Choosing the right tube furnace involves understanding its structure, functionality, and the specific requirements of your application. Tube furnaces are versatile, efficient, and widely used in industries like metallurgy, glass, heat treatment, and new energy. Key considerations include the furnace's heating capabilities, work tube material, safety features, and compatibility with other systems. By evaluating these factors, you can select a tube furnace that meets your operational needs and ensures optimal performance.
Key Points Explained:
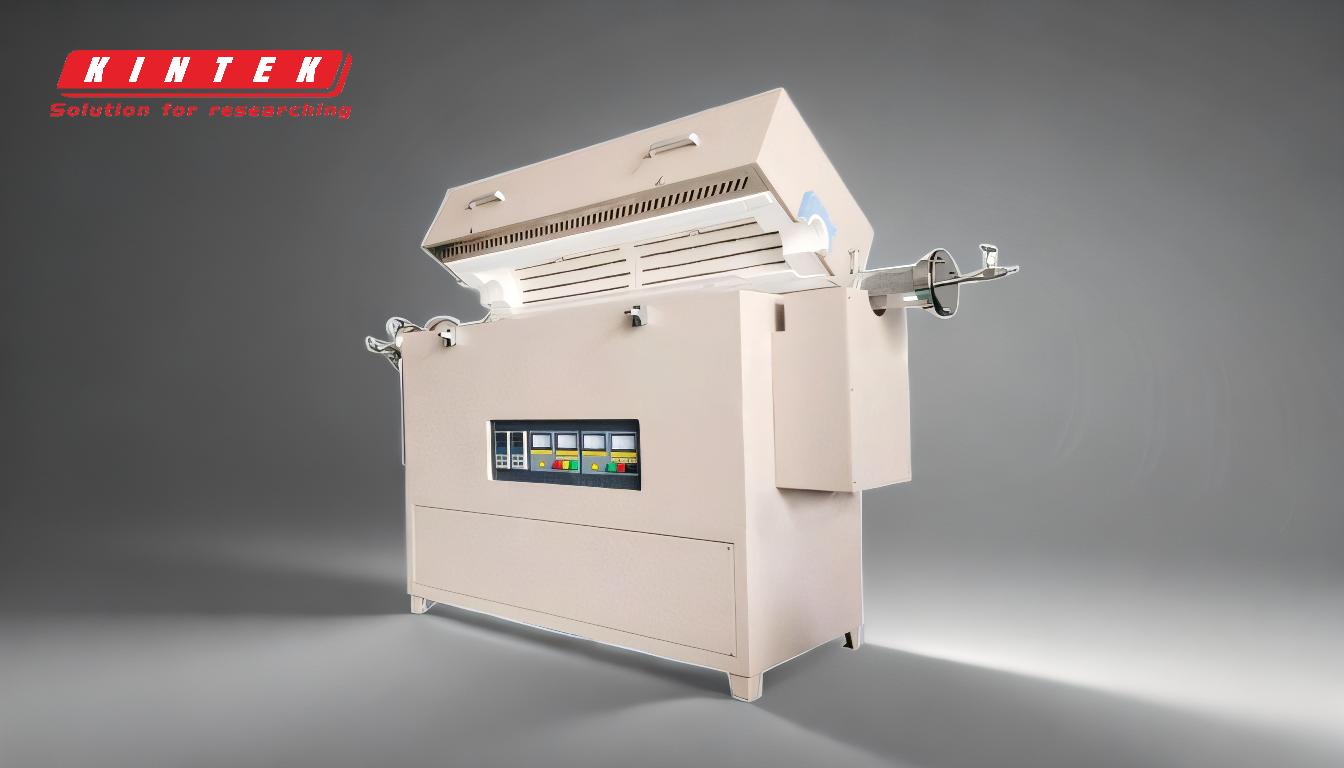
-
Understand the Basic Structure and Functionality
- Tube furnaces consist of cylindrical chambers surrounded by heating elements, which enable rapid heating, recovery, and cooling.
- They are designed for a range of applications, with features like independent digital control modules, double-shell construction, and split-hinge designs for horizontal or vertical usage.
- These furnaces typically heat tubes that are 50 cm to 100 cm in length and 25 mm to 100 mm in diameter, with samples placed inside using ceramic or metal boats.
-
Evaluate Heating Requirements
- Consider the specific heating needs of your process, such as rapid thermal processing, high-temperature and high-pressure capabilities, or uniform heating and coating of powders.
- Ensure the furnace can achieve the required temperature range and heating uniformity for your application.
- Functional considerations may also include integration with other systems like CVD, PECVD, or ALD systems.
-
Select the Appropriate Work Tube Material
- The work tube material must withstand the maximum operating temperature and have appropriate chemical resistance to prevent unwanted reactions with sample materials.
- Common materials include quartz, alumina, and stainless steel, each suited for different temperature ranges and chemical environments.
-
Consider Safety and Compliance
- Determine if specific guidelines, standards, or test procedures must be followed for your application.
- Assess any special hazards associated with experiments, such as toxic fumes or explosive materials, and ensure the furnace has adequate safety features.
- Verify if adequate air exchange is required inside the kiln to maintain a safe working environment.
-
Assess Operational Features
- Look for features that enhance usability, such as independent digital control modules, variable density insulation, and split-hinge designs for flexible installation.
- Evaluate the furnace's thermal efficiency, ease of operation, and maintenance requirements.
-
Match the Furnace to Your Industry Needs
- Tube furnaces are widely used in industries like metallurgy, glass, heat treatment, and new energy. Ensure the furnace you choose aligns with the specific demands of your industry.
- For example, in the new energy sector, a furnace with high-temperature capabilities and uniform heating may be essential for battery material processing.
By systematically evaluating these factors, you can select a tube furnace that meets your technical requirements, ensures safety, and enhances operational efficiency.
Summary Table:
Key Factor | Description |
---|---|
Structure & Functionality | Cylindrical chambers, heating elements, digital controls, and flexible designs. |
Heating Requirements | Temperature range, uniformity, and integration with systems like CVD or ALD. |
Work Tube Material | Quartz, alumina, or stainless steel for temperature and chemical resistance. |
Safety & Compliance | Follow guidelines, assess hazards, and ensure adequate air exchange. |
Operational Features | Digital controls, thermal efficiency, and ease of maintenance. |
Industry Needs | Match furnace capabilities to metallurgy, glass, heat treatment, or new energy. |
Ready to find the perfect tube furnace for your needs? Contact us today and let our experts guide you!