A melting furnace, particularly an induction melting furnace, operates on the principle of electromagnetic induction to melt metals efficiently. It consists of key components such as a power supply, induction coil, and a crucible made of refractory materials. The furnace generates heat by inducing eddy currents in the metal charge, which acts as a secondary winding of a transformer. This process allows for precise temperature control, energy efficiency, and rapid melting. Advanced features like vacuum induction melting further enhance its capabilities, making it suitable for specialized applications such as melting high-temperature alloys, rare earth metals, and non-ferrous metals under controlled atmospheres.
Key Points Explained:
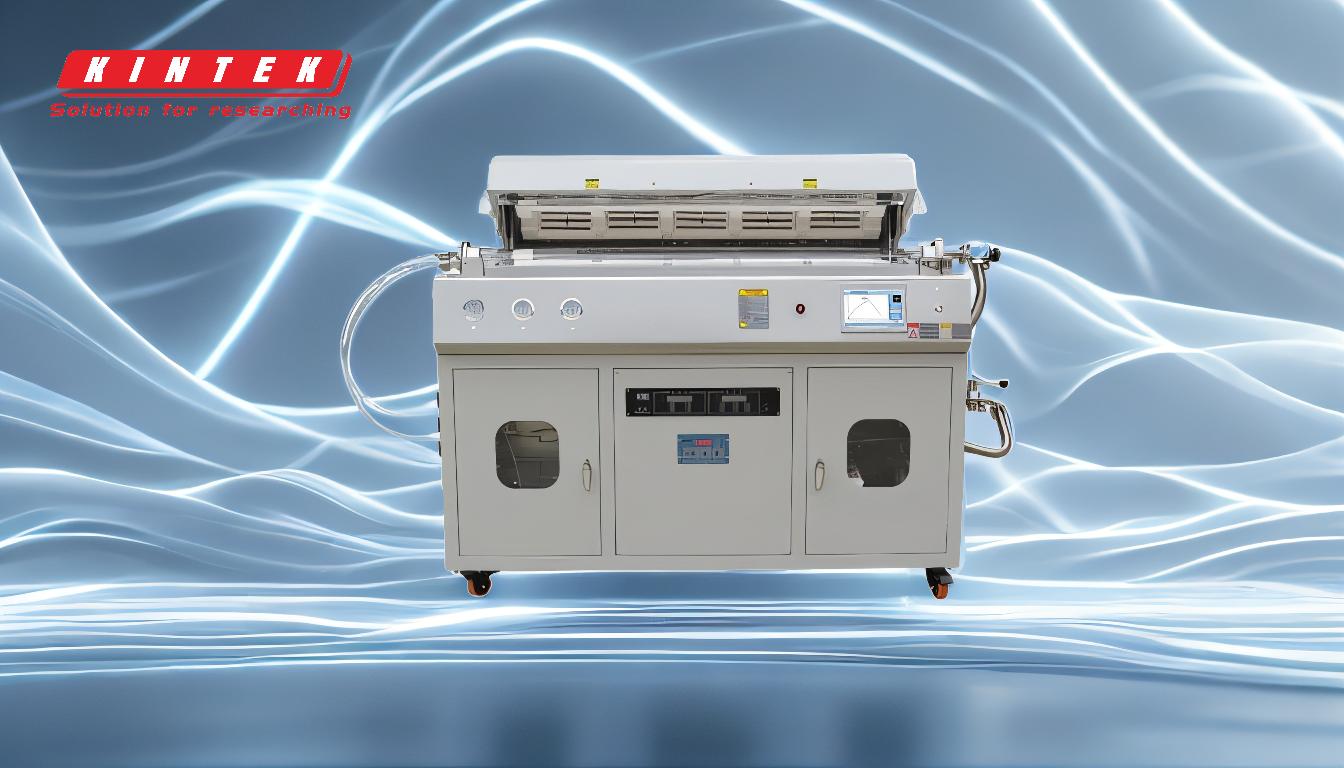
-
Principle of Operation:
- Induction melting furnaces work on the principle of electromagnetic induction. An alternating current passes through the induction coil, creating a magnetic field. This field induces eddy currents in the metal charge placed inside the crucible, generating heat and melting the metal.
- The process is contactless, as the induction coil does not directly touch the metal, ensuring minimal contamination and high efficiency.
-
Core Components:
- Power Supply: Provides the alternating current required to generate the magnetic field. Medium-frequency power supplies are commonly used for their efficiency and controllability.
- Induction Coil: A water-cooled coil that surrounds the crucible and generates the magnetic field necessary for induction heating.
- Crucible: Made of refractory materials, it holds the metal charge and withstands high temperatures during the melting process.
- Furnace Shell: An air-tight structure, often water-cooled, that maintains the required vacuum or protective atmosphere in vacuum induction melting furnaces.
-
Vacuum Induction Melting:
- In vacuum induction melting furnaces, the process occurs under vacuum or inert gas conditions, preventing oxidation and contamination. This is especially useful for melting high-purity metals, nickel-based alloys, and rare earth materials.
- The furnace shell is designed to withstand high vacuum levels, and the system includes vacuum pumps, gas control systems, and monitoring devices.
-
Control and Automation:
- Modern melting furnaces are equipped with advanced control systems that allow preset heating power and time. Infrared thermometers and automated controls ensure precise temperature regulation, improving heating quality and production efficiency.
- Features like observation windows, temperature measurement devices, and feeding systems enhance operational convenience.
-
Applications:
- Induction melting furnaces are versatile and used for melting a wide range of materials, including carbon steel, alloy steel, non-ferrous metals (copper, aluminum, lead, zinc), and specialized alloys like high-temperature and precision alloys.
- They are compact, energy-efficient, and capable of rapid melting, making them ideal for both industrial and research applications.
-
Advantages:
- Energy Efficiency: Induction heating directly transfers energy to the metal, minimizing heat loss.
- Precision: Accurate temperature control ensures consistent melting and high-quality output.
- Speed: Rapid heating and melting reduce processing time.
- Cleanliness: The contactless process and controlled atmospheres prevent contamination.
-
Additional Features:
- Tilting mechanisms for easy pouring of molten metal.
- Water cooling systems to maintain safe operating temperatures.
- Sampling and feeding devices for process control and material addition during melting.
By understanding these key points, a purchaser can evaluate the suitability of a melting furnace for their specific needs, ensuring efficient and high-quality metal processing.
Summary Table:
Key Aspect | Details |
---|---|
Principle of Operation | Electromagnetic induction generates heat via eddy currents in the metal. |
Core Components | Power supply, induction coil, crucible, and furnace shell. |
Vacuum Induction Melting | Melts metals under vacuum or inert gas to prevent contamination. |
Control & Automation | Advanced systems for precise temperature control and process automation. |
Applications | Melts carbon steel, non-ferrous metals, high-temperature alloys, and more. |
Advantages | Energy-efficient, precise, fast, and contamination-free. |
Discover how an induction melting furnace can revolutionize your metal processing—contact us today for expert advice!