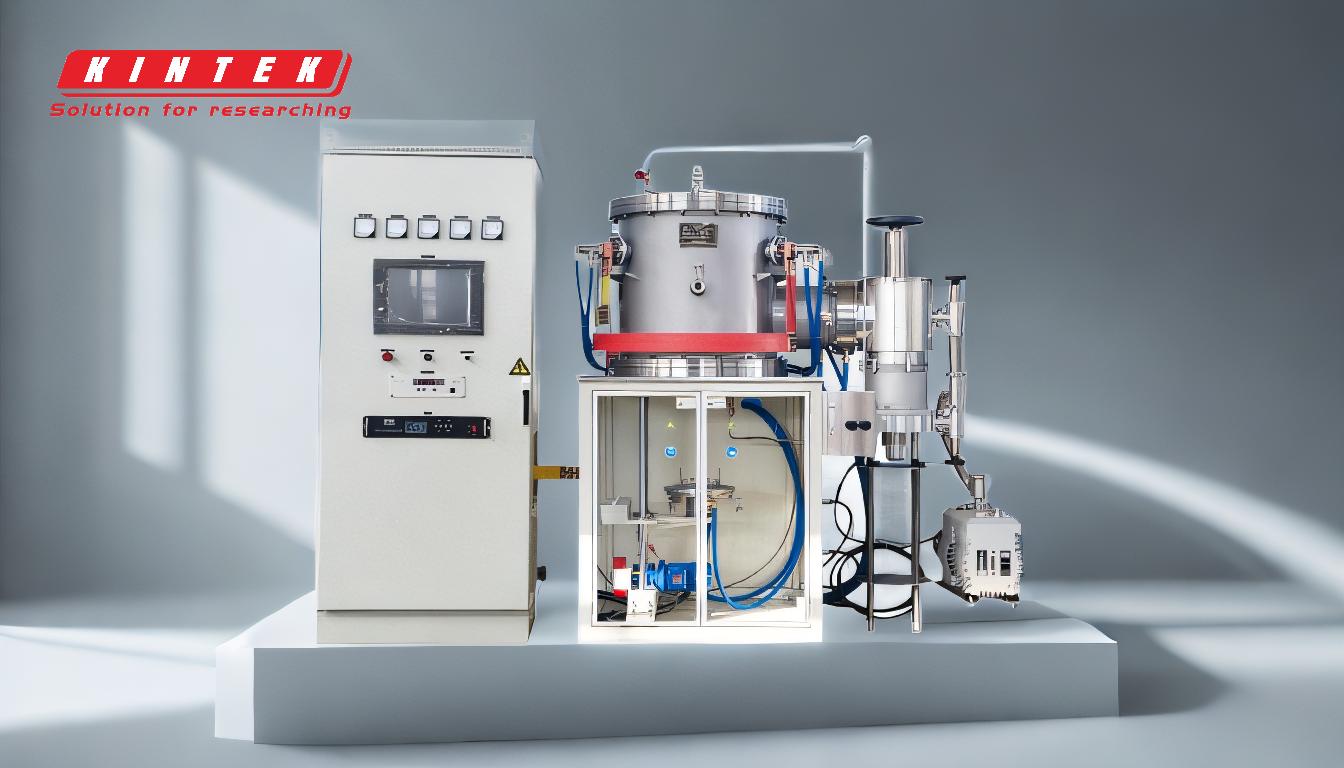
-
Principle of Induction Heating:
- Induction heating works by generating eddy currents in conductive materials when exposed to an alternating magnetic field. These currents produce heat due to the material's electrical resistance.
- Titanium, being a conductive metal, can be heated using this method. Its electrical resistivity, though higher than metals like copper or aluminum, is still within the range suitable for induction heating.
-
Applications of Induction Heating on Titanium:
- Heat Treatment: Induction heating is used to heat titanium to specific temperatures for processes like annealing, hardening, or stress relief. This is particularly useful in aerospace and medical industries where titanium alloys are prevalent.
- Melting: Induction furnaces can melt titanium and its alloys, enabling the production of specialized materials with precise compositions.
- Surface Hardening: Induction heating can selectively harden the surface of titanium components while leaving the core unaffected, improving wear resistance and durability.
-
Factors Affecting Induction Heating Efficiency on Titanium:
- Frequency of the Alternating Magnetic Field: Higher frequencies are generally more effective for heating smaller or thinner titanium parts, while lower frequencies are better suited for larger components.
- Geometry of the Workpiece: Complex shapes or thin sections may require careful design of the induction coil to ensure uniform heating.
- Electrical Resistivity: Titanium's resistivity is higher than some other metals, which means it may require more power or longer heating times compared to materials like copper or aluminum.
-
Advantages of Induction Heating for Titanium:
- Precision and Control: Induction heating allows for localized and controlled heating, reducing the risk of overheating or damaging the material.
- Speed: The process is faster than traditional heating methods, making it suitable for high-volume manufacturing.
- Energy Efficiency: Induction heating is more energy-efficient than conventional methods, as it directly heats the material without significant heat loss to the surroundings.
-
Challenges and Considerations:
- Oxidation: Titanium is highly reactive at elevated temperatures, so induction heating must often be performed in a controlled atmosphere or vacuum to prevent oxidation.
- Material Properties: The specific alloy composition of titanium can affect its response to induction heating, requiring tailored process parameters.
-
Future Prospects:
- As technology advances, induction heating is expected to play a larger role in the processing of titanium and other advanced materials. Research is ongoing to optimize parameters for emerging applications, such as additive manufacturing and medical device fabrication.
In summary, induction heating is a viable and effective method for processing titanium, offering precision, speed, and energy efficiency. However, careful consideration of factors like frequency, geometry, and environmental conditions is necessary to achieve optimal results.
Summary Table:
Aspect | Details |
---|---|
Principle | Generates heat via eddy currents in titanium when exposed to magnetic fields. |
Applications | Heat treatment, melting, and surface hardening of titanium alloys. |
Key Factors | Frequency, geometry, and electrical resistivity affect heating efficiency. |
Advantages | Precision, speed, and energy efficiency for high-performance applications. |
Challenges | Requires controlled atmosphere to prevent oxidation; alloy-specific parameters. |
Ready to optimize your titanium processing with induction heating? Contact our experts today for tailored solutions!