Plasma-Enhanced Chemical Vapor Deposition (PECVD) and Chemical Vapor Deposition (CVD) are both widely used techniques for depositing thin films onto substrates, but they differ significantly in their mechanisms, operational conditions, and applications. PECVD utilizes plasma to enhance the deposition process, enabling faster growth rates, better edge coverage, and more uniform films at lower temperatures compared to conventional CVD. This makes PECVD particularly suitable for high-quality applications where precision and reproducibility are critical. In contrast, CVD relies solely on thermal energy to drive chemical reactions, often requiring higher temperatures and offering different deposition characteristics. Understanding these differences is essential for selecting the appropriate method based on specific application requirements.
Key Points Explained:
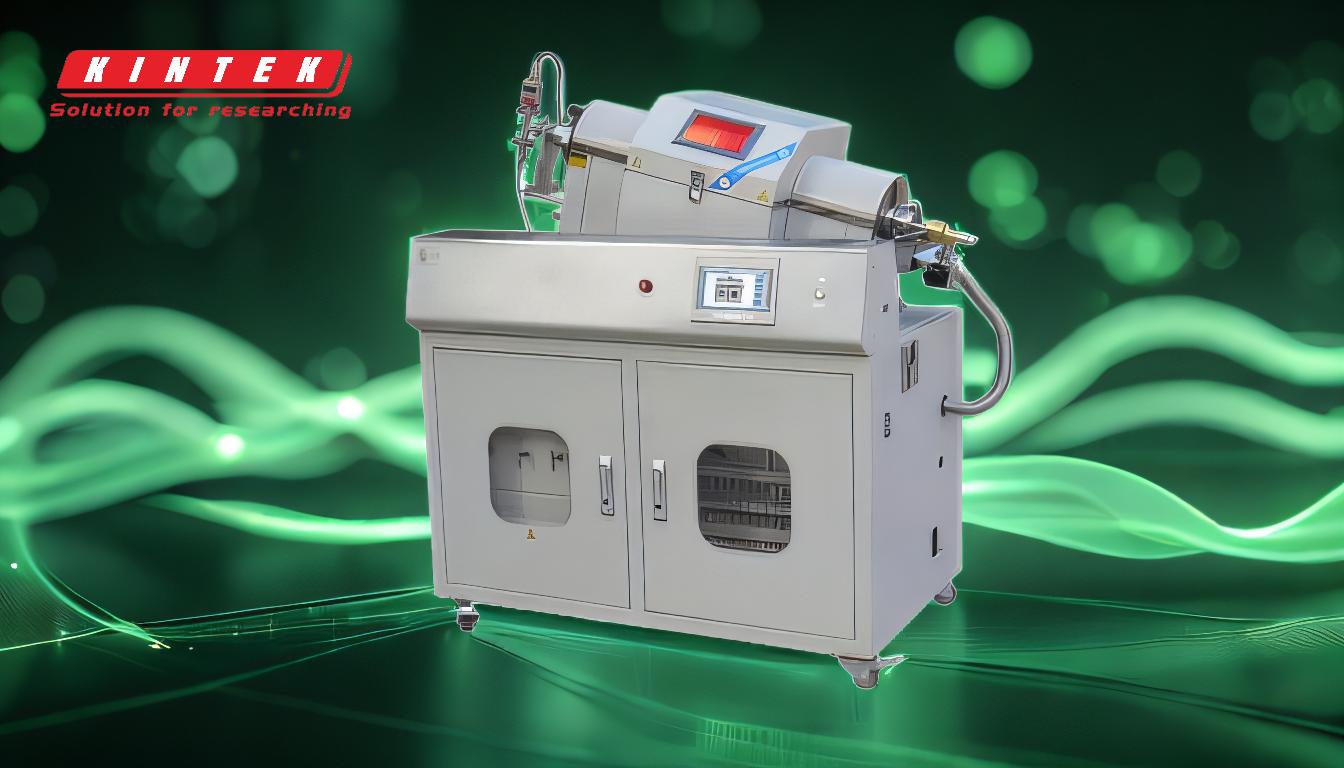
-
Mechanism of Deposition:
- PECVD: Utilizes plasma to provide the activation energy required for chemical reactions. The plasma contains high-energy electrons that enable the process to occur at lower temperatures, typically below 400°C.
- CVD: Relies on thermal energy to drive chemical reactions between gaseous precursors and the substrate. This process often requires higher temperatures, ranging from 450°C to 1050°C, depending on the material being deposited.
-
Temperature Requirements:
- PECVD: Operates at significantly lower temperatures compared to CVD. This is advantageous for temperature-sensitive substrates, such as polymers or certain semiconductors, where high temperatures could cause damage.
- CVD: Requires higher temperatures to achieve the necessary chemical reactions. This can limit its use with temperature-sensitive materials but is often necessary for depositing high-quality, dense films.
-
Deposition Rate and Uniformity:
- PECVD: Offers faster deposition rates and better film uniformity due to the enhanced reactivity provided by the plasma. This results in more consistent and high-quality films, particularly for complex geometries and edge coverage.
- CVD: Generally has slower deposition rates compared to PECVD, but it can produce very dense and high-quality films, especially for applications requiring high-temperature stability.
-
Edge Coverage and Conformality:
- PECVD: Provides excellent edge coverage and conformality, making it ideal for applications where uniform film deposition over complex topographies is required.
- CVD: While CVD can also provide good conformality, it may not match the edge coverage capabilities of PECVD, especially in intricate structures.
-
Applications:
- PECVD: Commonly used in the semiconductor industry for depositing dielectric films, such as silicon nitride and silicon dioxide, as well as in the production of solar cells and MEMS devices. Its low-temperature capability makes it suitable for temperature-sensitive applications.
- CVD: Widely used in the production of hard coatings, such as titanium nitride and diamond-like carbon, as well as in the fabrication of high-performance materials like graphene. It is also used in the semiconductor industry for depositing polycrystalline silicon and epitaxial layers.
-
Reproducibility and Control:
- PECVD: Offers better reproducibility and process control due to the use of plasma, which allows for precise tuning of deposition parameters. This makes it more suitable for high-quality, high-volume manufacturing.
- CVD: While CVD can also be highly reproducible, it may require more stringent control of temperature and gas flow rates to achieve consistent results.
-
Substrate Compatibility:
- PECVD: Can be used with a wider range of substrates, including those that are temperature-sensitive, due to its lower operating temperatures.
- CVD: Typically requires substrates that can withstand higher temperatures, limiting its use with certain materials.
In summary, PECVD and CVD are complementary techniques, each with its own advantages and limitations. The choice between the two depends on the specific requirements of the application, including the desired film properties, substrate compatibility, and process conditions. PECVD is particularly well-suited for applications requiring low-temperature deposition, high uniformity, and excellent edge coverage, while CVD is ideal for high-temperature processes and the deposition of dense, high-quality films.
Summary Table:
Aspect | PECVD | CVD |
---|---|---|
Mechanism | Uses plasma for activation energy, enabling lower-temperature deposition. | Relies on thermal energy, requiring higher temperatures for reactions. |
Temperature | Operates below 400°C, suitable for temperature-sensitive substrates. | Requires 450°C to 1050°C, limiting use with sensitive materials. |
Deposition Rate | Faster deposition rates with better uniformity. | Slower deposition rates but produces denser films. |
Edge Coverage | Excellent edge coverage and conformality for complex structures. | Good conformality but may not match PECVD in intricate structures. |
Applications | Ideal for semiconductors, solar cells, and MEMS devices. | Used for hard coatings, graphene, and high-performance materials. |
Reproducibility | Better reproducibility and process control due to plasma. | Requires stringent control of temperature and gas flow for consistency. |
Substrate Compatibility | Compatible with a wider range of temperature-sensitive substrates. | Limited to substrates that can withstand high temperatures. |
Need help choosing between PECVD and CVD for your application? Contact our experts today!