Induction coils, particularly those used in induction furnaces, require effective cooling to prevent overheating and ensure optimal performance. Cooling is typically achieved using a water-based system, where cold water is circulated through the coils via flexible cables. This process is essential to maintain the coil's temperature within safe limits, as excessive heat can damage the coil and reduce its efficiency. Additionally, the cooling system often operates in tandem with other equipment, such as air conditioners, to manage the overall thermal environment. This ensures the longevity and reliability of the induction furnace system.
Key Points Explained:
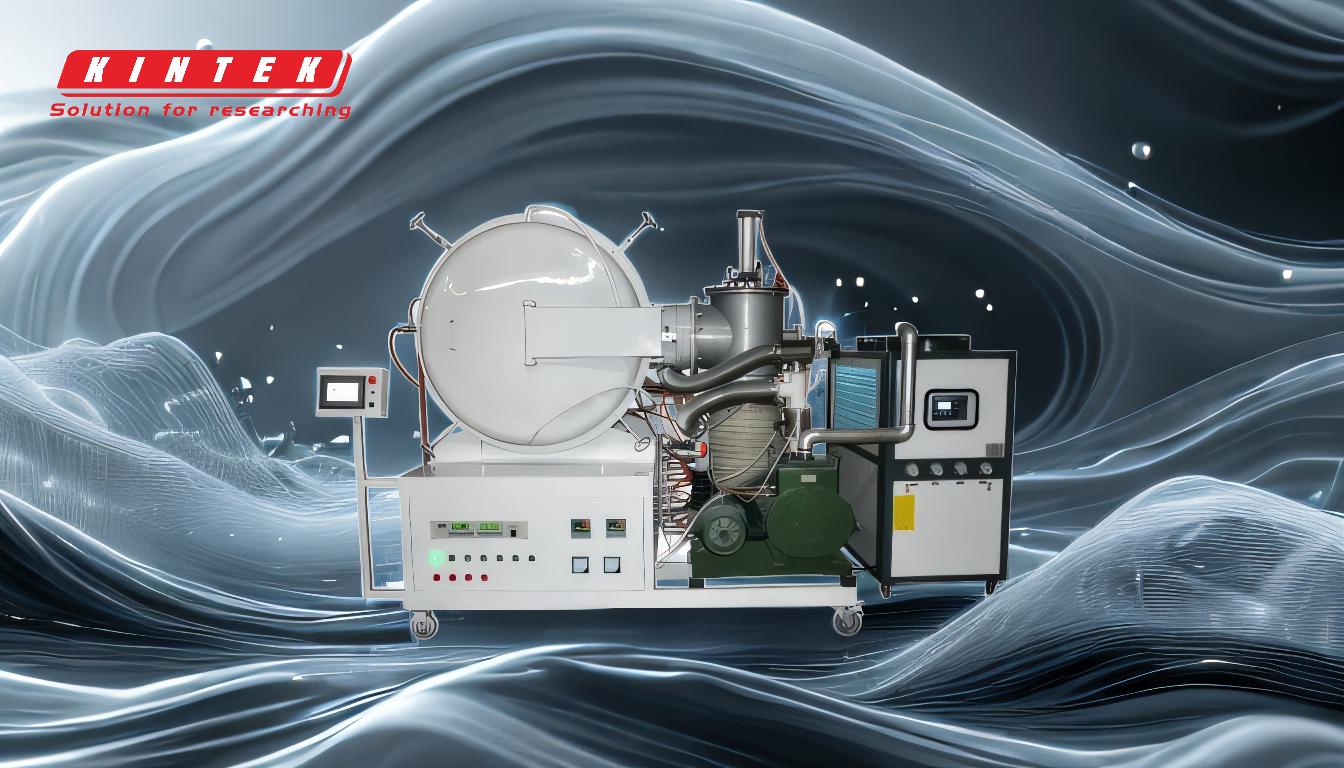
-
Importance of Cooling Induction Coils
- Induction coils generate significant heat during operation due to the high-frequency electrical currents passing through them. Without proper cooling, the coils can overheat, leading to:
- Degradation of the coil material.
- Reduced efficiency of the induction process.
- Potential failure of the coil or other components.
- Cooling is critical to maintain the coil's structural integrity and ensure consistent performance.
- Induction coils generate significant heat during operation due to the high-frequency electrical currents passing through them. Without proper cooling, the coils can overheat, leading to:
-
Water-Based Cooling Systems
- The most common method for cooling induction coils is through a water-based system. Key features include:
- Cold Water Supply: Cold water is circulated through the coils to absorb and dissipate heat.
- Flexible Cables: Flexible hoses or cables are used to deliver water to the coils, allowing for easy installation and maintenance.
- Closed-Loop Systems: Many systems use a closed-loop design, where the same water is continuously circulated, cooled, and reused.
- The most common method for cooling induction coils is through a water-based system. Key features include:
-
Simultaneous Operation of Furnace and Cooling Systems
- For effective cooling, the induction furnace and its cooling system must operate simultaneously. This ensures:
- Real-time heat dissipation during furnace operation.
- Prevention of temperature spikes that could damage the coil.
- The cooling system is often integrated with other thermal management equipment, such as air conditioners, to maintain a stable operating environment.
- For effective cooling, the induction furnace and its cooling system must operate simultaneously. This ensures:
-
Design Considerations for Cooling Systems
- When designing or selecting a cooling system for induction coils, consider:
- Flow Rate: Ensure sufficient water flow to remove heat effectively.
- Temperature Control: Use temperature sensors and controllers to monitor and regulate water temperature.
- Material Compatibility: Choose materials for hoses and fittings that can withstand high temperatures and corrosive environments.
- Maintenance: Design the system for easy access and maintenance to prevent downtime.
- When designing or selecting a cooling system for induction coils, consider:
-
Alternative Cooling Methods
- While water-based cooling is the most common, other methods may be used in specific applications:
- Air Cooling: Suitable for smaller or less intensive systems, but less efficient than water cooling.
- Oil Cooling: Used in high-temperature applications where water cooling is impractical.
- Phase-Change Cooling: Advanced systems that use refrigerants to absorb and dissipate heat more efficiently.
- While water-based cooling is the most common, other methods may be used in specific applications:
-
Safety and Efficiency
- Proper cooling not only protects the induction coil but also enhances the overall efficiency and safety of the system. Benefits include:
- Extended equipment lifespan.
- Reduced risk of malfunctions or accidents.
- Improved energy efficiency by maintaining optimal operating conditions.
- Proper cooling not only protects the induction coil but also enhances the overall efficiency and safety of the system. Benefits include:
By understanding these key points, equipment purchasers can make informed decisions about cooling systems for induction coils, ensuring they select the most suitable and effective solution for their specific needs.
Summary Table:
Key Aspect | Details |
---|---|
Importance of Cooling | Prevents overheating, material degradation, and efficiency loss. |
Water-Based Cooling | Uses cold water circulation, flexible cables, and closed-loop systems. |
Simultaneous Operation | Ensures real-time heat dissipation and prevents temperature spikes. |
Design Considerations | Flow rate, temperature control, material compatibility, and maintenance. |
Alternative Cooling Methods | Air cooling, oil cooling, and phase-change cooling for specific needs. |
Safety and Efficiency | Extends equipment lifespan, reduces malfunctions, and improves energy use. |
Need help selecting the right cooling system for your induction coils? Contact our experts today for tailored solutions!