PVD (Physical Vapor Deposition) coatings are highly effective in preventing rust due to their excellent corrosion resistance properties. These coatings are widely used in industries such as aerospace, automotive, and medical devices because they provide a durable, thin layer that protects the underlying material from environmental factors like moisture and oxidation. PVD coatings, such as Zirconium Nitride (ZrN), have demonstrated exceptional resistance to corrosion, surpassing 1200 hours in neutral salt spray tests (ASTM B117) and over 150 hours in CASS tests. The thinness of PVD coatings, ranging from 0.5 to 5 microns, does not compromise their effectiveness, as they are highly adherent and difficult to remove. Additionally, PVD coatings can replicate the original finish of materials, making them both functional and aesthetically pleasing. Overall, PVD coatings are a reliable solution for rust prevention, extending the lifespan of products significantly.
Key Points Explained:
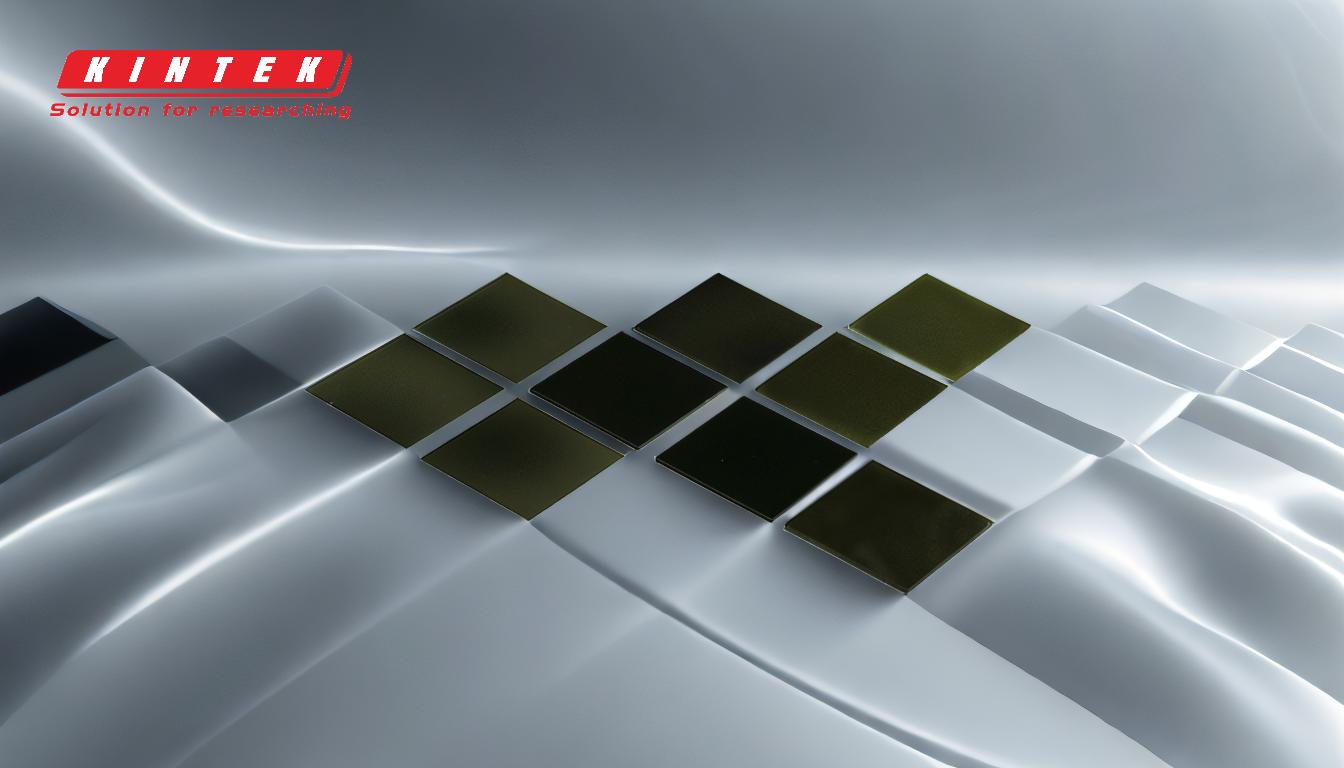
-
Corrosion Resistance of PVD Coatings
- PVD coatings are specifically designed to resist corrosion and oxidation, making them highly effective in preventing rust.
- They form a protective barrier that shields the underlying material from environmental factors like moisture, salt, and chemicals.
- For example, Zirconium Nitride (ZrN) coatings have been tested to withstand over 1200 hours in neutral salt spray tests (ASTM B117), which is a standard measure of corrosion resistance.
-
Thin Yet Durable Layer
- PVD coatings are extremely thin, ranging from 0.5 to 5 microns, but their thinness does not compromise their protective capabilities.
- The coatings are highly adherent, meaning they bond strongly to the substrate, making them difficult to remove and ensuring long-lasting protection.
- Despite their thinness, PVD coatings can replicate the original finish of materials, maintaining both functionality and aesthetics.
-
Applications in Rust-Prone Environments
- PVD coatings are used in industries where rust prevention is critical, such as automotive (e.g., wheels, pistons), aerospace, and medical devices.
- They are also applied to tools and equipment exposed to harsh conditions, such as cutting tools, dies, and molds, where corrosion resistance is essential for longevity.
- The ability of PVD coatings to withstand extreme conditions, such as salt spray and acidic environments, makes them ideal for use in marine, industrial, and outdoor applications.
-
Superior Performance Compared to Traditional Methods
- PVD coatings are a greener alternative to traditional methods like chrome plating, as they do not produce toxic substances during application.
- They offer better corrosion resistance and durability compared to electroplating, as evidenced by their performance in standardized tests like CASS (Copper-Accelerated Acetic Acid-Salt Spray).
- The enhanced lifespan of products coated with PVD (up to 25 years in some cases) highlights their effectiveness in preventing rust and other forms of degradation.
-
Versatility in Material Compatibility
- PVD coatings can be applied to a wide range of substrates, including metals, polymers, and ceramics, making them versatile for various applications.
- The properties of the coating can be tailored to the specific needs of the substrate, ensuring optimal protection against rust and other forms of corrosion.
- For instance, coatings like Titanium Nitride (TiN) not only provide corrosion resistance but also enhance the hardness and wear resistance of the material.
-
Long-Term Cost Efficiency
- By preventing rust and extending the lifespan of products, PVD coatings reduce the need for frequent replacements and maintenance, leading to long-term cost savings.
- Their durability and resistance to wear make them a cost-effective solution for industries that require high-performance materials.
- The ability to replicate the original finish of materials also reduces the need for additional finishing processes, further lowering costs.
In conclusion, PVD coatings are an excellent choice for preventing rust due to their superior corrosion resistance, durability, and versatility. Their thin yet highly adherent nature ensures long-lasting protection, while their compatibility with various substrates and applications makes them a practical solution for industries requiring rust prevention.
Summary Table:
Feature | Details |
---|---|
Corrosion Resistance | Withstands 1200+ hours in neutral salt spray tests (ASTM B117). |
Thickness | 0.5 to 5 microns, highly adherent and durable. |
Applications | Automotive, aerospace, medical devices, marine, and industrial equipment. |
Material Compatibility | Metals, polymers, ceramics—tailored for optimal protection. |
Cost Efficiency | Reduces maintenance and replacement costs, extends product lifespan. |
Protect your products from rust with PVD coatings—contact us today to learn more!