Cooling a muffle furnace requires careful attention to avoid rapid temperature changes that could damage the furnace or pose safety risks. The process involves turning off the power and allowing the furnace to cool naturally. Opening the door immediately after use is discouraged to prevent heat shock and potential hazards. While some muffle furnaces have basic fan-based exhaust systems to remove toxic gases, they lack sophisticated cooling mechanisms. Gradual cooling is essential to protect the furnace's internal components, such as refractories, and ensure safe operation.
Key Points Explained:
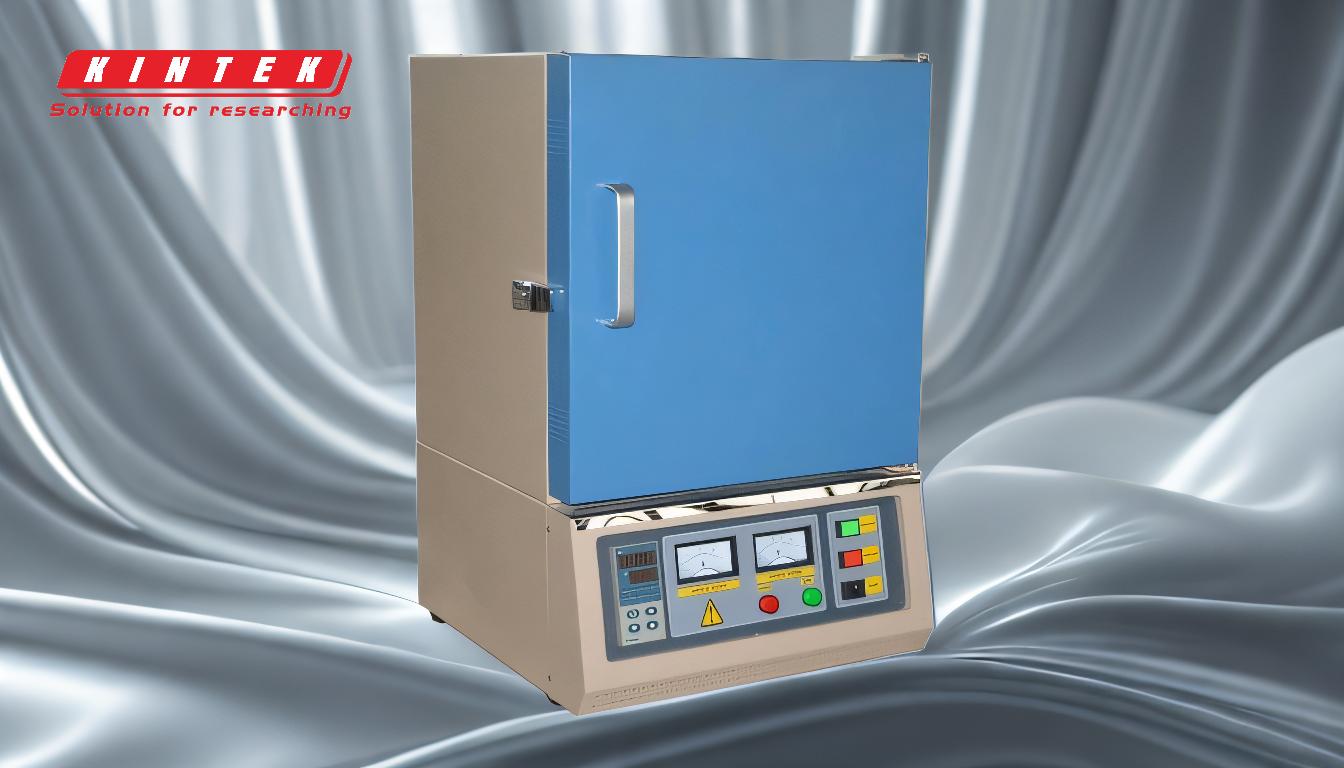
-
Turn Off the Power and Allow Natural Cooling
- After using the muffle furnace, the first step is to turn off the power. This stops further heating and allows the furnace to begin cooling.
- Natural cooling is preferred because it prevents rapid temperature changes, which can damage the furnace's internal components, such as refractories.
- Opening the door immediately after turning off the power is not recommended, as it can expose the furnace to a sharp temperature decline, leading to heat shock and potential safety hazards.
-
Avoid Rapid Cooling
- Rapid cooling can cause thermal stress on the furnace's materials, leading to cracks or other damage.
- Gradual cooling ensures that the temperature decreases uniformly, protecting the integrity of the furnace chamber and its components.
- This is particularly important for high-temperature furnaces, where sudden temperature changes can be more detrimental.
-
Do Not Open the Door Immediately
- Opening the door while the furnace is still hot can result in heat shock, which can damage the refractories and other sensitive parts of the furnace.
- It also poses a safety risk to the operator, as sudden exposure to high temperatures can cause burns or other injuries.
- Wait until the furnace has cooled sufficiently before opening the door to retrieve samples or perform maintenance.
-
Basic Cooling Systems in Muffle Furnaces
- Most lab muffle furnaces are not equipped with advanced cooling systems. Instead, they rely on simple fan-based exhaust systems, sometimes supported by a chimney.
- These systems are primarily designed to remove toxic gases generated during the heating process, not to actively cool the furnace.
- As a result, natural cooling remains the primary method for reducing the furnace's temperature after use.
-
Gradual Temperature Reduction
- If the furnace has a temperature control system, gradually reducing the setpoint temperature can help achieve a more controlled cooling process.
- This method is particularly useful in industrial settings where maintaining consistent cooling rates is critical for process integrity.
- However, in most lab settings, simply turning off the furnace and allowing it to cool naturally is sufficient and safer.
-
Prioritize Safety
- Safety should always be the top priority when cooling a muffle furnace. Avoid actions that could lead to rapid temperature changes or expose the operator to high heat.
- Ensure that the furnace is placed in a well-ventilated area to allow heat to dissipate effectively.
- Regularly inspect the furnace for signs of wear or damage, as these can compromise safety during the cooling process.
By following these guidelines, you can ensure that your muffle furnace cools safely and efficiently, extending its lifespan and maintaining optimal performance.
Summary Table:
Key Steps | Details |
---|---|
Turn Off the Power | Stop heating and allow natural cooling to prevent thermal stress. |
Avoid Rapid Cooling | Gradual cooling protects internal components like refractories. |
Do Not Open the Door Immediately | Prevents heat shock and safety hazards. Wait until the furnace cools. |
Basic Cooling Systems | Most muffle furnaces use fan-based exhaust systems, not advanced cooling. |
Gradual Temperature Reduction | Gradually lower the setpoint temperature for controlled cooling. |
Prioritize Safety | Ensure proper ventilation and inspect for wear to maintain safe operation. |
Need help with your muffle furnace? Contact our experts today for personalized advice and solutions!