Polishing a PVD (Physical Vapor Deposition) coating requires careful consideration of the coating's properties, such as hardness, thickness, and adhesion, to avoid damaging the underlying material or the coating itself. The process involves selecting appropriate tools, abrasives, and techniques to achieve a smooth, reflective, or matte finish, depending on the desired outcome. Understanding the nature of the PVD coating, including its deposition method and material composition, is crucial for determining the best polishing approach.
Key Points Explained:
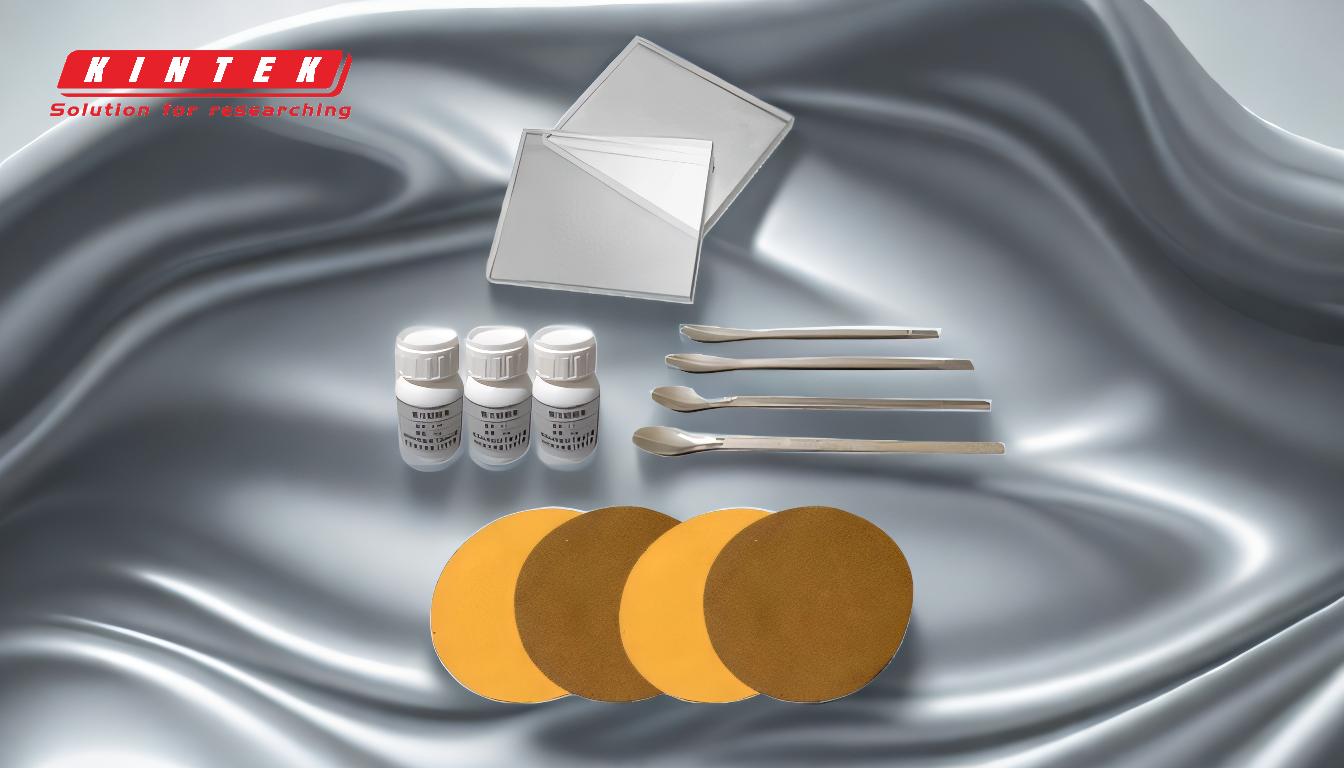
-
Understanding PVD Coating Properties:
- PVD coatings are known for their hardness, durability, and resistance to wear and corrosion. These properties are influenced by factors such as the deposition method (e.g., thermal evaporation, cathodic arc, sputtering), coating thickness, and the specific materials used.
- The hardness of the coating, for example, will determine the type of abrasives and tools required for polishing. Softer coatings may require finer abrasives, while harder coatings might need diamond-based tools.
-
Preparation Before Polishing:
- Ensure the surface is clean and free of contaminants. Any debris or oils can interfere with the polishing process and lead to uneven results.
- Inspect the coating for defects such as pinholes, cracks, or uneven thickness. Addressing these issues before polishing can prevent further damage.
-
Selecting the Right Tools and Abrasives:
- For softer PVD coatings, use fine-grit abrasives like polishing compounds or diamond pastes with a grit size of 1 micron or less.
- For harder coatings, diamond-impregnated tools or diamond lapping films may be necessary.
- Polishing wheels or pads made from materials like felt, leather, or foam can be used depending on the desired finish.
-
Polishing Techniques:
- Manual Polishing: Suitable for small or intricate parts. Use a soft cloth or pad with the chosen abrasive and apply even pressure in circular motions.
- Machine Polishing: Ideal for larger or flat surfaces. Use a rotary tool or polishing machine with adjustable speed settings to avoid overheating the coating.
- Lapping: For achieving a mirror-like finish, lapping with a fine abrasive slurry can be effective.
-
Post-Polishing Care:
- After polishing, clean the surface thoroughly to remove any residual abrasives or polishing compounds.
- Inspect the coating for uniformity and check for any signs of damage or wear caused during the polishing process.
- Apply a protective layer, such as a clear coat or wax, to enhance the coating's durability and appearance.
-
Safety Considerations:
- Wear appropriate personal protective equipment (PPE), such as gloves and safety glasses, to protect against abrasives and dust.
- Ensure proper ventilation when using polishing compounds or working with fine particles.
By following these steps and considering the specific characteristics of the PVD coating, you can achieve a polished finish that enhances both the aesthetic and functional properties of the coated material.
Summary Table:
Step | Key Details |
---|---|
1. Understand PVD Properties | Hardness, thickness, and adhesion influence polishing methods. |
2. Preparation | Clean the surface and inspect for defects before polishing. |
3. Tools & Abrasives | Use fine-grit abrasives for soft coatings, diamond tools for hard coatings. |
4. Polishing Techniques | Manual, machine, or lapping methods depending on the surface and desired finish. |
5. Post-Polishing Care | Clean thoroughly, inspect for uniformity, and apply a protective layer. |
6. Safety | Wear PPE and ensure proper ventilation during polishing. |
Need help polishing your PVD coating? Contact our experts today for tailored solutions!