A plasma arc furnace operates by using a high-energy plasma arc to melt and refine metals. The process involves generating a plasma arc between an electrode and the metal, which heats the material to extremely high temperatures. This allows for efficient melting and refining of metals, often with better control over the chemical composition and purity compared to traditional methods. The furnace typically operates in a controlled environment, often with reduced gas pressure, to optimize the plasma generation and stability. The plasma arc furnace is particularly useful for processing refractory metals and alloys that require high temperatures and precise control.
Key Points Explained:
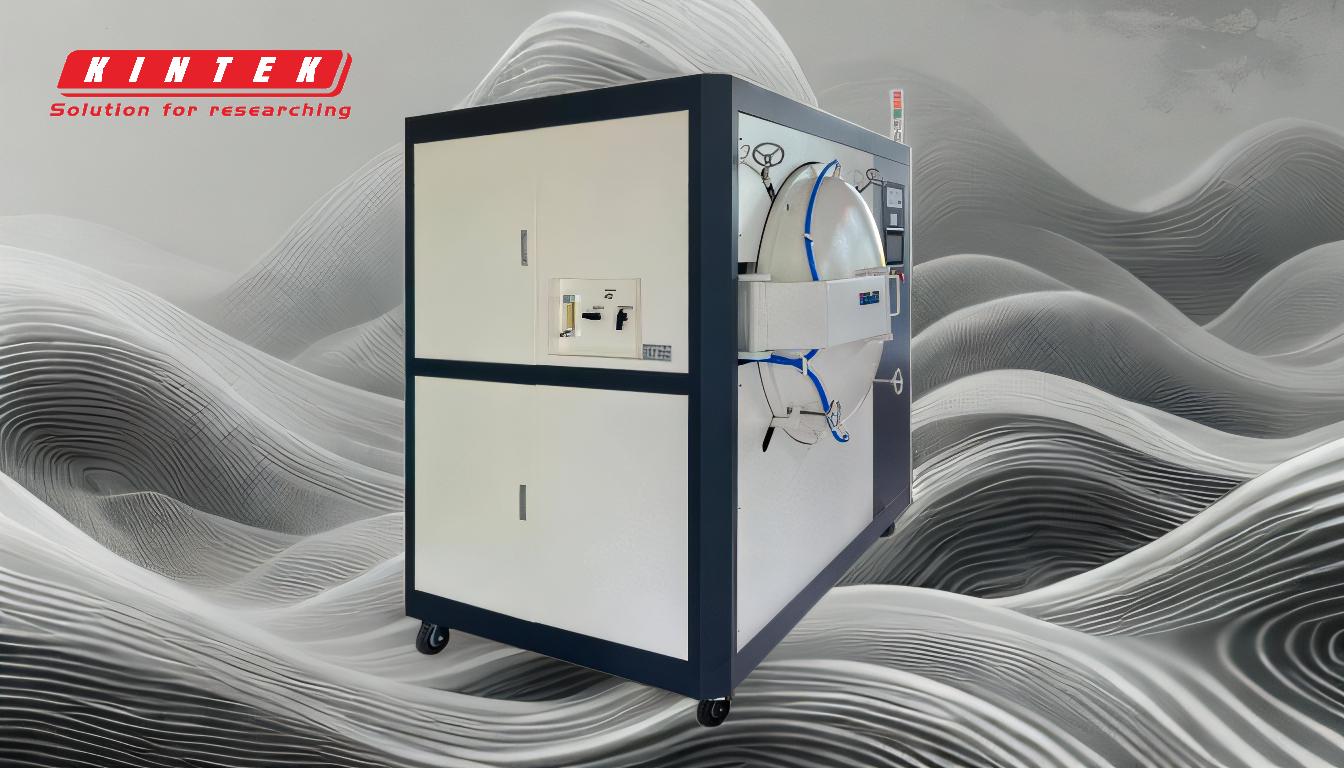
-
Generation of Plasma Arc:
- The plasma arc is created by ionizing gas between an electrode and the metal charge. This ionization produces a high-temperature plasma, which can reach temperatures up to 20,000°C, far exceeding those achievable in conventional electric arc furnaces.
- The plasma is typically generated using a high-frequency electric field, similar to the RF field used in PECVD processes, which excites the gas molecules to form a plasma.
-
Melting and Refining Process:
- Once the plasma arc is established, it transfers intense heat to the metal charge, causing it to melt. The high temperatures also facilitate the refining process by allowing impurities to be more easily separated and removed.
- The process can include the addition of fluxes or other materials to aid in slag formation, similar to the use of burnt lime and spar in traditional electric arc furnaces.
-
Controlled Environment:
- Plasma arc furnaces often operate in a controlled atmosphere, which can be adjusted to optimize the plasma generation and stability. This environment is typically maintained at reduced gas pressures, similar to the conditions in PECVD processes, to enhance the efficiency of the plasma arc.
- The controlled environment also helps in preventing contamination of the metal, ensuring a higher purity of the final product.
-
Applications and Advantages:
- Plasma arc furnaces are particularly useful for melting and refining refractory metals and alloys that require extremely high temperatures. They offer better control over the chemical composition and purity of the metal compared to traditional methods.
- The precise control over the plasma arc allows for more efficient energy use and can result in lower operational costs over time.
-
Equipment Design:
- A typical plasma arc furnace includes a water-cooled chamber, often made of stainless steel, to contain the high-temperature plasma and molten metal. The electrode (or stinger) is positioned to direct the plasma arc towards the metal charge.
- The hearth, where the metal is melted, is usually water-cooled and may have an interchangeable surface to accommodate different types of metal charges.
By understanding these key points, a purchaser can better evaluate the suitability of a plasma arc furnace for their specific needs, considering factors such as the types of metals to be processed, the required purity levels, and the operational environment.
Summary Table:
Key Aspect | Description |
---|---|
Plasma Arc Generation | Ionized gas creates a plasma arc reaching up to 20,000°C, using high-frequency electric fields. |
Melting & Refining Process | Intense heat melts metals, aiding impurity removal and slag formation for higher purity. |
Controlled Environment | Operates in reduced gas pressure to optimize plasma stability and prevent contamination. |
Applications | Ideal for refractory metals and alloys requiring extreme temperatures and precise control. |
Equipment Design | Includes water-cooled chambers, electrodes, and interchangeable hearths for versatile use. |
Ready to optimize your metal processing? Contact us today to explore plasma arc furnace solutions!