Sintering is a critical process in materials science that involves heating powdered materials to a temperature below their melting point to form a solid mass. This process significantly impacts the microstructure of materials, including grain size, pore size, and grain boundary distribution. While sintering generally leads to densification and improved mechanical properties, its effect on grain size is complex and depends on various factors such as temperature, time, and the initial powder characteristics. In many cases, sintering can lead to grain growth rather than a decrease in grain size, especially at higher temperatures or longer sintering times. However, controlled sintering conditions can be optimized to minimize grain growth and achieve desired material properties.
Key Points Explained:
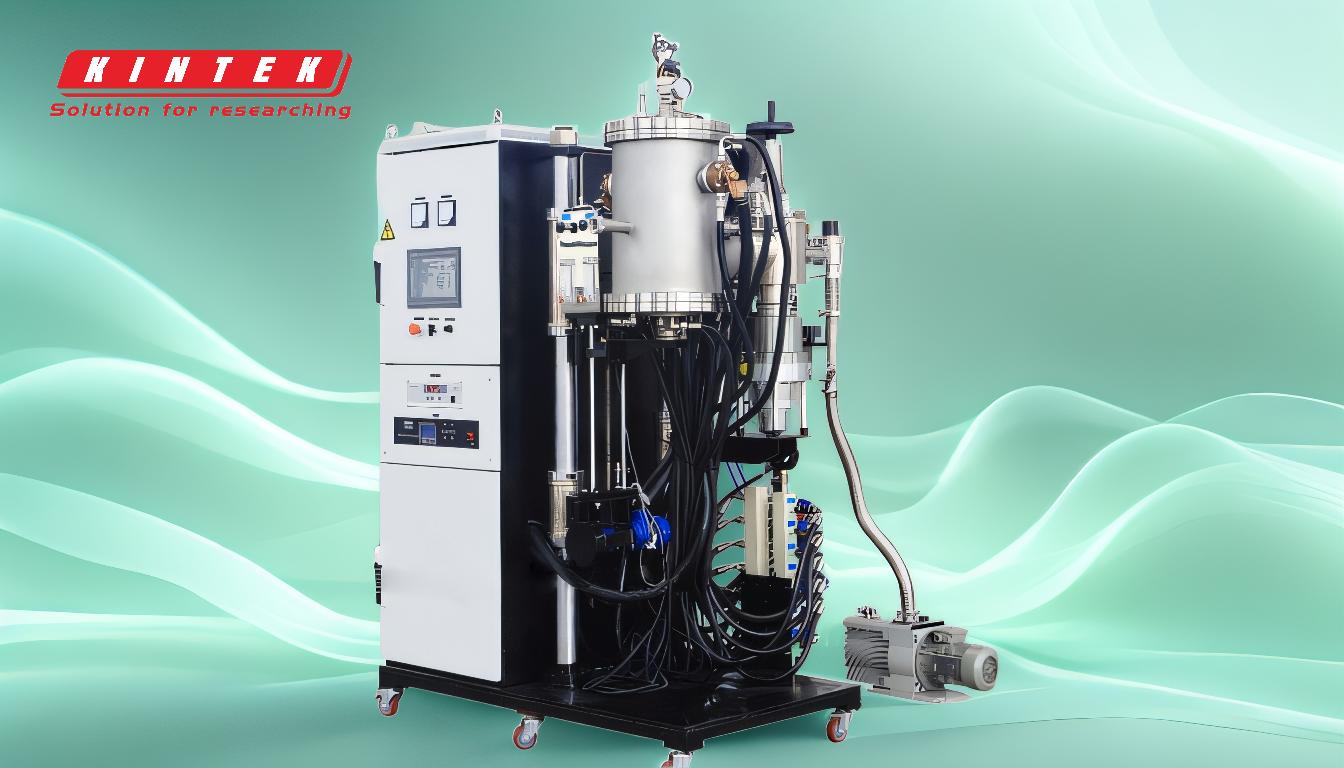
-
Sintering and Microstructure Changes:
- Sintering directly influences the microstructure of materials, including grain size, pore size, and grain boundary distribution.
- The process involves the bonding of particles through diffusion mechanisms, leading to densification and the formation of a cohesive structure.
-
Effect on Grain Size:
- Sintering can lead to grain growth rather than a decrease in grain size, especially at higher temperatures or longer sintering durations.
- Grain growth occurs as smaller grains merge to form larger ones, driven by the reduction of surface energy and the diffusion of atoms across grain boundaries.
-
Factors Influencing Grain Size During Sintering:
- Temperature: Higher sintering temperatures generally promote grain growth.
- Time: Longer sintering times can also lead to increased grain size.
- Initial Powder Characteristics: The size and distribution of the initial powder particles can influence the final grain size after sintering.
-
Controlling Grain Size:
- To minimize grain growth, sintering conditions such as temperature and time must be carefully controlled.
- Techniques such as two-step sintering or the use of grain growth inhibitors can be employed to achieve finer grain sizes.
-
Impact on Material Properties:
- Grain size significantly affects the mechanical properties of materials, including strength, hardness, and wear resistance.
- Smaller grain sizes generally lead to higher strength and hardness due to the increased number of grain boundaries, which impede dislocation movement.
-
Applications and Considerations:
- Sintering is used in various applications, including the production of ceramics, metals, and composites, where controlled grain size is crucial for achieving desired properties.
- For applications requiring high strength and durability, optimizing sintering conditions to control grain size is essential.
In summary, while sintering can lead to grain growth, careful control of sintering parameters can help achieve the desired grain size and, consequently, the desired material properties. Understanding the relationship between sintering conditions and grain size is crucial for optimizing the performance of sintered materials in various applications.
Summary Table:
Aspect | Details |
---|---|
Sintering Effect | Influences grain size, pore size, and grain boundary distribution. |
Grain Size Impact | Can lead to grain growth, especially at higher temperatures or longer times. |
Key Factors | Temperature, time, and initial powder characteristics. |
Control Techniques | Two-step sintering, grain growth inhibitors, and optimized conditions. |
Material Properties | Smaller grains enhance strength, hardness, and wear resistance. |
Applications | Used in ceramics, metals, and composites for high-strength materials. |
Optimize your sintering process for superior material properties—contact our experts today!