Sintering at lower temperatures is a critical goal in materials science and manufacturing, as it reduces energy consumption, minimizes thermal stress, and allows for greater control over material properties. This can be achieved through various methods, including applying pressure, using advanced sintering techniques like Spark Plasma Sintering (SPS) or Microwave Sintering, and optimizing material composition. Lower-temperature sintering is particularly beneficial for materials with high melting points and enables energy-efficient processes like 3D printing. Below, we explore the key strategies and methods for lowering sintering temperatures.
Key Points Explained:
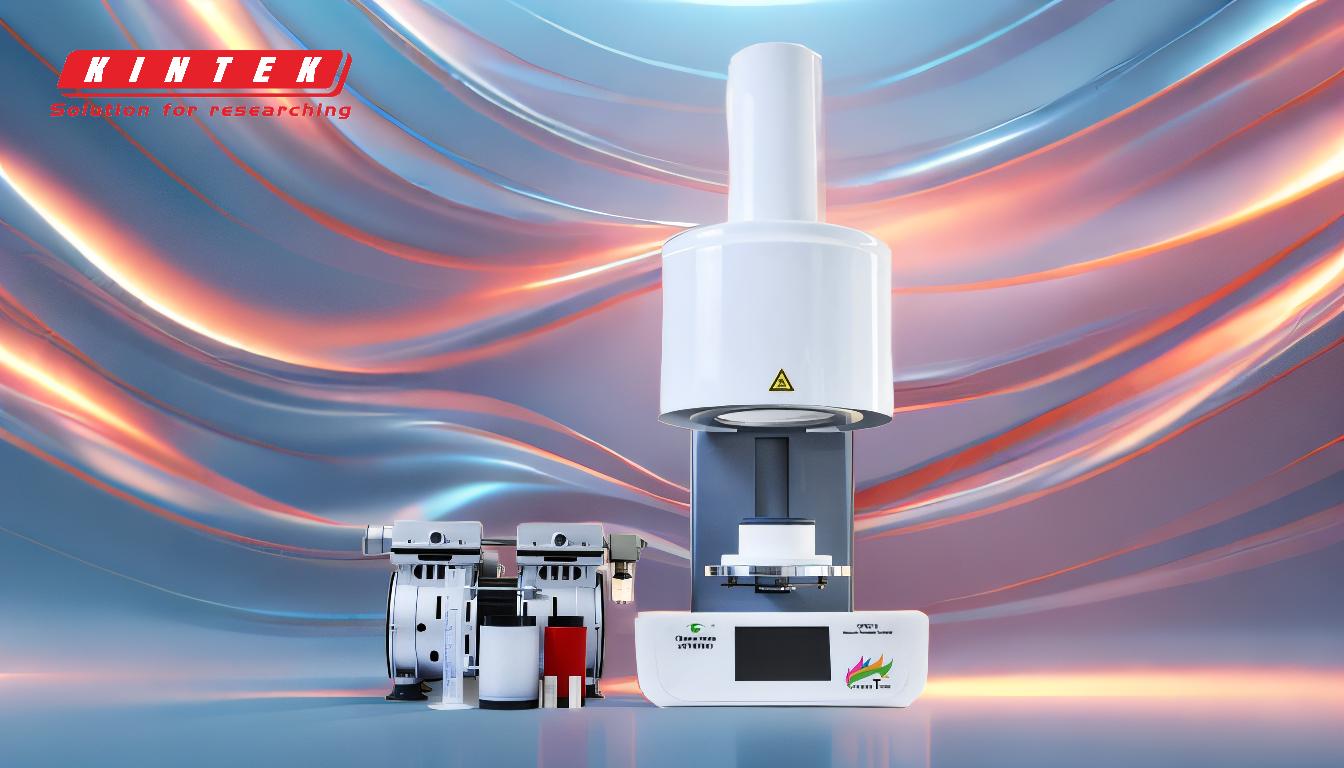
-
Applying Pressure to Lower Sintering Temperature
- Sintering can occur at lower temperatures when sufficient pressure is applied. This is because pressure enhances particle contact and diffusion, reducing the energy required for densification.
- High-pressure methods, such as hot pressing or isostatic pressing, are often used to achieve this effect. These techniques compress the material while heating, promoting densification without requiring extremely high temperatures.
- This approach is particularly useful for materials that are difficult to sinter at low temperatures, such as ceramics or refractory metals.
-
Advanced Sintering Techniques
-
Spark Plasma Sintering (SPS):
- SPS is a rapid sintering method that uses pulsed electric currents to generate heat internally within the material. This allows for sintering at lower temperatures and shorter times compared to conventional methods.
- The electric current also promotes localized heating at particle interfaces, enhancing diffusion and densification.
-
Microwave Sintering:
- Microwave sintering uses electromagnetic waves to heat the material volumetrically, rather than relying on external heat sources. This results in faster and more uniform heating, enabling sintering at lower temperatures.
- It is particularly effective for materials that absorb microwave energy efficiently, such as certain ceramics and composites.
-
Spark Plasma Sintering (SPS):
-
Optimizing Material Composition
- Adding sintering aids or dopants can significantly lower the sintering temperature. These additives reduce the activation energy required for diffusion and promote densification at lower temperatures.
- For example, adding small amounts of glass-forming oxides or low-melting-point metals can enhance sintering in ceramic or metallic systems.
- Particle size and morphology also play a role. Smaller particles have higher surface energy, which facilitates sintering at lower temperatures.
-
Benefits of Lower-Temperature Sintering
- Energy Efficiency: Lowering the sintering temperature reduces energy consumption, making the process more sustainable and cost-effective.
- Material Integrity: High temperatures can cause grain growth, phase transformations, or thermal stresses, which degrade material properties. Lower temperatures help maintain the desired microstructure and mechanical properties.
- Compatibility with Advanced Manufacturing: Low-temperature sintering is essential for processes like 3D printing, where layer-by-layer fabrication requires precise control over material properties and energy usage.
-
Applications and Future Directions
- Lower-temperature sintering is widely used in industries such as electronics, aerospace, and biomedical engineering, where precise material properties are critical.
- Ongoing research focuses on developing new sintering aids, optimizing advanced sintering techniques, and exploring novel materials that can be sintered at even lower temperatures.
By leveraging these strategies, manufacturers and researchers can achieve high-quality sintering results while conserving energy and improving material performance.
Summary Table:
Method | Key Benefits |
---|---|
Applying Pressure | Enhances particle contact, reduces energy for densification, ideal for ceramics. |
Spark Plasma Sintering (SPS) | Rapid sintering, lower temperatures, localized heating for better densification. |
Microwave Sintering | Volumetric heating, uniform results, effective for microwave-absorbing materials. |
Optimizing Material Composition | Reduces activation energy, improves sintering efficiency with additives. |
Benefits | Energy efficiency, material integrity, compatibility with advanced manufacturing. |
Unlock the potential of low-temperature sintering for your applications—contact our experts today!