Isostatic presses work by applying uniform pressure from all directions to compact or densify materials, such as powders, into a desired shape. This process is achieved using either gas (in hot isostatic pressing, or HIP) or liquid (in cold isostatic pressing, or CIP) as the pressure medium. The materials are placed in a flexible mold or container, which is then subjected to high pressure and, in the case of HIP, high temperatures. The uniform pressure ensures consistent density and shape in the final product. Isostatic presses are widely used in industries like aerospace, automotive, and ceramics for creating high-strength, defect-free components.
Key Points Explained:
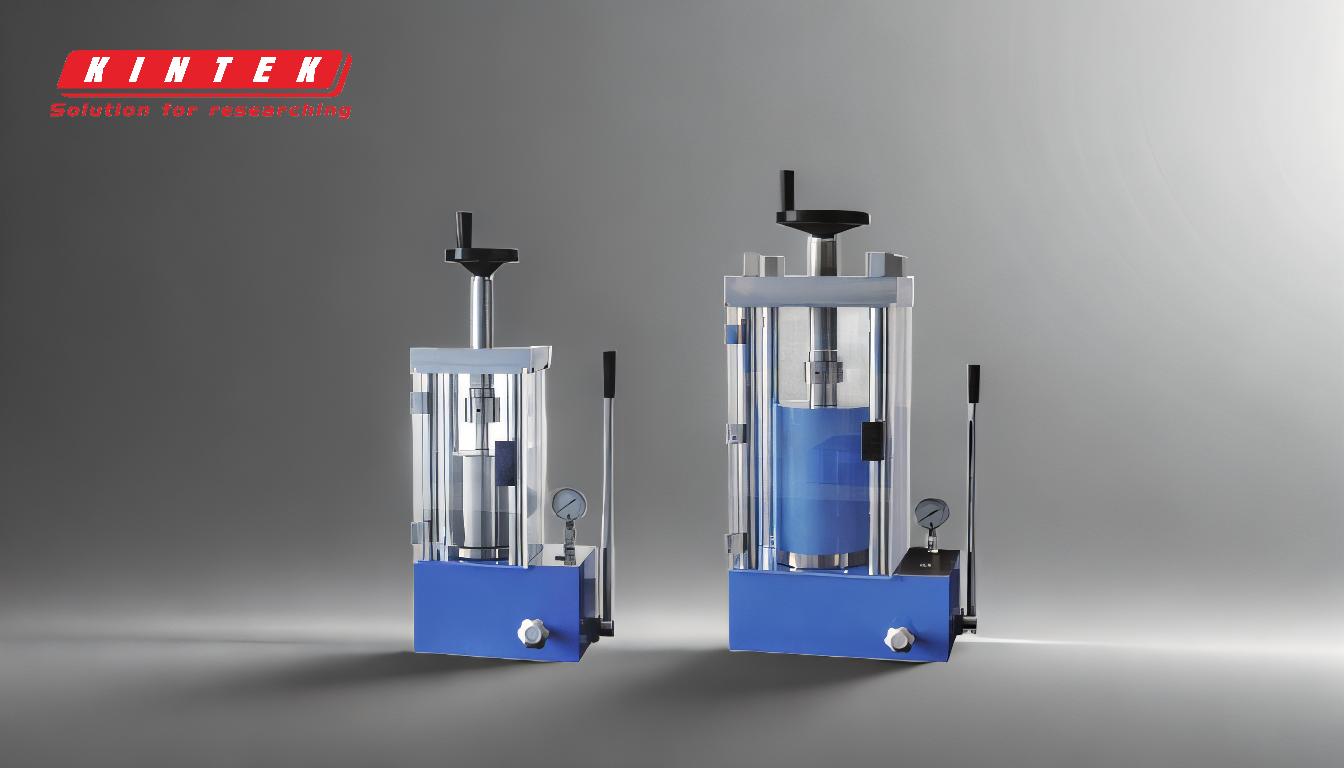
-
Principle of Isostatic Pressing:
- Isostatic pressing relies on the principle of applying uniform pressure from all directions, known as hydrostatic pressure. This ensures that the material being processed experiences equal force on every surface, leading to uniform density and shape.
- An analogy is an object submerged deep underwater, where water pressure comes from all around, not just one direction. This principle is key to achieving consistent results in isostatic pressing.
-
Types of Isostatic Pressing:
-
Cold Isostatic Pressing (CIP):
- In CIP, a liquid medium (often an oil-water mixture) is used to apply pressure. The powder material is placed in a flexible mold, which is then inserted into a high-pressure chamber. The liquid is pumped in and pressurized uniformly, typically up to 100,000 psi, to compact the powder into the desired shape.
- CIP is commonly used for ceramics, metals, and composites where high-temperature processing is not required.
-
Hot Isostatic Pressing (HIP):
- HIP uses a gas, such as argon, as the pressure medium. The material is placed in a sealed container, and both high pressure (up to 100,000 psi) and high temperature (up to 3000°F) are applied simultaneously. This process densifies the material and eliminates internal defects, making it ideal for producing high-strength components in industries like aerospace and automotive.
-
Cold Isostatic Pressing (CIP):
-
Key Components of Isostatic Presses:
-
High-Pressure Cavity:
- The high-pressure cavity is designed to withstand extreme pressures. It often uses a prestressed winding structure with steel wire for added strength and safety. Even if some steel wires fracture, the risk of catastrophic failure is minimized.
-
Flexible Mold:
- In both CIP and HIP, a flexible rubber or plastic mold is used to contain the material. The mold transmits the uniform pressure to the powder, ensuring consistent compaction.
-
Filtration System:
- The high-pressure cavity is equipped with a composite filter unit to remove impurities from the working medium. This ensures smooth operation and prevents blockages in the system.
-
High-Pressure Cavity:
-
Applications of Isostatic Pressing:
- Isostatic pressing is used to create high-density, defect-free components in various industries:
- Aerospace: For manufacturing turbine blades and other critical components.
- Automotive: For producing engine parts and other high-strength components.
- Ceramics: For creating complex shapes with uniform density.
- Medical: For producing biocompatible implants and prosthetics.
- Isostatic pressing is used to create high-density, defect-free components in various industries:
-
Advantages of Isostatic Pressing:
- Uniform Density: The equal pressure from all directions ensures uniform density in the final product.
- Complex Shapes: Isostatic pressing can produce intricate shapes that are difficult to achieve with other methods.
- Defect Elimination: HIP, in particular, is effective at removing internal defects, such as voids and porosity, resulting in stronger materials.
- Versatility: Isostatic pressing can be used with a wide range of materials, including metals, ceramics, and plastics.
-
Safety Features:
- The use of a prestressed winding structure in the high-pressure cavity enhances safety by reducing the risk of failure under extreme conditions.
- The filtration system and design of components like the superhigh-pressure throttle valve ensure resistance to impurities and blockages, further improving reliability.
By understanding how isostatic press works, manufacturers can leverage this technology to produce high-quality, high-performance components for a variety of applications.
Summary Table:
Aspect | Details |
---|---|
Principle | Applies uniform hydrostatic pressure from all directions for consistent results. |
Types | - CIP: Uses liquid medium, up to 100,000 psi. |
- HIP: Uses gas medium, up to 100,000 psi and 3000°F. | |
Key Components | - High-pressure cavity with safety features. |
- Flexible mold for uniform compaction.
- Filtration system for smooth operation. | | Applications | Aerospace, automotive, ceramics, and medical industries. | | Advantages | Uniform density, complex shapes, defect elimination, and material versatility. | | Safety Features | Prestressed winding structure and filtration system for reliability. |
Discover how isostatic presses can transform your manufacturing process—contact our experts today!