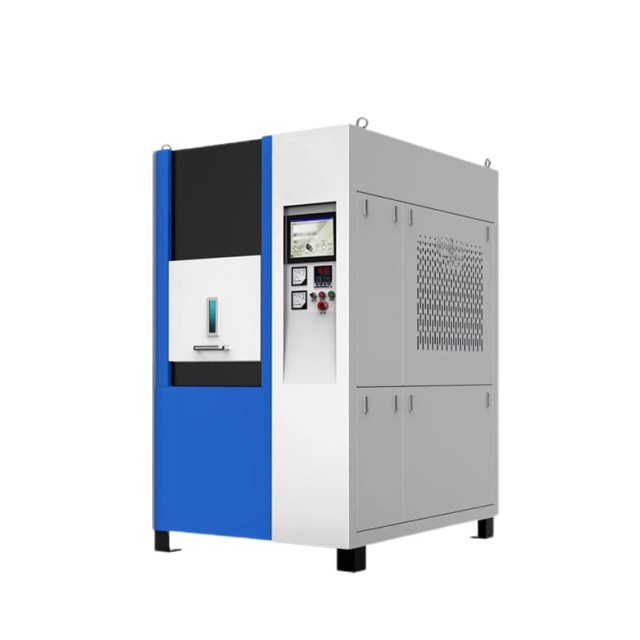
Vacuum Hot Press Furnace
Spark Plasma Sintering Furnace SPS Furnace
Item Number : KTSP
Price varies based on specs and customizations
- Output current
- 0-30000 A
- Rated temperature
- 2300 ℃
- Rated pressure
- 100-500 KN
- Sample size
- Ø30-Ø200 mm
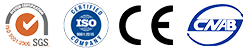
Shipping:
Contact us to get shipping details Enjoy On-time Dispatch Guarantee.
Why Choose Us
Reliable PartnerEasy ordering process, quality products, and dedicated support for your business success.
Introduction
Spark Plasma Sintering (SPS) is a rapid material preparation method that utilizes pulsed current to sinter materials directly in a mold. It combines plasma activation, hot pressing, and resistance heating, offering several advantages over traditional sintering methods. SPS enables uniform heating, high heating rates, low sintering temperatures, short sintering times, and high production efficiency. It also purifies surfaces, inhibits grain growth, and facilitates the production of uniform and controllable structures. Compared to conventional sintering, SPS is environmentally friendly, cost-effective, and requires minimal operation time.
Application
The Spark Plasma Sintering Furnace (SPS) is a versatile and advanced tool used in various scientific and industrial applications. This technology is particularly known for its ability to sinter materials at high speeds and with excellent compactness, making it ideal for a range of specialized materials and processes. Below are the main application areas of the SPS furnace:
- Sintering of Nanophase Materials: Utilized for the consolidation of nanoscale materials, enhancing their mechanical and physical properties.
- Functionally Graded Materials (FGM): Enables the creation of materials with spatially varying properties, crucial for advanced engineering applications.
- Nanoscale Thermoelectric Materials: Essential for the production of materials used in energy conversion devices.
- Rare Earth Permanent Magnets: Critical for manufacturing high-performance magnets used in various electronics and automotive applications.
- Target Materials: Used in the production of materials for thin film deposition in electronics and optics.
- Nonequilibrium Materials: Suitable for synthesizing materials that do not follow traditional equilibrium phase diagrams.
- Medical Implants: Helps in the development of biocompatible materials with precise mechanical properties for medical devices.
- Joining and Forming: Beyond sintering, SPS can be used for joining dissimilar materials and forming complex shapes.
- Surface Modification: Effective for altering the surface properties of materials to enhance durability or functionality.
- Solid Electrolyte and Electric Thermal Material Research: Ideal for the study and production of materials used in solid-state batteries and thermal management systems.
Features
The Spark Plasma Sintering Furnace (SPS) is a cutting-edge solution for rapid and efficient sintering of a wide range of materials, including metals, ceramics, and composites. This advanced furnace utilizes a unique pressure sintering method that employs on-off DC pulse currents to generate discharge plasma, discharge impact pressure, Joule heat, and electric field diffusion, significantly enhancing the sintering process. Below are the key features of the SPS furnace, highlighting how they benefit the customer:
- Automated Program Control: The SPS furnace features an advanced control system that automates critical processes such as sintering temperature, pressure, and current control. This automation not only ensures consistent and precise sintering conditions but also reduces the need for manual intervention, saving time and reducing human error.
- Enhanced Safety Measures: Equipped with a safety shutdown function, the SPS furnace automatically shuts down when it detects abnormal water temperatures, mold damage, or other emergencies. This proactive safety feature protects both the equipment and the operator, ensuring a secure working environment.
- Data Acquisition and Analysis System: The furnace includes a sophisticated data acquisition system that records and analyzes critical process parameters such as sintering voltage, current, control temperature, applied pressure, displacement, and vacuum degree. This capability allows for detailed tracking of the production process and helps in optimizing the sintering conditions for better product quality.
- User-Friendly Interface: With a large LCD touch operation panel, the SPS furnace provides real-time diagnostics and status updates, including displacement data, interlock status, alarm displays, and pressurization pressure settings. This intuitive interface simplifies operation and maintenance, making it easier for operators to manage the sintering process effectively.
- High-Pressure Graphite Mold: The use of a robust graphite mold in the SPS furnace allows for high-pressure sintering, enhancing the density and quality of the sintered products. The mold is designed with a through hole for thermocouple insertion, enabling precise temperature monitoring during the sintering process.
Detail & Parts
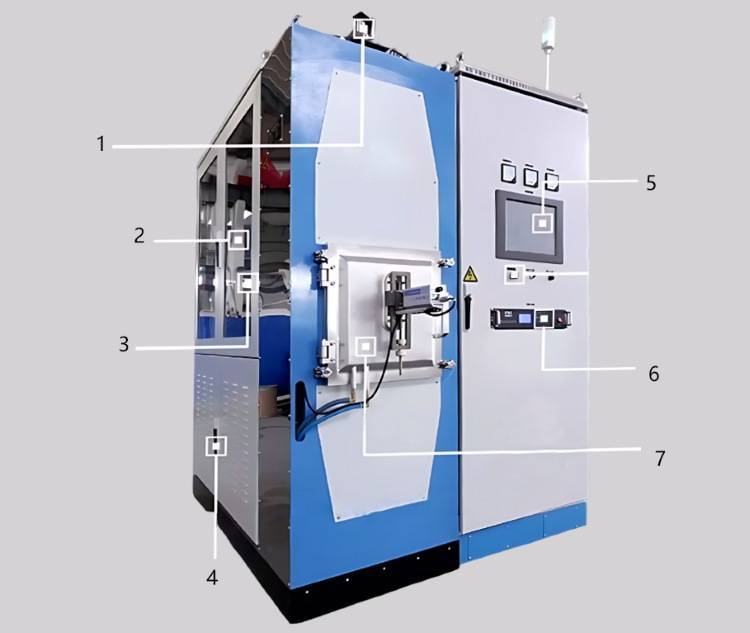
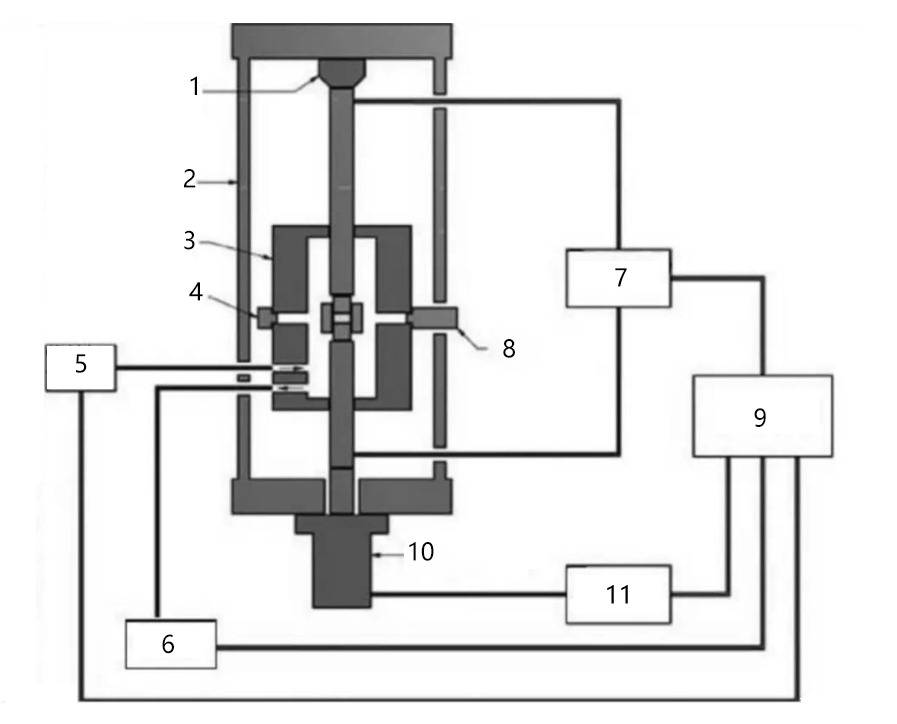
1. Loading unit 2. Loading frame 3. Vacuum chamber 4. Observation window 5. Inert gas channel 6. Vacuum pump 7. Pulse switch 8. Temperature meter 9. Control system 10. Hydraulic cylinder 11. Hydraulic system
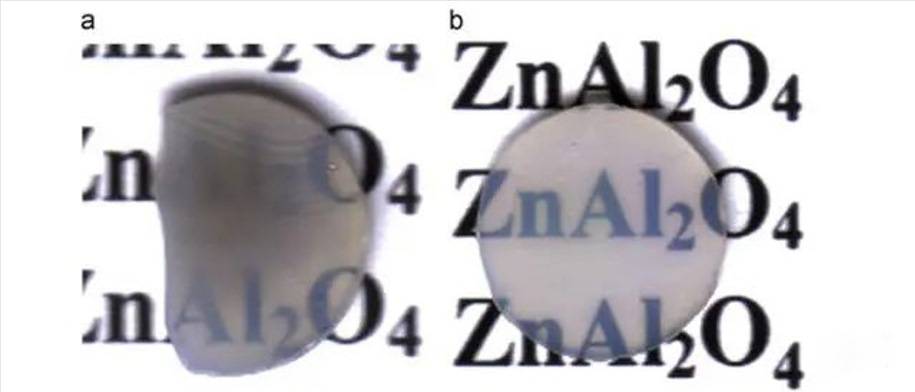
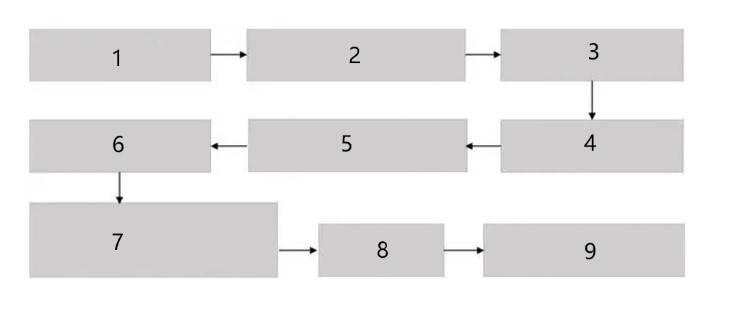
Process flow of spark plasma sintering (1.Select appropriate mold 2.Calculate the required powder mass3.Fill the mold 4.Apply pressure 5.Place in plasma sintering 6.Static pressure molding 7.Computer adjust sintering parameters plasma rapid sintering 8.Sample finished product 9.Performance testing and research)
Principle
Spark Plasma Sintering (SPS) is a rapid material preparation method that combines plasma activation, hot pressing, and resistance heating. It involves passing a pulse current directly through the mold and powder particles or bulk samples to induce sintering.
SPS utilizes the Joule heat generated by the current flow to heat the sample. The current passing through the powder creates spark discharge between adjacent particles, ionizing gas molecules and generating positrons and electrons. The resulting plasma purifies and activates the particle surfaces, promoting material migration and reducing sintering temperature and time.
The pulse current voltage applied provides high energy density, enabling rapid sintering and dispersion of the discharge point. This unique heating mode facilitates rapid cooling within the crystal structure, allowing for the preparation of high-quality amorphous and nano materials.
Advantages
- Rapid Sintering: SPS furnaces offer exceptionally fast heating rates, drastically reducing sintering time compared to traditional methods.
- Compact Structure: The compact design of SPS furnaces minimizes floor space requirements, enabling efficient deployment.
- Uniform Heating: SPS furnaces deliver uniform heating throughout the sample, ensuring consistent sintering results.
- High Heating Rate: The high heating rate of SPS furnaces enables rapid temperature increases, allowing for shorter processing times.
- Low Sintering Temperature: SPS furnaces operate at lower sintering temperatures than traditional methods, preserving material integrity.
- Surface Purification: The plasma discharge in SPS furnaces purifies the surface of particles, removing impurities and enhancing bonding.
- Grain Growth Inhibition: SPS furnaces minimize grain growth, resulting in a uniform and controllable product structure.
- Versatile Material Compatibility: SPS furnaces can sinter a wide range of materials, including metals, alloys, ceramics, and composites.
- Environmental Sustainability: SPS technology is environmentally friendly, reducing energy consumption and waste generation.
- Cost-Effectiveness: SPS furnaces offer a cost-effective solution for high-speed sintering, reducing production time and expenses.
- Solid-State Diffusion Bonding: SPS furnaces enable solid-state diffusion bonding between materials, providing high product strength and airtightness.
- Advanced Material Synthesis: SPS furnaces facilitate the synthesis of advanced materials, such as nanomaterials, functionally graded materials, and rare earth magnets.
Technical parameters
Spark Plasma Sintering Furnace (SPS) upto 20 Ton pressure and 1600ºC , is a Spark Plasma Sintering System is designed for a wide range of material research upto 1600ºC. It can be used for sintering, sinter-bonding, surface treatment, and synthesis. The sample material can be metals, ceramics, nanostructured material and amorphous material. This system is perfectly fit solid electrolyte and electric thermal material research.
Configuration |
|
Temperature controller |
|
Hydraulic Press |
|
Vacuum Chamber |
|
Dimension |
|
Technical specifications
Model | KTSP-10T-5 | KTSP-20T-6 | KTSP-20T-10 | KTSP-50T-30 |
Rated power | 50Kw | 60Kw | 100Kw | 300Kw |
Output current | 0-5000A | 0-6000A | 0-10000A | 0-30000A |
Input voltage | 0-10V | 0-10V | 0-10V | 0-10V |
Rated temperature | 2300℃ | |||
Rated pressure | 100KN | 200KN | 200KN | 500KN |
Sample size | Ø30mm | Ø50mm | Ø100mm | Ø200mm |
Ram stroke | 100mm | 100mm | 100mm | 200mm |
Ultimate vacuum | 1Pa |
Warnings
Operator safety is the top important issue! Please operate the equipment with cautions. Working with inflammable& explosive or toxic gases is very dangerous, operators must take all necessary precautions before starting the equipment. Working with positive pressure inside the reactors or chambers is dangerous, operator must fellow the safety procedures strictly. Extra caution must also be taken when operating with air-reactive materials, especially under vacuum. A leak can draw air into the apparatus and cause a violent reaction to occur.
Designed for You
KinTek provide deep custom made service and equipment to worldwide customers, our specialized teamwork and rich experienced engineers are capable to undertake the custom tailoring hardware and software equipment requirements, and help our customer to build up the exclusive and personalized equipment and solution!
Would you please drop your ideas to us, our engineers are ready for you now!
4.9
out of
5
The SPS furnace has brought about a remarkable improvement in our research capabilities, enabling us to conduct experiments and obtain results in a fraction of the time.
4.8
out of
5
This sintering furnace is a game-changer. Its speed, efficiency, and versatility have made it an indispensable tool in our lab, allowing us to explore new materials and processes.
4.7
out of
5
The SPS furnace is a well-built and reliable piece of equipment. Its user-friendly design and safety features make it an excellent choice for our research lab.
4.9
out of
5
The SPS furnace has exceeded our expectations. The quality of the sintered materials is exceptional, and the furnace's durability ensures consistent performance.
4.8
out of
5
The SPS furnace offers exceptional value for money. Its cost-effectiveness, combined with its high performance, makes it an attractive investment for any research institution.
4.7
out of
5
The SPS furnace is a testament to technological advancement. Its innovative features and groundbreaking capabilities have opened up new avenues of research for our team.
4.9
out of
5
The SPS furnace has significantly enhanced our research productivity. Its rapid sintering process has enabled us to complete experiments in a timely manner, leading to accelerated progress.
4.8
out of
5
The SPS furnace is a versatile tool that has facilitated the exploration of diverse materials and applications. Its ability to handle various materials sets it apart from other sintering furnaces.
4.7
out of
5
The SPS furnace is an invaluable asset to our lab. Its speed, reliability, and ease of use have made it a favorite among our researchers.
4.9
out of
5
The SPS furnace is a remarkable piece of equipment. Its ability to produce high-quality sintered materials in a matter of minutes is truly impressive.
Products
Spark Plasma Sintering Furnace SPS Furnace
REQUEST A QUOTE
Our professional team will reply to you within one business day. Please feel free to contact us!
Related Products
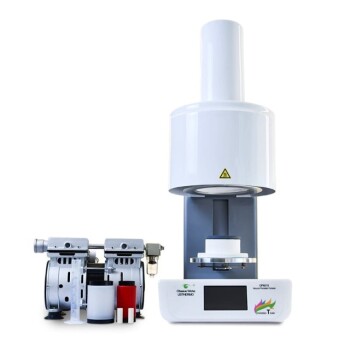
Dental Porcelain Zirconia Sintering Ceramic Vacuum Press Furnace
Get precise dental results with Dental Vacuum Press Furnace. Automatic temperature calibration, low noise tray, and touch screen operation. Order now!
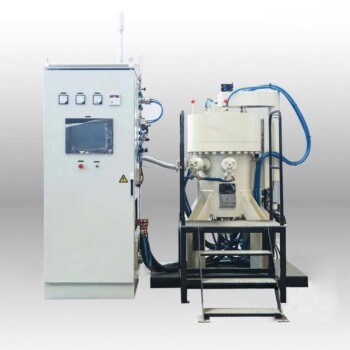
Vacuum Heat Treat and Sintering Furnace with 9MPa Air Pressure
The air pressure sintering furnace is a high-tech equipment commonly used for the sintering of advanced ceramic materials. It combines vacuum sintering and pressure sintering techniques to achieve high-density and high-strength ceramics.
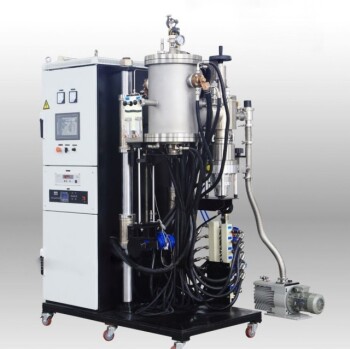
Small Vacuum Heat Treat and Tungsten Wire Sintering Furnace
The small vacuum tungsten wire sintering furnace is a compact experimental vacuum furnace specially designed for universities and scientific research institutes. The furnace features a CNC welded shell and vacuum piping to ensure leak-free operation. Quick-connect electrical connections facilitate relocation and debugging, and the standard electrical control cabinet is safe and convenient to operate.
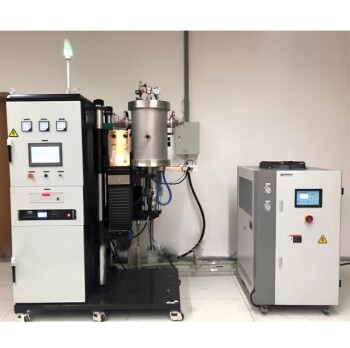
Vacuum Heat Treat and Molybdenum Wire Sintering Furnace for Vacuum Sintering
A vacuum molybdenum wire sintering furnace is a vertical or bedroom structure, which is suitable for withdrawal, brazing, sintering and degassing of metal materials under high vacuum and high temperature conditions. It is also suitable for dehydroxylation treatment of quartz materials.
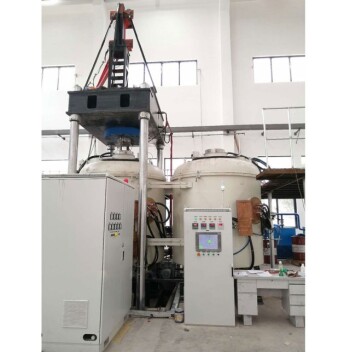
600T Vacuum Induction Hot Press Furnace for Heat Treat and Sintering
Discover the 600T Vacuum Induction Hot Press Furnace, designed for high-temperature sintering experiments in vacuum or protected atmospheres. Its precise temperature and pressure control, adjustable working pressure, and advanced safety features make it ideal for nonmetal materials, carbon composites, ceramics, and metal powders.
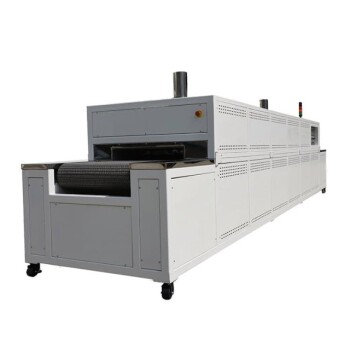
Mesh belt controlled atmosphere furnace
Discover our KT-MB mesh belt sintering furnace - perfect for high-temperature sintering of electronic components & glass insulators. Available for open air or controlled atmosphere environments.
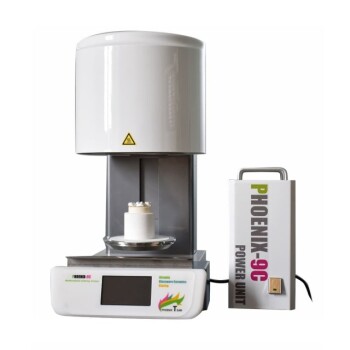
Dental Porcelain Zirconia Sintering Ceramic Furnace Chairside with Transformer
Experience top-notch sintering with Chairside Sintering Furnace with Transformer. Easy to operate, noise-free pallet, and automatic temperature calibration. Order now!
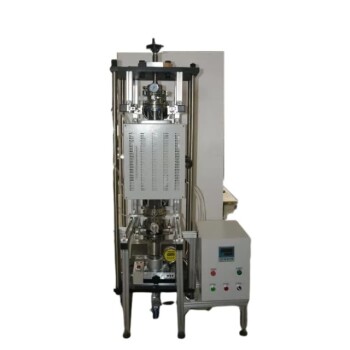
Vacuum Hot Press Furnace Heated Vacuum Press Machine Tube Furnace
Reduce forming pressure & shorten sintering time with Vacuum Tube Hot Press Furnace for high-density, fine-grain materials. Ideal for refractory metals.
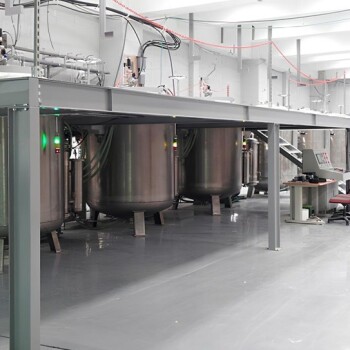
Graphite Vacuum Furnace Negative Material Graphitization Furnace
Graphitization furnace for battery production has uniform temperature and low energy consumption. Graphitization furnace for negative electrode materials: an efficient graphitization solution for battery production and advanced functions to enhance battery performance.
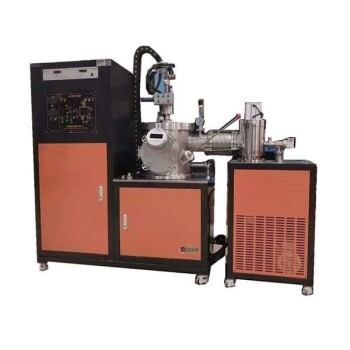
Vacuum Arc Induction Melting Furnace
Discover the power of Vacuum Arc Furnace for melting active & refractory metals. High-speed, remarkable degassing effect, and free of contamination. Learn more now!
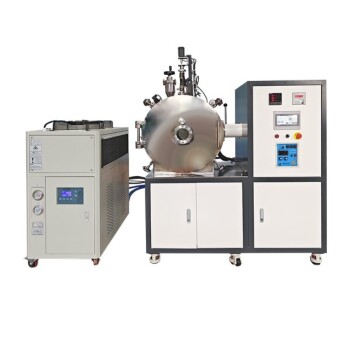
Lab-Scale Vacuum Induction Melting Furnace
Get precise alloy composition with our Vacuum Induction Melting Furnace. Ideal for aerospace, nuclear energy, and electronic industries. Order now for effective smelting and casting of metals and alloys.
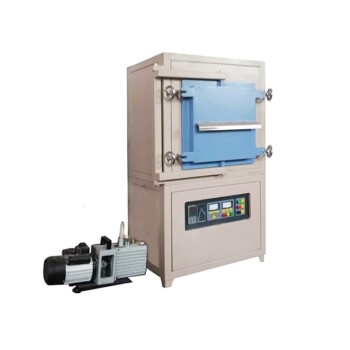
1700℃ Controlled Atmosphere Furnace Nitrogen Inert Atmosphere Furnace
KT-17A Controlled atmosphere furnace: 1700℃ heating, vacuum sealing technology, PID temperature control, and versatile TFT smart touch screen controller for laboratory and industrial use.
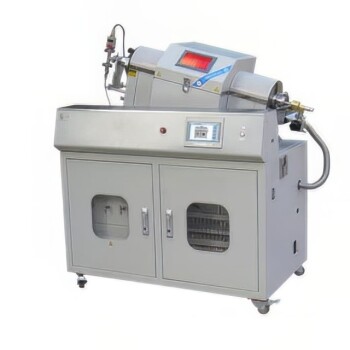
Inclined Rotary Plasma Enhanced Chemical Vapor Deposition PECVD Equipment Tube Furnace Machine
Introducing our inclined rotary PECVD furnace for precise thin film deposition. Enjoy automatic matching source, PID programmable temperature control, and high accuracy MFC mass flowmeter control. Built-in safety features for peace of mind.
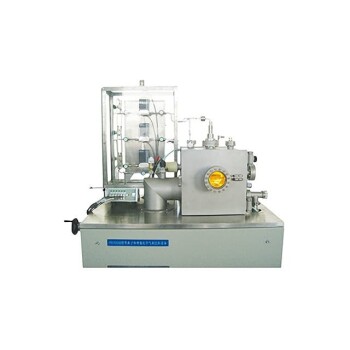
Inclined Rotary Plasma Enhanced Chemical Vapor Deposition PECVD Equipment Tube Furnace Machine
Upgrade your coating process with PECVD coating equipment. Ideal for LED, power semiconductors, MEMS and more. Deposits high-quality solid films at low temps.
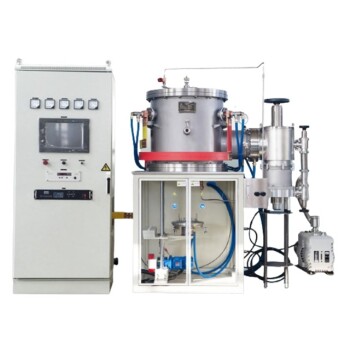
2200 ℃ Tungsten Vacuum Heat Treat and Sintering Furnace
Experience the ultimate refractory metal furnace with our Tungsten vacuum furnace. Capable of reaching 2200℃, perfect for sintering advanced ceramics and refractory metals. Order now for high-quality results.
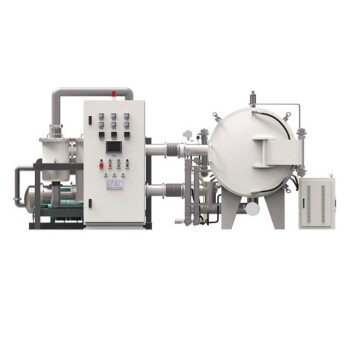
Horizontal High Temperature Graphite Vacuum Graphitization Furnace
Horizontal Graphitization Furnace: This type of furnace is designed with the heating elements placed horizontally, allowing for uniform heating of the sample. It's well-suited for graphitizing large or bulky samples that require precise temperature control and uniformity.
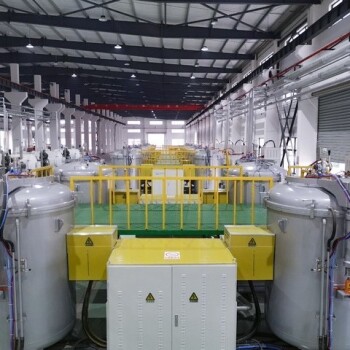
Vertical High Temperature Graphite Vacuum Graphitization Furnace
Vertical high temperature graphitization furnace for carbonization and graphitization of carbon materials up to 3100℃.Suitable for shaped graphitization of carbon fiber filaments and other materials sintered in a carbon environment.Applications in metallurgy, electronics, and aerospace for producing high-quality graphite products like electrodes and crucibles.
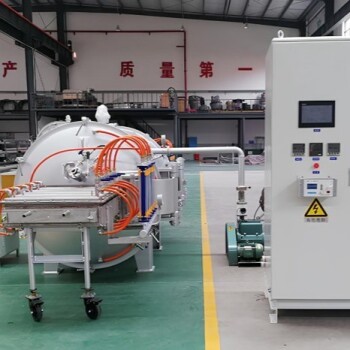
Graphite Vacuum Continuous Graphitization Furnace
High-temperature graphitization furnace is a professional equipment for graphitization treatment of carbon materials. It is a key equipment for the production of high-quality graphite products. It has high temperature, high efficiency and uniform heating. It is suitable for various high-temperature treatments and graphitization treatments. It is widely used in metallurgy, electronics, aerospace, etc. industry.
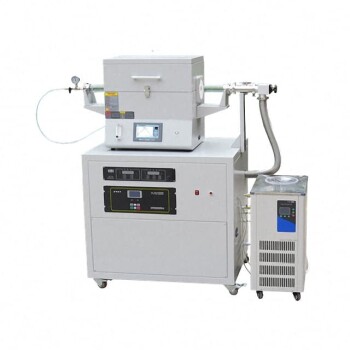
Efficient split chamber CVD furnace with vacuum station for intuitive sample checking and quick cooling. Up to 1200℃ max temperature with accurate MFC mass flowmeter control.
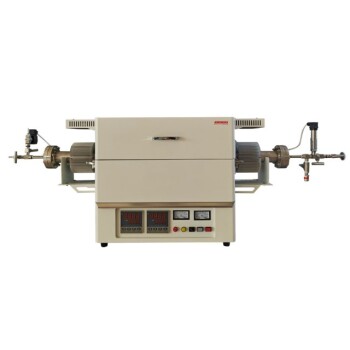
High Pressure Laboratory Vacuum Tube Furnace Quartz Tubular Furnace
KT-PTF High Pressure Tube Furnace: Compact split tube furnace with strong positive pressure resistance. Working temp up to 1100°C and pressure up to 15Mpa. Also works under controller atmosphere or high vacuum.
Related Articles
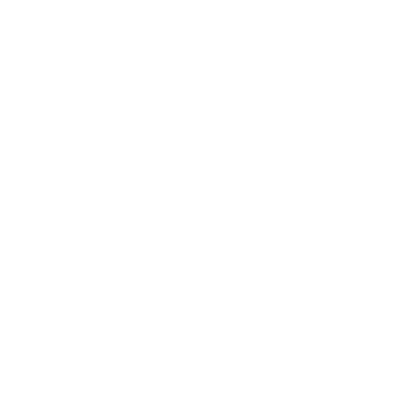
Spark Plasma Sintering Furnace: The Ultimate Guide to SPS Furnaces
Discover the world of Spark Plasma Sintering Furnaces (SPS). This comprehensive guide covers everything from its advantages and applications to its process and equipment. Learn how SPS furnaces can revolutionize your sintering operations.
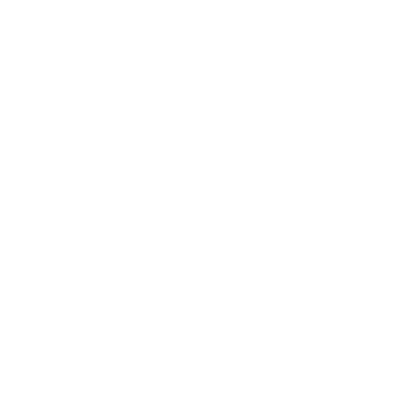
Exploring Spark Plasma Sintering Furnace (SPS): Technology, Applications, and Advantages
Dive into the comprehensive guide on Spark Plasma Sintering Furnace (SPS), covering its technology, applications in materials science, and significant advantages over traditional sintering methods.
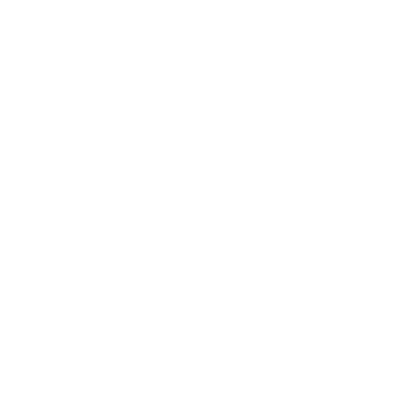
Exploring the Advanced Capabilities of Spark Plasma Sintering (SPS) Furnaces
Dive into the world of Spark Plasma Sintering (SPS) furnaces, their innovative technology, and applications in material science. Learn how SPS furnaces revolutionize the sintering process with high-speed, efficiency, and precision.
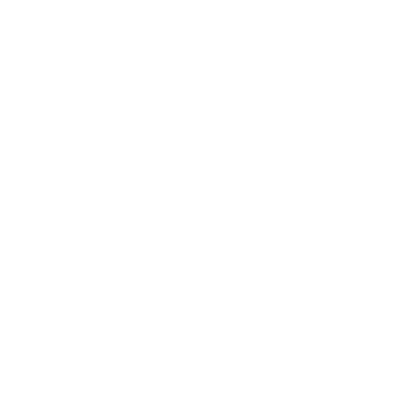
Comprehensive Guide to Spark Plasma Sintering Furnaces: Applications, Features, and Benefits
Explore the advanced features and applications of Spark Plasma Sintering Furnaces (SPS) in material science. Learn how SPS technology offers rapid, efficient, and versatile sintering for various materials.
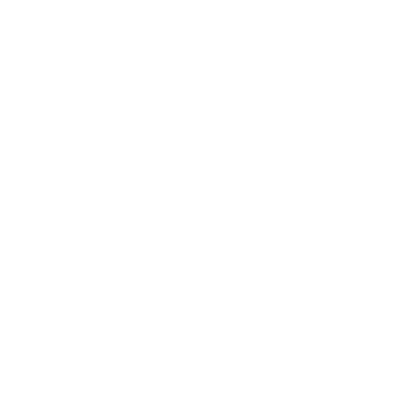
The Benefits of Controlled Atmosphere Furnaces for Sintering and Annealing Processes
They are essential in preventing oxidation, reducing the risk of contamination, and improving the properties of the materials being treated.
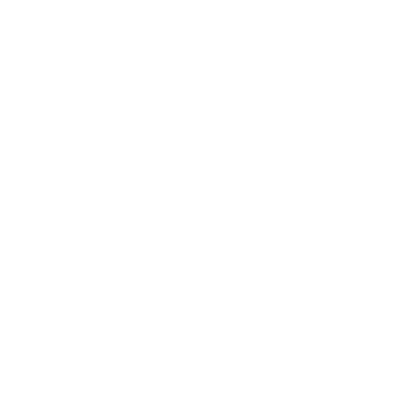
Understanding Saturated Calomel Reference Electrodes: Composition, Uses, and Considerations
Explore the detailed guide on saturated calomel reference electrodes, including their composition, advantages, disadvantages, and applications. Ideal for researchers and lab technicians.
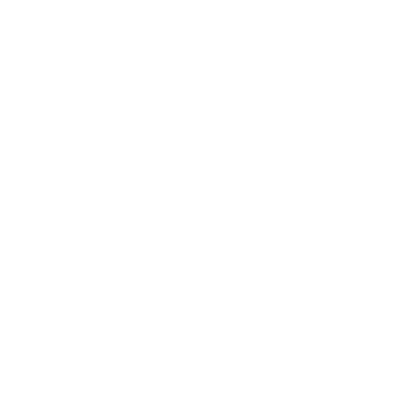
Dental Sintering Furnaces The Impact on Restoration Quality and Durability
Dental sintering furnaces play a crucial role in the manufacturing process of dental crowns and other restorations.
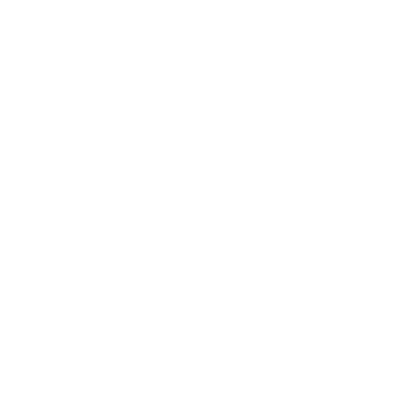
An In-depth Analysis of Hot Pressing Technology and Its Applications
Hot pressing is a high-pressure, low-strain-rate powder metallurgy process used to form powder or powder compact at high temperatures to induce sintering and creep processes. It involves the simultaneous application of heat and pressure to fabricate hard and brittle materials.
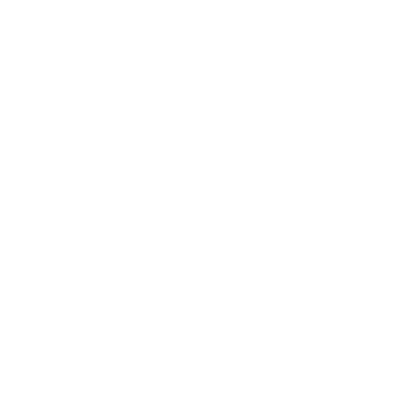
The Ultimate Guide to Vacuum Pressure Sintering Furnace: Benefits, Applications, and Working Principle
Discover the benefits, applications, and working principle of vacuum pressure sintering furnace. Learn how vacuum sintering produces clean, bright parts with incredible design flexibility and quick turnaround, and its applications in teaching, scientific research, and production. Explore the precise setting and monitoring of process parameters, and the advantages of sintering under vacuum and pressure. Find out how vacuum sintering furnace is perfect for higher temperature sintering applications and for sintering extremely reactive materials.
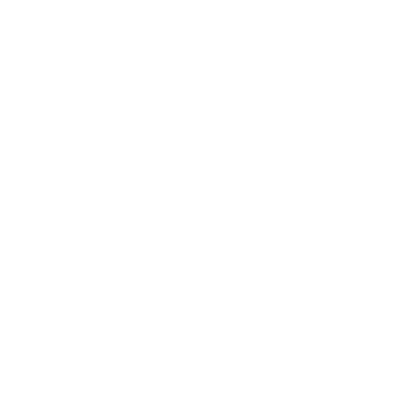
Understanding the PECVD Method
PECVD is a plasma-enhanced chemical vapor deposition process that is widely used in the production of thin films for various applications.
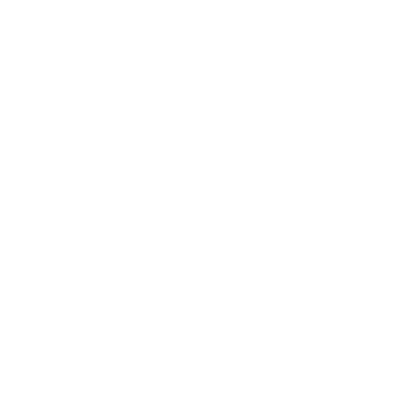
A Comparative Study of Evaporation and Sputtering Techniques in Thin Film Deposition
The two most common techniques used for thin film deposition are evaporation and sputtering.
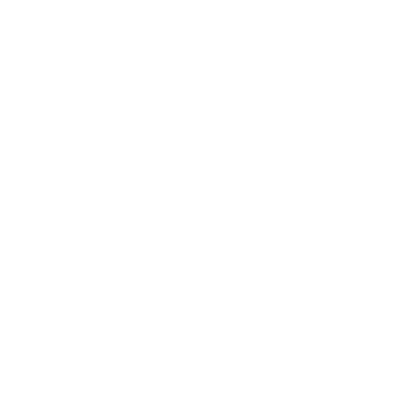
The Latest Advancements in Zirconia Sintering Furnaces for Dental Applications
Zirconia sintering furnaces are designed to give dental professionals the ability to create dental restorations with the highest level of precision and accuracy.