Calculating the power consumption of an induction furnace involves understanding the relationship between the material being melted, the furnace's efficiency, and the desired production rate. There are two primary methods to calculate power consumption: one uses a standard power consumption rate (e.g., 625 kWh/ton for steel), and the other employs a detailed formula that accounts for specific heat, material weight, heating temperature, time, and efficiency. Both methods are essential for determining the required power supply capacity, which ensures the furnace operates efficiently and meets production goals. Factors such as charge cleanliness, furnace design, and refractory materials also influence power consumption and overall efficiency.
Key Points Explained:
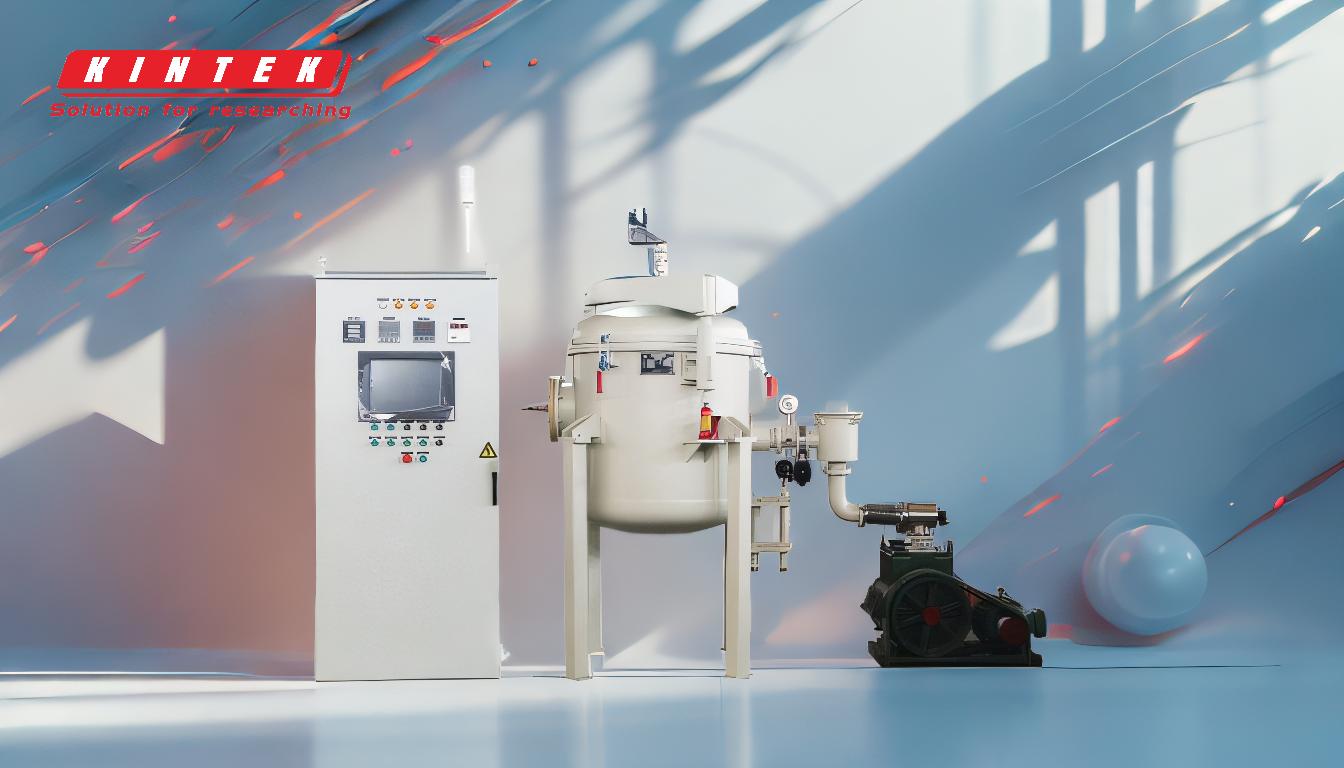
-
Standard Power Consumption Method:
- This method uses a predefined power consumption rate, such as 625 kWh/ton for steel.
- To calculate the required power supply capacity:
- Determine the hourly production rate (e.g., 520 kg/hour for a yearly production target of 2000 tons).
- Multiply the hourly production by the standard power consumption rate (625 kWh/1000 kg).
- Example: (520 kg/hour) * (625 kWh/1000 kg) = 325 kW.
- This method is straightforward and useful for quick estimations based on standard materials.
-
Detailed Formula Method:
- The formula used is:
[ P = \frac{C \times T \times G}{0.24 \times t \times \eta} ] Where:- ( P ) = Power (kW)
- ( C ) = Specific heat of the material (kcal/kg℃)
- ( T ) = Heating temperature (℃)
- ( G ) = Workpiece weight (kg)
- ( t ) = Time (seconds)
- ( \eta ) = Heating efficiency (typically 0.6 for induction furnaces).
- This method accounts for material-specific properties and provides a more precise calculation.
- Example: For a material with ( C = 0.12 ) kcal/kg℃, ( T = 1500 )℃, ( G = 1000 ) kg, ( t = 3600 ) seconds, and ( \eta = 0.6 ): [ P = \frac{0.12 \times 1500 \times 1000}{0.24 \times 3600 \times 0.6} \approx 347 \text{ kW}. ]
- The formula used is:
-
Factors Influencing Power Consumption:
- Melting Rate and Power Configuration: Higher melting rates require more power, and the power supply must be configured accordingly.
- Charge Cleanliness and Size: Clean and appropriately sized charges improve efficiency and reduce power consumption.
- Refractory Materials: The type of crucible (e.g., quartz) and furnace lining materials affect heat transfer and energy efficiency.
- Furnace Design: Properly designed furnaces with optimal block lengths and insulation minimize energy losses.
-
Practical Considerations for Equipment Purchasers:
- Production Goals: Calculate power requirements based on desired production rates (e.g., yearly or hourly targets).
- Material-Specific Calculations: Use the detailed formula for materials with non-standard properties or when precision is critical.
- Efficiency Improvements: Invest in high-quality refractory materials and ensure proper furnace maintenance to reduce power consumption.
- Energy-Saving Designs: Consider furnaces designed for low energy consumption and high efficiency, especially for small-scale operations.
By combining these methods and considerations, equipment purchasers can accurately determine the power consumption of an induction furnace and select a system that aligns with their production needs and efficiency goals.
Summary Table:
Method | Key Details | Example Calculation |
---|---|---|
Standard Power Consumption | Uses predefined rates (e.g., 625 kWh/ton for steel). | (520 kg/hour) * (625 kWh/1000 kg) = 325 kW. |
Detailed Formula | Accounts for specific heat, weight, temperature, time, and efficiency. | P = (0.12 * 1500 * 1000) / (0.24 * 3600 * 0.6) ≈ 347 kW. |
Factors Influencing Power | Melting rate, charge cleanliness, refractory materials, and furnace design. | Higher melting rates and clean charges improve efficiency. |
Practical Considerations | Production goals, material-specific calculations, and energy-saving designs. | Use detailed formulas for precision and invest in high-quality refractory materials. |
Need help calculating your induction furnace's power requirements? Contact our experts today for tailored solutions!