Choosing the right crucible requires a thorough understanding of your specific application, including the type of furnace, the materials being melted, and the operational processes involved. Key considerations include the crucible's compatibility with the furnace, its ability to withstand high temperatures and chemical interactions, and its suitability for the specific alloys or materials being processed. Additionally, factors such as temperature change rates, charging methods, and slag removal processes must be evaluated to ensure optimal performance and longevity. Scientific applications demand inert materials like platinum or zirconium to avoid contamination, while industrial applications may require crucibles with specific electrical properties for induction furnaces. Each operation is unique, making crucible selection a highly individualized process.
Key Points Explained:
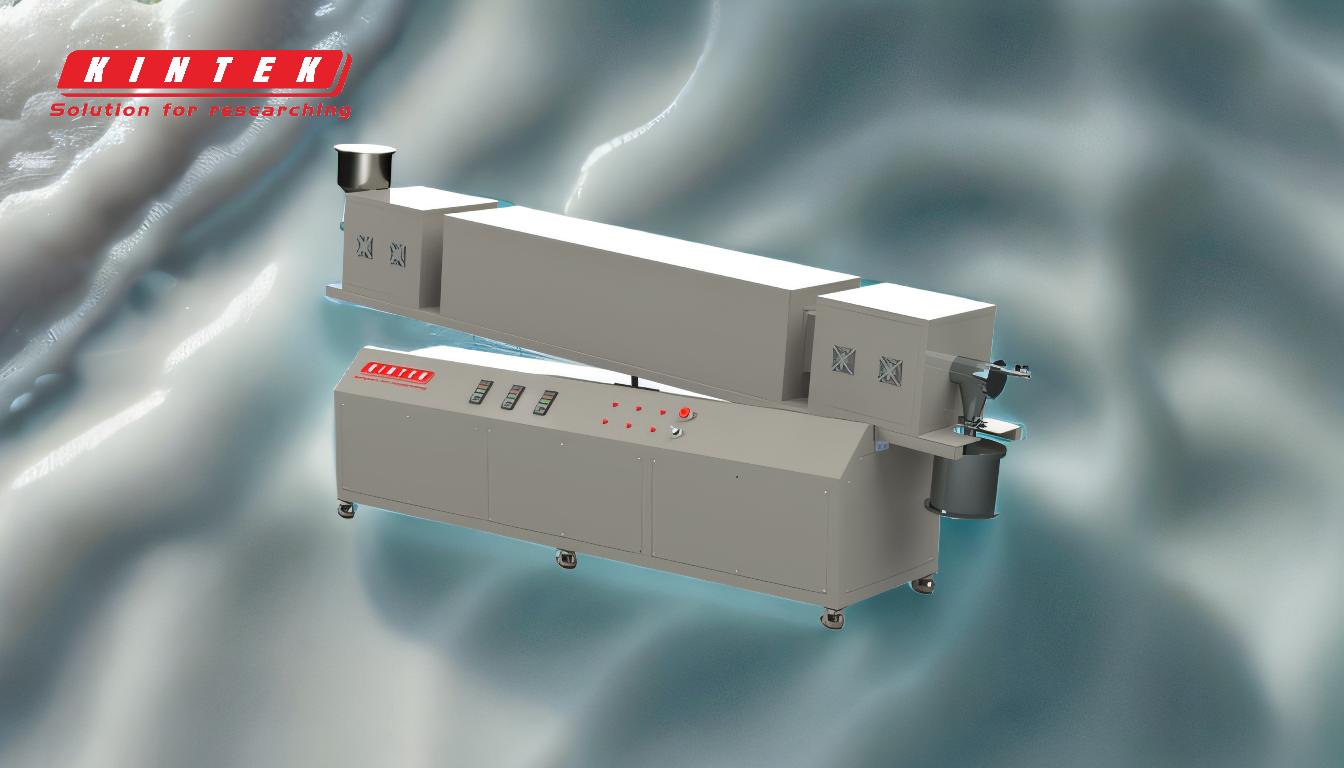
-
Furnace Compatibility:
- The crucible must match the type, capacity, and dimensions of the furnace. For example, induction furnaces require crucibles with specific electrical resistivity to prevent overheating. Lower frequency furnaces may need high silicon carbide content, while higher frequency furnaces may require high clay content.
-
Material Compatibility:
- The crucible must be compatible with the specific alloy or range of alloys being melted. This includes considering the melting and holding temperatures, as well as the chemical stability of the crucible material to avoid contamination or degradation.
-
Temperature Considerations:
- The crucible must withstand the melting and holding temperatures of the materials being processed. Rapid temperature changes can cause thermal shock, so the crucible material should have good thermal shock resistance.
-
Operational Processes:
- Consider how the crucible will be charged, the use of fluxes or additions, degassing or refining processes, and slag or dross removal methods. These factors can affect the crucible's performance and lifespan.
-
Specific Operational Requirements:
- Some operations may have unique requirements, such as avoiding alloy cross-contamination. In such cases, the crucible material must be inert and resistant to chemical reactions with the materials being processed.
-
Scientific Applications:
- In scientific applications, crucibles must be made of inert materials like platinum or zirconium to avoid contaminating the analyte. They must also withstand high temperatures and be chemically stable to ensure accurate results in analytical chemistry and sample preparation.
-
Electrical Properties for Induction Furnaces:
- For induction furnaces, the crucible's electrical resistivity must match the operating frequency of the furnace. This is crucial to prevent overheating and ensure efficient melting.
-
Individualized Selection:
- Each operation is unique, involving a specific combination of furnaces, alloys, working practices, metallurgical treatments, pouring arrangements, and end products. Therefore, the selection of a crucible must be tailored to the specific requirements of the operation to ensure maximum performance.
By carefully considering these factors, you can select a crucible that meets the specific needs of your application, ensuring optimal performance, longevity, and quality of the final product.
Summary Table:
Key Factor | Description |
---|---|
Furnace Compatibility | Match crucible type, capacity, and dimensions to the furnace. |
Material Compatibility | Ensure compatibility with specific alloys and chemical stability. |
Temperature Considerations | Withstand melting/holding temperatures and resist thermal shock. |
Operational Processes | Evaluate charging methods, slag removal, and degassing processes. |
Specific Requirements | Address unique needs like alloy cross-contamination prevention. |
Scientific Applications | Use inert materials like platinum or zirconium to avoid contamination. |
Induction Furnace Needs | Match electrical resistivity to furnace frequency for efficient melting. |
Individualized Selection | Tailor crucible choice to specific operation requirements for maximum performance. |
Need help selecting the perfect crucible for your application? Contact our experts today!