Starting a pyrolysis tyre plant involves a series of well-defined steps, from initial planning and setup to the actual processing of waste tires into valuable products. The process begins with the collection and preparation of waste tires, followed by feeding them into a pyrolysis reactor where they are heated to break down into oil, carbon black, steel wire, and gas. The plant must be equipped with systems for heating, condensing, and separating these products, as well as handling the by-products. Additionally, regulatory compliance, environmental considerations, and market analysis are crucial for successful operation. Below is a detailed breakdown of the key steps and considerations involved in starting a pyrolysis tyre plant.
Key Points Explained:
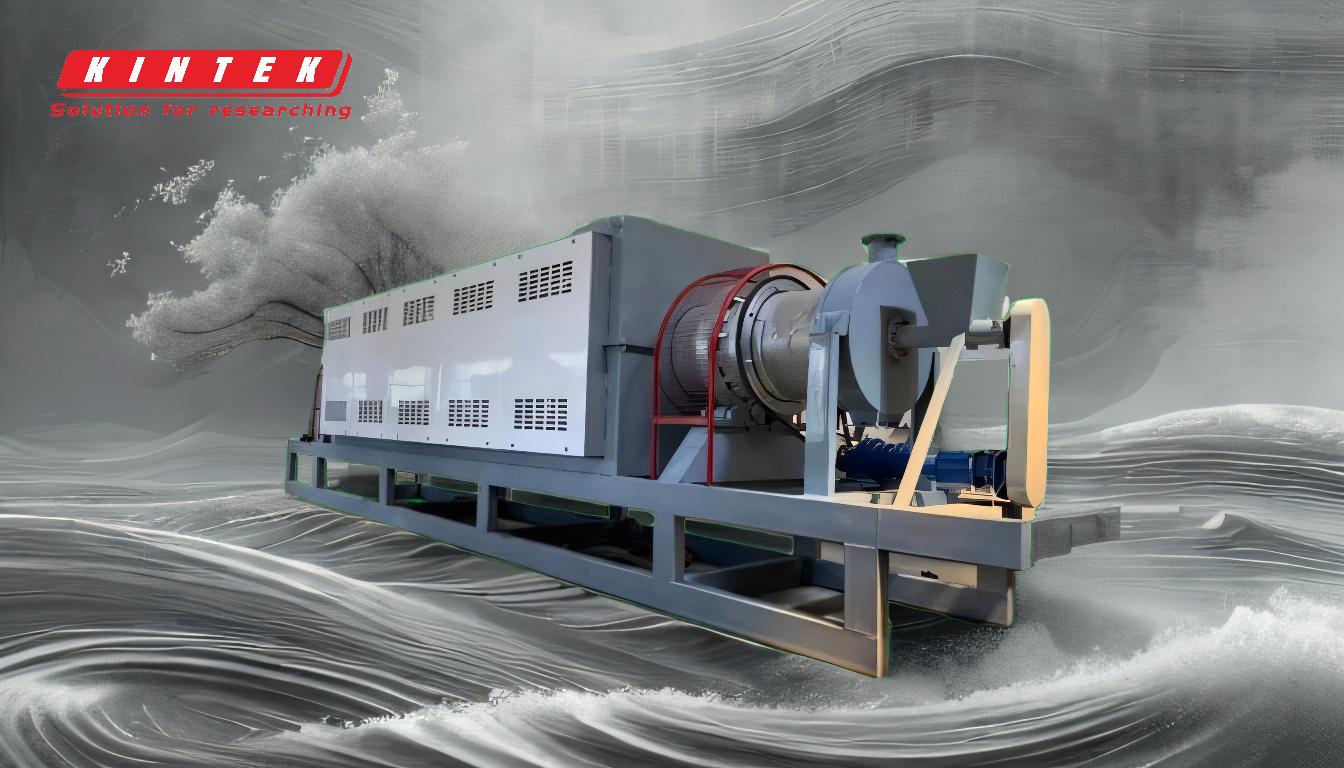
-
Market Research and Feasibility Study
- Conduct a thorough market analysis to understand the demand for pyrolysis products such as tire oil, carbon black, and steel wire in your region.
- Assess the availability of waste tires as raw material and identify potential suppliers.
- Evaluate the financial viability, including initial investment, operational costs, and potential revenue streams.
-
Regulatory Compliance and Permits
- Obtain necessary permits and licenses for operating a pyrolysis plant, including environmental clearances.
- Ensure compliance with local, state, and national regulations regarding waste management and emissions.
- Implement safety protocols to meet occupational health and safety standards.
-
Site Selection and Plant Setup
- Choose a location with adequate space for the plant, storage of raw materials, and finished products.
- Ensure the site has access to utilities such as electricity, water, and transportation facilities.
- Install the pyrolysis reactor, condensing system, and other necessary equipment.
-
Raw Material Collection and Preparation
- Collect waste tires from various sources, including tire shops, recycling centers, and landfills.
- Shred the tires into smaller pieces to facilitate efficient processing in the pyrolysis reactor.
- Use magnetic separation to remove steel wires from the shredded tires.
-
Pyrolysis Process
- Feed the prepared tire pieces into the pyrolysis reactor.
- Heat the reactor to temperatures above 100-120°C to initiate the pyrolysis process, breaking down the tires into vaporized gas, carbon black, and steel wire.
- Condense the vaporized gas into liquid tire oil using a heat exchange system.
- Collect the non-condensable gas, which can be reused to heat the reactor or treated through a wet scrubber system to minimize emissions.
-
Product Collection and Storage
- Separate and collect the final products: tire oil, carbon black, and steel wire.
- Store the products in appropriate containers or facilities to maintain their quality.
- Ensure proper handling and storage of carbon black, which can be sold as a raw material for various industries.
-
Environmental and Safety Measures
- Install emission control systems such as wet scrubbers to minimize air pollution.
- Implement waste management practices to handle any residual by-products safely.
- Train staff on safety protocols and emergency response procedures.
-
Marketing and Distribution
- Develop a marketing strategy to sell the pyrolysis products to industries such as fuel, construction, and manufacturing.
- Establish distribution channels to ensure timely delivery of products to customers.
- Build relationships with potential buyers and negotiate favorable terms.
-
Continuous Improvement and Maintenance
- Regularly maintain and inspect the pyrolysis plant to ensure optimal performance and longevity.
- Monitor the quality of the products and make adjustments to the process as needed.
- Stay updated on advancements in pyrolysis technology and incorporate improvements to enhance efficiency and profitability.
By following these steps, you can establish a successful pyrolysis tyre plant that not only recycles waste tires but also generates valuable products, contributing to environmental sustainability and economic growth.
Summary Table:
Step | Key Actions |
---|---|
Market Research | Analyze demand, assess raw material availability, evaluate financial viability. |
Regulatory Compliance | Obtain permits, ensure environmental and safety compliance. |
Site Selection & Setup | Choose a location with utilities, install pyrolysis equipment. |
Raw Material Preparation | Collect and shred tires, remove steel wires. |
Pyrolysis Process | Heat tires, condense gas into oil, collect carbon black and steel wire. |
Product Collection | Separate and store tire oil, carbon black, and steel wire. |
Environmental Measures | Install emission controls, manage by-products, train staff. |
Marketing & Distribution | Develop strategies, establish channels, build buyer relationships. |
Maintenance & Improvement | Regularly inspect and update the plant for efficiency. |
Ready to transform waste tires into valuable resources? Contact us today to start your pyrolysis tyre plant journey!