To check the ash content of a sample using a muffle furnace, the process involves preparing the sample, heating it at high temperatures to burn off organic matter, and measuring the remaining inorganic residue (ash). The most common method is dry ashing, which is suitable for materials stable up to 900°C, such as polymers and rubbers. The steps include preparing the furnace, setting the temperature, placing the sample in a porcelain boat, heating it, and calculating the ash content based on the weight difference before and after ashing. Proper handling of the furnace, including temperature control and safety precautions, is essential for accurate results.
Key Points Explained:
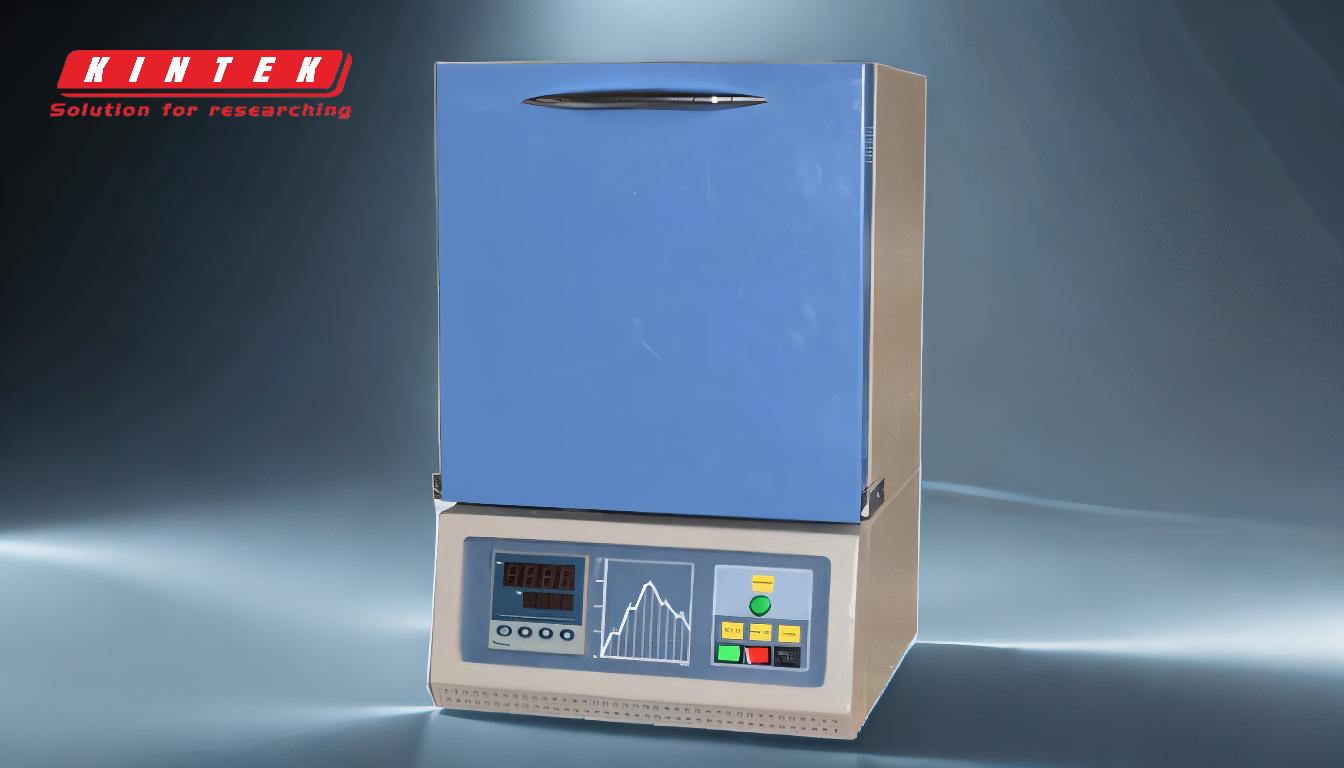
-
Understanding Ash Content Determination:
- Ash content refers to the inorganic residue left after burning off organic matter in a sample.
- It is commonly measured using a muffle furnace, which can reach high temperatures (up to 900°C).
- The two primary methods are dry ashing and wet ashing, with dry ashing being the most widely used for its simplicity and suitability for materials like polymers and rubbers.
-
Preparing the Muffle Furnace:
- Initial Setup: Ensure the furnace is clean, undamaged, and placed on a flat, stable surface. Avoid vibrations and overheating of the controller.
- Thermocouple Installation: Insert the thermocouple into the furnace, filling gaps with asbestos rope, and connect it to the controller using compensation wires with correct polarity.
- Power and Grounding: Install a power switch at the power line inlet and ensure the furnace and controller are properly grounded.
- Temperature Calibration: Adjust the thermometer to zero before use, considering the cold end compensator if applicable.
-
Sample Preparation:
- Flatten the sample in a porcelain boat to ensure even heating.
- Avoid making the sample layer too thick, as this can lead to incomplete ashing.
- Ensure the sample is stable and won’t tip over during heating.
-
Heating Process:
- Power On and Temperature Setting: Turn on the power and set the desired temperature using the controller.
- Initial Heating: For the first use or after a long period of disuse, heat the furnace empty to stabilize the temperature and reduce impurities.
- Placing the Sample: Place the prepared sample into the furnace chamber, ensuring it is stable and not in direct contact with the heating element to prevent fire risks.
- Monitoring: Keep the furnace door closed during heating to maintain temperature and prevent heat loss. Monitor the temperature indicator lights (green for heating, red for constant temperature).
-
Calculating Ash Content:
- After heating, allow the furnace to cool to a safe temperature.
- Weigh the remaining inorganic residue (ash) and calculate the ash content using the formula: [ \text{Ash Content (%)} = \frac{\text{Weight of Ash}}{\text{Weight of Original Sample}} \times 100 ]
- Ensure accurate measurements by using a precision balance.
-
Safety and Maintenance:
- Always follow safety protocols, such as wearing protective gear and ensuring proper ventilation.
- Regularly clean the furnace to prevent contamination and ensure consistent performance.
- Avoid placing flammable or volatile materials directly into the furnace to prevent accidents.
By following these steps, you can accurately determine the ash content of a sample using a muffle furnace, ensuring reliable and consistent results for applications in materials science, food analysis, and other fields.
Summary Table:
Step | Key Actions |
---|---|
1. Prepare the Furnace | Clean, install thermocouple, ensure proper grounding, and calibrate temperature. |
2. Prepare the Sample | Flatten in a porcelain boat, avoid thick layers, and ensure stability. |
3. Heating Process | Set temperature, heat furnace empty initially, and monitor heating indicators. |
4. Calculate Ash Content | Weigh ash residue, use formula to calculate percentage ash content. |
5. Safety & Maintenance | Wear protective gear, clean regularly, and avoid flammable materials. |
Need help with ash content analysis? Contact our experts today for tailored solutions!