A CVD (Chemical Vapor Deposition) machine works by facilitating a series of chemical reactions that deposit a thin film of material onto a substrate. The process begins with the introduction of precursor gases into a reaction chamber, where they undergo decomposition, combination, or other chemical reactions. These reactions are often enhanced by heat, plasma, or reduced pressure, depending on the specific type of CVD process. The resulting solid material is deposited onto the substrate in either crystalline or amorphous form, improving surface properties such as smoothness, conductivity, and compatibility with other materials. The process involves discrete steps, including precursor delivery, surface reaction, and by-product removal, ensuring a controlled and uniform deposition.
Key Points Explained:
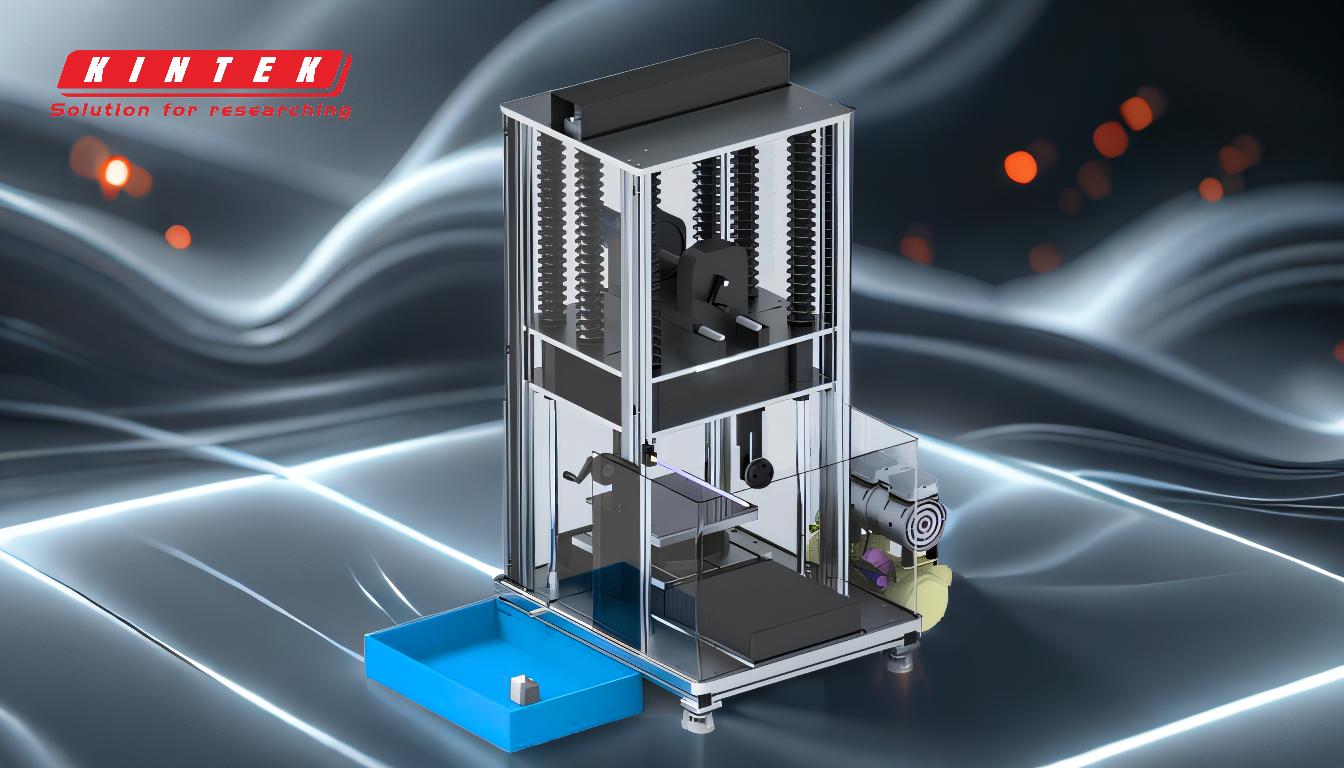
-
Chemical Reactions in CVD:
- The CVD process relies on key chemical reactions such as decomposition, combination, hydrolysis, oxidation, and reduction of precursor gases. These reactions produce a solid material that deposits onto the substrate.
- The reactions are influenced by factors like temperature, pressure, and the presence of plasma, which can lower the required reaction temperatures significantly.
-
Types of CVD Processes:
- Thermal CVD: Uses heat to drive chemical reactions. It operates at high temperatures and is suitable for depositing materials like silicon dioxide and silicon nitride.
- Plasma-Enhanced CVD (PECVD): Utilizes plasma to excite gas molecules, enabling reactions at lower temperatures. This is particularly useful for depositing films on temperature-sensitive substrates.
- Other variants include low-pressure CVD (LPCVD) and atomic layer deposition (ALD), each tailored for specific applications and material properties.
-
Process Steps in CVD:
- Precursor Delivery: Gaseous precursors are introduced into the reaction chamber. These precursors are often volatile compounds that can decompose or react under specific conditions.
- Transport and Adsorption: The precursor molecules are transported to the substrate surface through fluid dynamics and diffusion. They then adsorb onto the surface.
- Surface Reaction: The adsorbed molecules undergo chemical reactions, forming a solid film on the substrate. By-products of these reactions are desorbed and removed from the chamber.
- Film Growth: The process continues, layer by layer, until the desired film thickness is achieved.
-
Role of Plasma in PECVD:
- In PECVD, a glow-discharge plasma is created within the reaction chamber using an RF field. This plasma decomposes gas molecules into reactive species, enabling chemical reactions at lower temperatures.
- The plasma environment operates at reduced pressures (50 mtorr to 5 torr) and generates high electron and ion densities, which facilitate efficient film deposition.
-
Benefits of CVD:
- Surface Enhancement: CVD improves surface properties such as smoothness, electrical conductivity, and thermal conductivity. This is achieved through the uniform deposition of material on the substrate.
- Material Compatibility: The process enhances the compatibility of the substrate with other materials, making it suitable for applications in electronics, optics, and coatings.
- Versatility: CVD can deposit a wide range of materials, including metals, ceramics, and polymers, making it a highly versatile technique.
-
Applications of CVD:
- Semiconductor Manufacturing: CVD is extensively used to deposit thin films of materials like silicon, silicon dioxide, and silicon nitride in the production of integrated circuits.
- Optical Coatings: CVD is employed to create anti-reflective and protective coatings on lenses and mirrors.
- Protective Coatings: It is used to apply wear-resistant and corrosion-resistant coatings on tools and components.
By understanding these key points, one can appreciate the complexity and versatility of CVD machines, which are essential tools in modern material science and engineering.
Summary Table:
Aspect | Details |
---|---|
Key Chemical Reactions | Decomposition, combination, hydrolysis, oxidation, and reduction of gases. |
Types of CVD Processes | Thermal CVD, Plasma-Enhanced CVD (PECVD), Low-Pressure CVD (LPCVD), ALD. |
Process Steps | Precursor delivery, transport and adsorption, surface reaction, film growth. |
Role of Plasma in PECVD | Excites gas molecules, enabling reactions at lower temperatures. |
Benefits | Surface enhancement, material compatibility, and versatility. |
Applications | Semiconductor manufacturing, optical coatings, and protective coatings. |
Ready to explore how a CVD machine can transform your material science projects? Contact our experts today for tailored solutions!