Sintering is a critical process in ceramic manufacturing that transforms powdered materials into solid, dense objects by applying heat and sometimes pressure. The process involves several key steps: preparing the ceramic powder, compacting it into a desired shape (green body), and heating it to a high temperature below its melting point to fuse the particles. This reduces porosity, enhances strength, and results in a consolidated, durable ceramic product. The sintering process is essential for creating high-performance ceramics used in industries ranging from electronics to aerospace.
Key Points Explained:
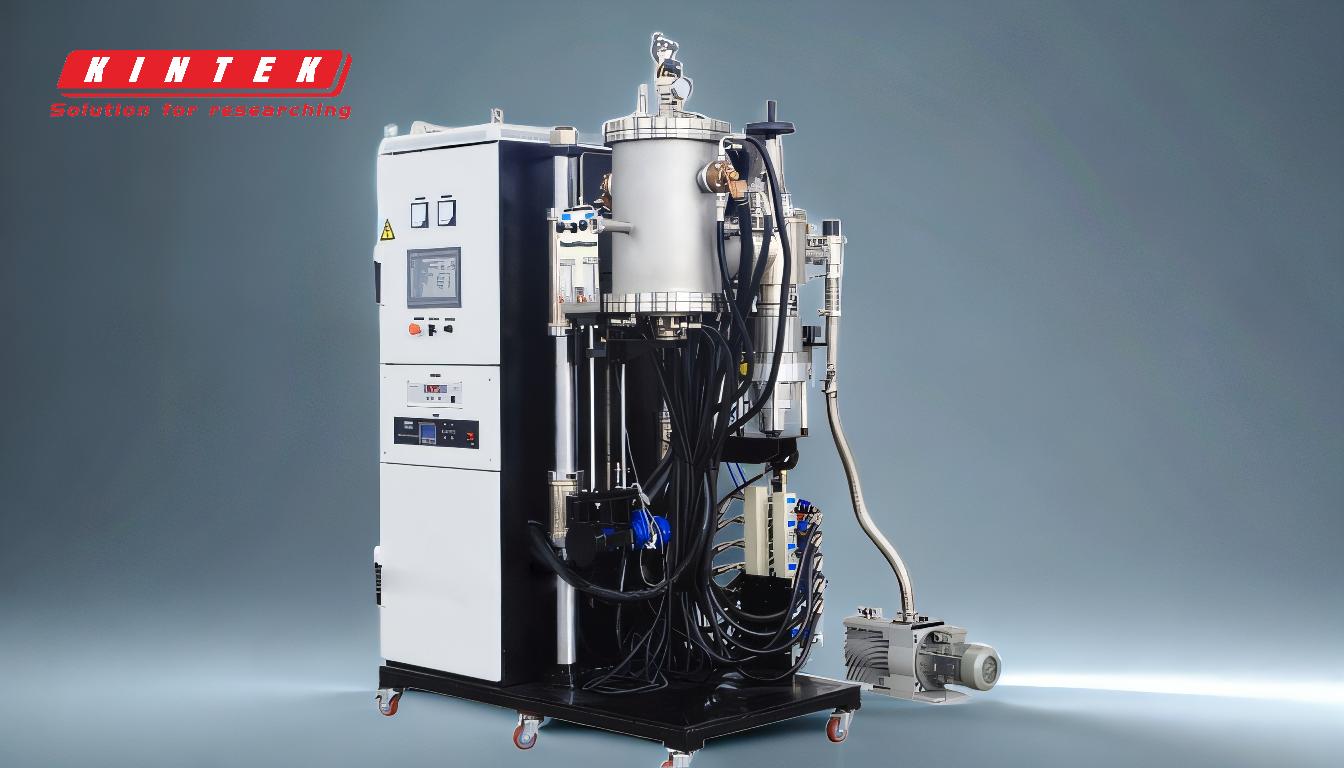
-
Preparation of Ceramic Powder:
- The process begins with the preparation of ceramic powder, which involves mixing raw materials like clay, oxides, or other ceramic compounds with additives such as binders and deflocculants. These additives help in shaping and stabilizing the powder.
- The mixture is often spray-dried to form a free-flowing granular powder, which is easier to handle and press into molds.
-
Forming the Green Body:
- The prepared powder is compacted into a specific shape using techniques like pressing, extrusion, or slip casting. This forms the "green body," which is a fragile, porous structure that holds the desired shape.
- The green body is carefully handled to avoid cracks or deformations before sintering.
-
Binder Burn-Off (Debinding):
- Before sintering, the green body is heated at a low temperature to remove organic binders and other volatile components. This step is crucial to prevent defects during the high-temperature sintering process.
-
Sintering Process:
- The green body is heated in a controlled environment (often in a kiln) to a temperature just below the melting point of the ceramic material. This allows the particles to diffuse and bond at their boundaries without liquefying.
- During sintering, the material undergoes densification, where pores shrink and the particles merge, resulting in a solid, low-porosity structure.
- Additional forces like pressure (hot pressing) or electrical currents (spark plasma sintering) may be applied to enhance the densification process.
-
Cooling and Solidification:
- After sintering, the ceramic is slowly cooled to room temperature to prevent thermal stress and cracking. This solidifies the material into a unified, dense mass with improved mechanical properties.
-
Post-Sintering Processes:
- Sintered ceramics may undergo additional machining, such as grinding or polishing with diamond tools, to achieve precise dimensions and surface finishes.
- In some cases, ceramics are metallized or brazed to join them with other materials for specific applications.
-
Applications and Benefits:
- Sintered ceramics are used in a wide range of applications, including electronics, medical devices, aerospace components, and industrial tools, due to their high strength, wear resistance, and thermal stability.
- The sintering process is particularly advantageous for materials with extremely high melting points, such as tungsten and molybdenum, which are difficult to process using traditional melting techniques.
By following these steps, the sintering process effectively transforms ceramic powders into high-performance components with tailored properties for specific applications.
Summary Table:
Step | Description |
---|---|
1. Preparation | Mix raw materials with additives, then spray-dry to form free-flowing powder. |
2. Green Body | Compact powder into shape using techniques like pressing or extrusion. |
3. Debinding | Heat to remove binders and prevent defects during sintering. |
4. Sintering | Heat to near-melting point to bond particles and reduce porosity. |
5. Cooling | Slowly cool to solidify the material and prevent cracking. |
6. Post-Processing | Machine, polish, or metallize for precise dimensions and applications. |
7. Applications | Used in electronics, aerospace, medical devices, and industrial tools. |
Discover how sintering can enhance your ceramic manufacturing process—contact our experts today!